Vacuum deposition of metals is a sophisticated process used to deposit thin layers of material onto a substrate in a controlled vacuum environment. This technique is essential for creating precise, high-quality coatings with applications ranging from optical and decorative coatings to functional layers in electronics and industrial components. The process involves depositing material atom-by-atom or molecule-by-molecule, allowing for the creation of films as thin as a single atom or as thick as several millimeters. Vacuum deposition is widely used in industries such as aerospace, automotive, medical, and electronics due to its ability to produce coatings with specific properties like durability, conductivity, and corrosion resistance.
Key Points Explained:
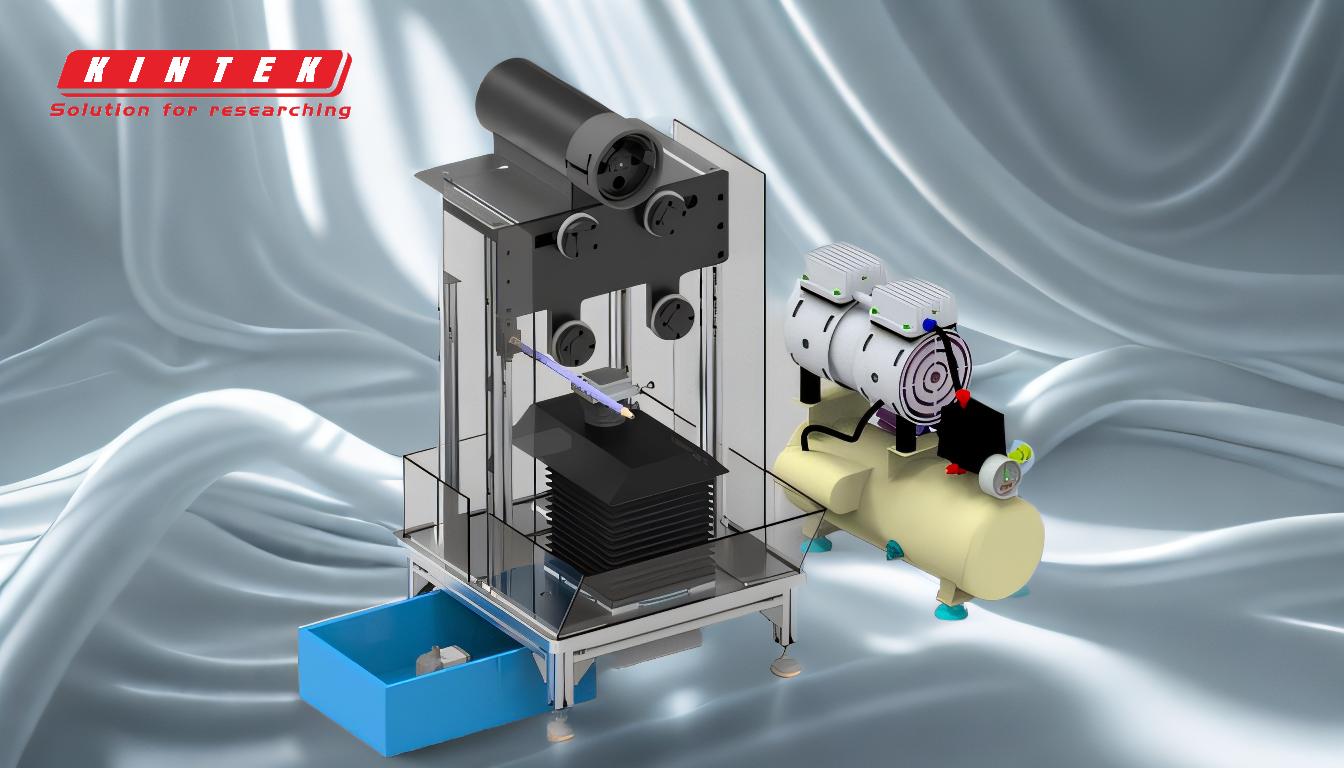
-
Definition and Process of Vacuum Deposition:
- Vacuum deposition is a family of processes that deposit thin layers of material onto a substrate in a high-vacuum environment.
- The process involves depositing material atom-by-atom or molecule-by-molecule, ensuring precise control over the thickness and quality of the coating.
- Common techniques include Physical Vapor Deposition (PVD) and Low-Pressure Chemical Vapor Deposition (LPCVD).
-
Applications of Vacuum Deposition:
- Optical Coatings: Used to create interference coatings, mirror coatings, and anti-reflective layers for lenses and optical devices.
- Decorative Coatings: Applied to surfaces for aesthetic purposes, such as on automotive parts or consumer electronics.
- Functional Coatings: Includes wear-resistant, corrosion-protective, and electrically conductive coatings for industrial and aerospace components.
- Energy and Electronics: Used in thin-film solar cells, microchips, LEDs, and flexible displays to enhance performance and durability.
-
Materials and Substrates:
- Vacuum deposition can be applied to a variety of materials, including glass, metal, and plastics.
- Common substrates include optical lenses, engine components, and flexible packaging materials.
- The process is versatile, allowing for the deposition of metals, ceramics, and polymers.
-
Advantages of Vacuum Deposition:
- Precision: Allows for the deposition of extremely thin and uniform layers, even at the nanometer scale.
- Clean Environment: The high-vacuum environment minimizes contamination, resulting in high-purity coatings.
- Versatility: Suitable for a wide range of materials and applications, from decorative to highly functional coatings.
- Durability: Coatings produced through vacuum deposition are often more durable and resistant to wear, corrosion, and environmental factors.
-
Industrial and Commercial Use Cases:
- Aerospace: Used for protective coatings on aircraft components to enhance durability and resistance to extreme conditions.
- Automotive: Applied to carbon fiber composites and engine parts for improved performance and aesthetics.
- Medical: Used for biocompatible coatings on medical devices and implants.
- Consumer Electronics: Essential for manufacturing microchips, LEDs, and flexible displays.
-
Future Trends and Innovations:
- Thin-Film Solar Cells: Continued advancements in vacuum deposition are improving the efficiency and durability of solar cells.
- Flexible Electronics: The development of thin-film transistors and sensors for flexible displays and wearable devices is a growing application.
- Sustainable Manufacturing: Efforts are being made to reduce the environmental impact of vacuum deposition processes, such as using greener materials and energy-efficient systems.
By understanding these key points, equipment and consumable purchasers can better appreciate the value of vacuum deposition in various industries and make informed decisions about its application in their specific use cases.
Summary Table:
Aspect | Details |
---|---|
Definition | Deposits thin layers of material atom-by-atom in a vacuum environment. |
Techniques | Includes PVD and LPCVD for precise, high-quality coatings. |
Applications | Optical, decorative, functional coatings, and energy/electronics industries. |
Materials | Glass, metal, plastics, ceramics, and polymers. |
Advantages | Precision, clean environment, versatility, and durability. |
Use Cases | Aerospace, automotive, medical, and consumer electronics. |
Future Trends | Thin-film solar cells, flexible electronics, and sustainable manufacturing. |
Ready to enhance your coatings with vacuum deposition? Contact our experts today for tailored solutions!