Hot isostatic pressing (HIP) is a manufacturing process that enhances material performance by applying high temperature and pressure simultaneously. This process is widely used to improve the density, ductility, and fatigue resistance of materials, particularly in cast, sintered, and additively manufactured parts. The typical temperature range for HIP varies depending on the material, but it generally operates between 900°C to 2,200°C (1,652°F to 3,992°F). The pressure range is commonly between 15,000 psi to 44,000 psi (100 MPa to 300 MPa). These conditions help in minimizing porosity, improving layer adhesion, and creating a uniform microstructure, which are critical for achieving high-quality parts.
Key Points Explained:
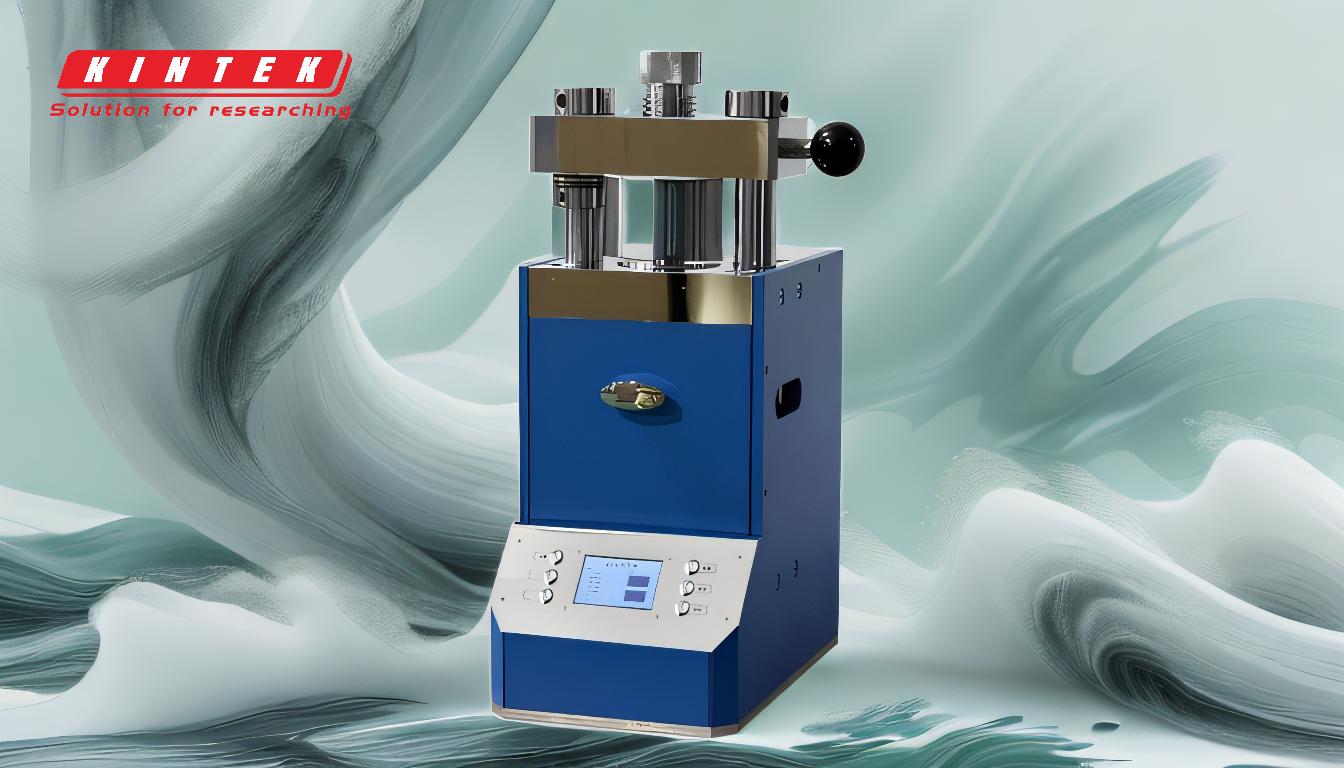
-
Temperature Range in Hot Isostatic Pressing:
- The temperature in HIP typically ranges from 900°C to 2,200°C (1,652°F to 3,992°F). This high temperature is necessary to facilitate the diffusion of atoms, which helps in densifying the material and eliminating internal voids or porosity.
- The exact temperature depends on the material being processed. For example, metals like titanium and nickel-based alloys require higher temperatures, while ceramics may require lower temperatures.
-
Pressure Range in Hot Isostatic Pressing:
- The pressure applied during HIP usually ranges from 15,000 psi to 44,000 psi (100 MPa to 300 MPa). This high pressure is applied uniformly from all directions, ensuring that the material is compressed evenly, leading to a high and uniform density.
- The pressure helps in closing pores and improving the mechanical properties of the material, such as strength, ductility, and fatigue resistance.
-
Benefits of Hot Isostatic Pressing:
- Improved Material Properties: HIP enhances the density, ductility, and fatigue resistance of materials. It also reduces internal stresses, which can lead to better performance in critical applications.
- Versatility: HIP can be used on a wide range of materials, including metals, ceramics, and composites. It is particularly useful for materials that are difficult to process using conventional methods.
- Complex Part Production: HIP allows for the production of complex shapes and large-sized components that would be challenging to manufacture using traditional methods.
-
Applications of Hot Isostatic Pressing:
- Aerospace: HIP is used to produce high-strength components for aerospace applications, where material performance is critical.
- Medical: In the medical field, HIP is used to manufacture implants and other components that require high precision and reliability.
- Additive Manufacturing: For 3D printed parts, HIP is used to address issues like porosity and poor layer adhesion, resulting in parts with a uniform microstructure and improved mechanical properties.
-
Comparison with Warm Isostatic Pressing:
- Warm Isostatic Pressing operates at lower temperatures compared to HIP, typically between 80°C to 200°C (176°F to 392°F). This process is used for materials that cannot withstand the high temperatures of HIP but still require the benefits of isostatic pressing.
- Warm isostatic pressing is particularly useful for powders, binders, and other materials that have special temperature requirements or cannot be molded at room temperature.
In summary, hot isostatic pressing is a powerful manufacturing process that combines high temperature and pressure to improve the properties of materials. The typical temperature range is 900°C to 2,200°C, and the pressure range is 15,000 psi to 44,000 psi. This process is essential for producing high-quality, complex parts in industries such as aerospace, medical, and additive manufacturing. For more information on related processes, you can explore warm isostatic press.
Summary Table:
Parameter | Range |
---|---|
Temperature | 900°C to 2,200°C (1,652°F–3,992°F) |
Pressure | 15,000 psi to 44,000 psi (100–300 MPa) |
Key Benefits | Improved density, ductility, fatigue resistance |
Applications | Aerospace, medical, additive manufacturing |
Ready to enhance your material performance with hot isostatic pressing? Contact us today for expert guidance!