Vacuum furnaces are the most effective type of furnace for removing air to prevent decarburization. By creating a vacuum environment, these furnaces eliminate exposure to oxygen and other reactive gases, which are the primary causes of decarburization and oxidation during heat treatment processes. This ensures that the workpiece retains its carbon content and surface integrity, making vacuum furnaces ideal for applications requiring precise material properties and minimal surface degradation.
Key Points Explained:
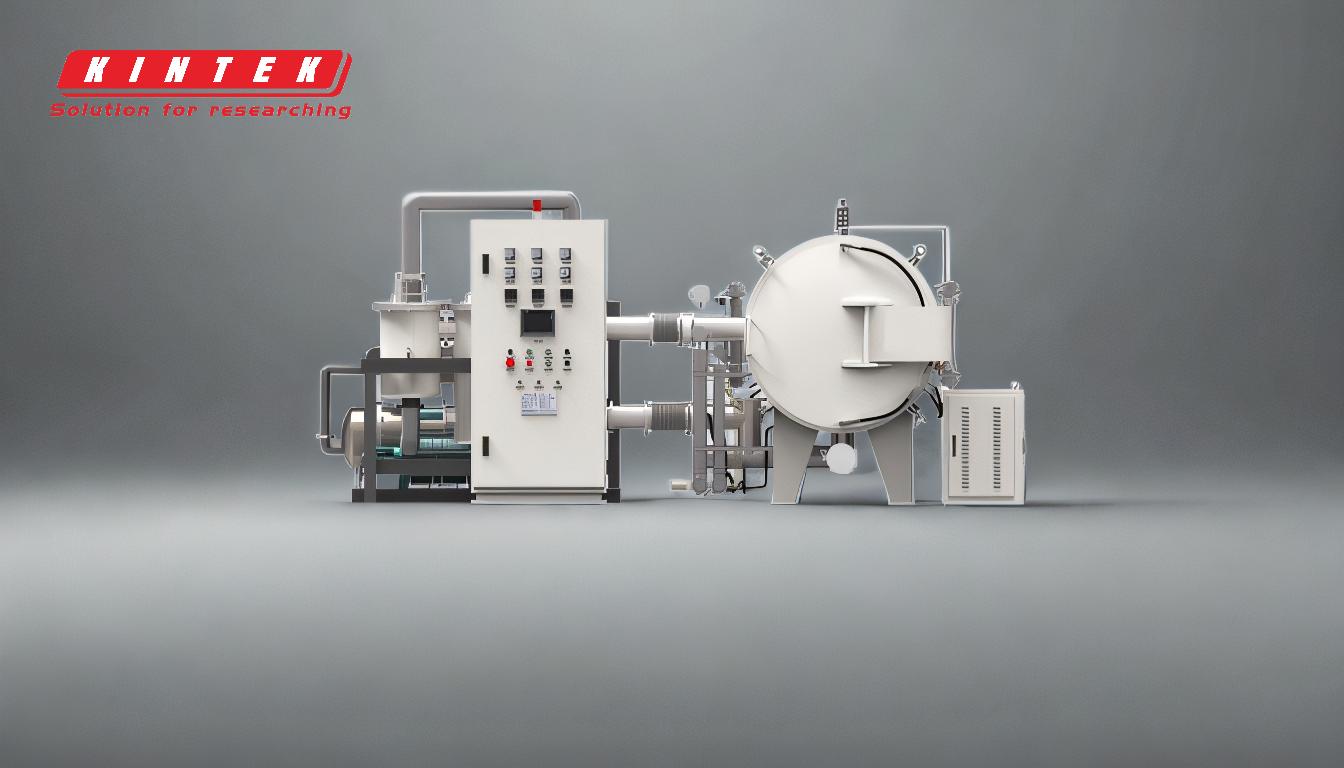
-
Vacuum Furnaces and Air Removal:
- Vacuum furnaces operate by removing air from the heating chamber, creating a near-perfect vacuum environment.
- This absence of air prevents oxidation and decarburization, as there is no oxygen or reactive gases to react with the workpiece.
-
Decarburization Prevention:
- Decarburization occurs when carbon is lost from the surface of a metal due to exposure to oxygen or other reactive gases at high temperatures.
- In a vacuum furnace, the lack of air ensures that the carbon content of the workpiece remains intact, preserving its mechanical properties.
-
Surface Oxidation Minimization:
- Surface oxidation is another common issue in heat treatment processes, leading to scaling and surface degradation.
- Vacuum furnaces eliminate this problem by preventing any exposure to oxygen, ensuring a clean and oxidation-free surface.
-
Applications of Vacuum Furnaces:
- Vacuum furnaces are widely used in industries where material integrity is critical, such as aerospace, automotive, and tool manufacturing.
- They are particularly beneficial for heat treating high-alloy steels, titanium alloys, and other materials that are prone to oxidation and decarburization.
-
Comparison with Other Furnace Types:
- Household Furnaces: These are designed for general heating purposes and do not provide the controlled environment needed to prevent decarburization.
- Industrial Furnaces: While some industrial furnaces can control the atmosphere to some extent, they often rely on protective gases rather than a complete vacuum, which may not be as effective.
- Laboratory Furnaces: These are used for research and small-scale applications but may not always offer the same level of air removal as vacuum furnaces.
-
Advantages of Vacuum Furnaces:
- Precision: Vacuum furnaces offer precise control over the heating environment, ensuring consistent results.
- Cleanliness: The absence of air and reactive gases results in a cleaner heat treatment process, with minimal surface contamination.
- Material Integrity: By preventing decarburization and oxidation, vacuum furnaces help maintain the mechanical and chemical properties of the treated materials.
-
Limitations of Vacuum Furnaces:
- Cost: Vacuum furnaces are generally more expensive to purchase and operate compared to other types of furnaces.
- Complexity: The need for a vacuum system adds complexity to the furnace design and maintenance.
- Size Limitations: Vacuum furnaces are typically smaller in size compared to some industrial furnaces, which may limit their use for large-scale applications.
-
Conclusion:
- Vacuum furnaces are the best choice for applications where preventing decarburization and oxidation is critical. Their ability to create a vacuum environment ensures that the workpiece is heated without exposure to air, preserving its carbon content and surface quality. While they may be more costly and complex, the benefits they offer in terms of material integrity and precision make them indispensable in many high-tech industries.
Summary Table:
Key Feature | Description |
---|---|
Air Removal | Creates a near-perfect vacuum to eliminate oxygen and reactive gases. |
Decarburization Prevention | Preserves carbon content by preventing exposure to air. |
Oxidation Minimization | Ensures a clean, oxidation-free surface during heat treatment. |
Applications | Ideal for aerospace, automotive, and tool manufacturing industries. |
Advantages | Precision, cleanliness, and material integrity. |
Limitations | Higher cost, complexity, and size constraints. |
Learn how vacuum furnaces can enhance your heat treatment processes—contact us today!