Thermal debinding is a critical step in metal additive manufacturing, particularly in processes like Metal Injection Molding (MIM) or Binder Jetting. It involves the removal of polymer binders that are mixed with metal powders during the printing process. These binders are essential for shaping the part during printing but must be removed to prepare the part for sintering. The thermal debinding process typically occurs in a controlled environment, where the part is heated to specific temperatures to evaporate or decompose the binders without damaging the metal structure. This step ensures that the final sintered part achieves the desired mechanical properties and dimensional accuracy.
Key Points Explained:
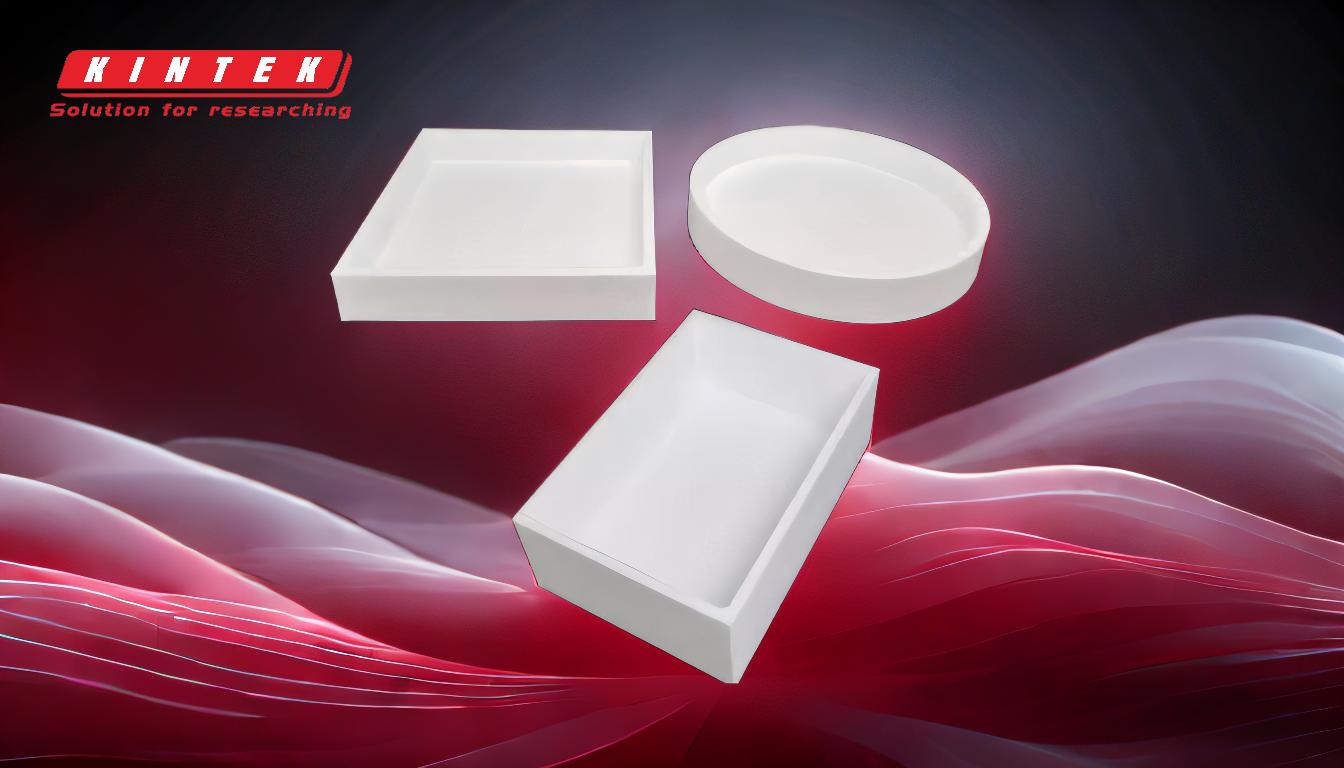
-
Purpose of Thermal Debinding:
- Thermal debinding is used to remove organic binders from a printed metal part. These binders are necessary during the printing process to hold the metal powder together and maintain the part's shape. However, they must be removed before sintering to avoid contamination and ensure the part's structural integrity.
-
Process Overview:
- The thermal debinding process involves heating the printed part in a controlled environment, often in a furnace. The temperature is gradually increased to allow the binders to evaporate or decompose. This process must be carefully controlled to prevent rapid gas formation, which could cause defects like cracking or bloating in the part.
-
Types of Binders:
- Binders used in metal additive manufacturing can be categorized into two types: primary binders and secondary binders. Primary binders are typically low-molecular-weight polymers that evaporate at lower temperatures, while secondary binders are higher-molecular-weight polymers that require higher temperatures to decompose. The thermal debinding process must account for the different evaporation or decomposition temperatures of these binders.
-
Temperature Control:
- Temperature control is crucial during thermal debinding. The process often involves multiple stages, starting at lower temperatures to remove the primary binders and gradually increasing to higher temperatures to remove the secondary binders. This staged approach helps prevent defects and ensures complete binder removal.
-
Environment:
- Thermal debinding is typically performed in an inert atmosphere, such as nitrogen or argon, or under vacuum conditions. This prevents oxidation of the metal powder and ensures that the binders are removed without leaving residues that could affect the final part's properties.
-
Equipment Used:
- The process is carried out in specialized furnaces designed for controlled heating and atmosphere management. These furnaces are equipped with precise temperature controls and gas flow systems to ensure uniform heating and binder removal.
-
Importance for Sintering:
- Thermal debinding is a preparatory step for sintering, where the metal particles are fused together to form a dense, solid part. Complete removal of binders is essential to achieve the desired density and mechanical properties during sintering. Any residual binders can lead to defects such as porosity or weak spots in the final part.
-
Challenges:
- One of the main challenges in thermal debinding is achieving uniform binder removal, especially in complex geometries or thick sections. Non-uniform debinding can lead to uneven shrinkage during sintering, resulting in warping or cracking of the part. Advanced debinding techniques, such as solvent debinding or catalytic debinding, are sometimes used in conjunction with thermal debinding to address these challenges.
-
Applications:
- Thermal debinding is widely used in industries that require high-precision metal parts, such as aerospace, automotive, and medical devices. It is an essential step in processes like Metal Injection Molding (MIM) and Binder Jetting, where the final part's mechanical properties and dimensional accuracy are critical.
By understanding the thermal debinding process, manufacturers can optimize their additive manufacturing workflows to produce high-quality metal parts with the desired properties. This process, while complex, is essential for ensuring the success of subsequent steps like sintering and achieving the final part's performance requirements.
Summary Table:
Aspect | Details |
---|---|
Purpose | Removes organic binders from printed metal parts to prepare for sintering. |
Process | Heating in a controlled environment to evaporate or decompose binders. |
Types of Binders | Primary (low-molecular-weight) and secondary (high-molecular-weight). |
Temperature Control | Staged heating to prevent defects and ensure complete binder removal. |
Environment | Inert atmosphere (nitrogen/argon) or vacuum to prevent oxidation. |
Equipment | Specialized furnaces with precise temperature and gas flow controls. |
Importance for Sintering | Ensures final part density and mechanical properties. |
Challenges | Uniform binder removal in complex geometries to prevent defects. |
Applications | Aerospace, automotive, and medical industries requiring precision parts. |
Optimize your metal additive manufacturing process with expert thermal debinding solutions—contact us today!