The temperature limit for brazing is typically determined by the liquidus temperature of the braze alloy, which is the lowest temperature at which the alloy becomes fully liquid. The brazing temperature should be set at least 25ºC (50ºF) above this liquidus temperature to ensure proper flow and bonding of the alloy. However, the exact temperature can vary depending on the specific materials and alloys used in the brazing process. It is crucial to adhere to the recommended temperature range to avoid issues such as incomplete bonding or damage to the base materials.
Key Points Explained:
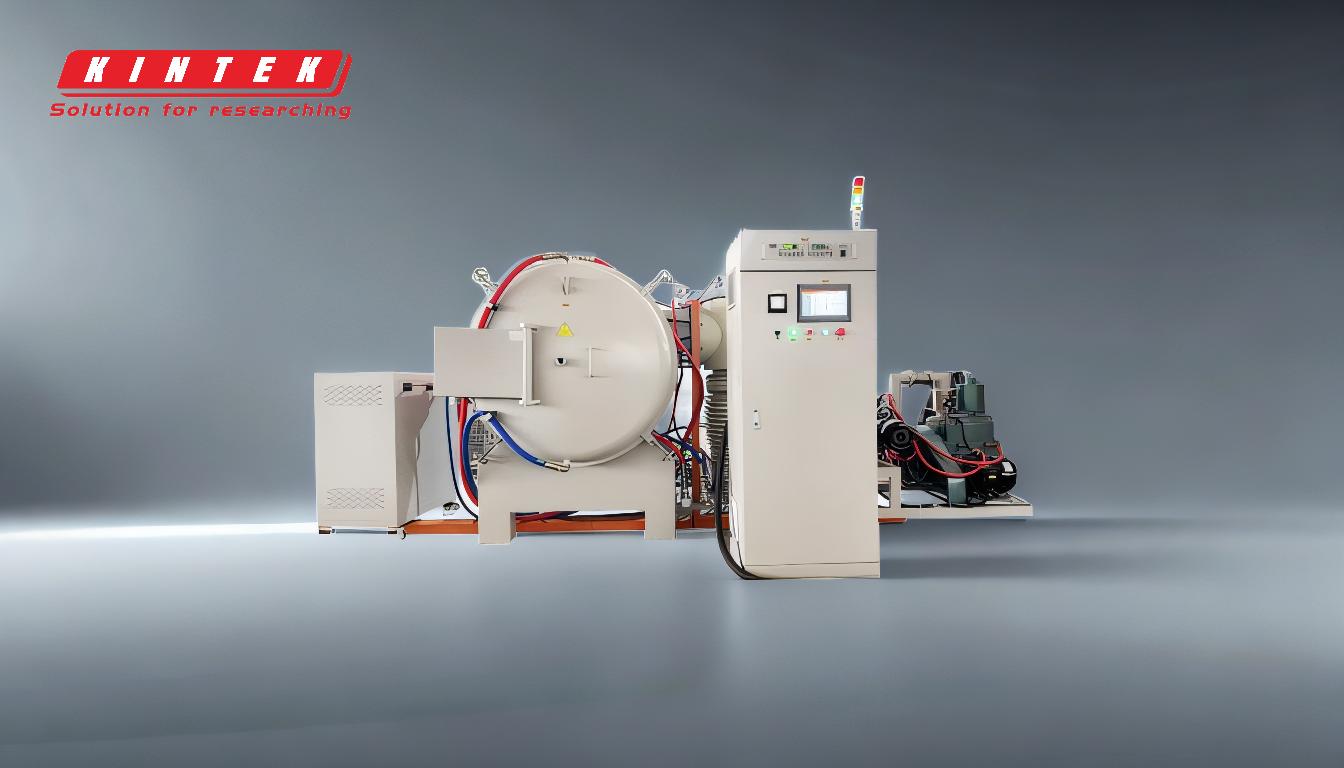
-
Liquidus Temperature:
- The liquidus temperature is the minimum temperature at which the braze alloy becomes completely liquid. This is a critical parameter because brazing requires the alloy to flow and fill the gaps between the base materials.
- The brazing temperature must exceed this liquidus temperature to ensure proper wetting and bonding.
-
Recommended Temperature Range:
- The brazing temperature should be set at least 25ºC (50ºF) above the liquidus temperature. This ensures that the alloy remains in a liquid state long enough to flow and form a strong joint.
- Operating within this range minimizes the risk of incomplete bonding or voids in the joint.
-
Material Considerations:
- The temperature limit also depends on the base materials being joined. Some materials, such as aluminum or certain steels, have specific temperature thresholds that must not be exceeded to avoid degradation or melting.
- The thermal expansion coefficients of the base materials and the braze alloy must also be considered to prevent stress or cracking during cooling.
-
Process Optimization:
- Using the lowest possible temperature within the recommended range helps conserve energy and reduces the risk of overheating the base materials.
- Proper temperature control is essential for achieving consistent and reliable brazed joints.
-
Alloy Selection:
- Different braze alloys have varying liquidus temperatures, so the choice of alloy directly impacts the brazing temperature. For example, silver-based alloys typically have lower liquidus temperatures compared to nickel-based alloys.
- The alloy must be compatible with the base materials and the intended application to ensure optimal performance.
-
Practical Implications:
- Exceeding the recommended temperature range can lead to issues such as excessive alloy flow, oxidation, or damage to the base materials.
- Conversely, operating below the liquidus temperature can result in poor joint formation and inadequate bonding.
By carefully selecting the appropriate braze alloy and adhering to the recommended temperature guidelines, manufacturers can achieve strong, durable, and reliable brazed joints.
Summary Table:
Key Factor | Details |
---|---|
Liquidus Temperature | Minimum temperature at which the braze alloy becomes fully liquid. |
Recommended Range | Set brazing temperature at least 25ºC (50ºF) above the liquidus temperature. |
Material Considerations | Base material properties and thermal expansion coefficients affect limits. |
Alloy Selection | Choose alloys with compatible liquidus temperatures for the application. |
Process Optimization | Use the lowest possible temperature within the range to conserve energy. |
Practical Implications | Exceeding or falling below the range can lead to bonding issues or damage. |
Need help determining the ideal brazing temperature for your project? Contact our experts today for tailored solutions!