Introduction
Table of Contents
Cold Isostatic Pressing (CIP) is a fascinating process that offers numerous benefits in the field of ceramic manufacturing. By understanding this process, you can gain valuable insights into how it can improve your business operations. CIP involves the use of a high-pressure pump to generate isotropic uniform pressure on a ceramic material. The resulting uniform pressure distribution leads to enhanced density and high strength of the final product. In this blog post, we will explore the process and advantages of CIP, as well as its cost efficiency, making it an ideal choice for businesses looking to produce high-quality ceramic products.
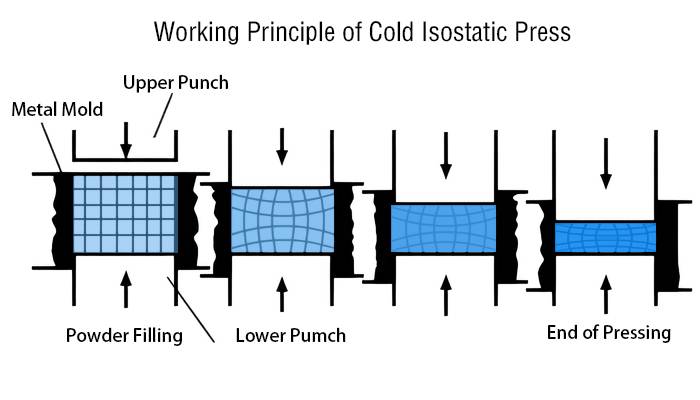
Description of Cold Isostatic Pressing
Understanding the process of isostatic pressing (CIP)
Cold Isostatic Pressing (CIP) is a method of processing materials that involves compacting powders by enclosing them in an elastomer mold. The process is based on Pascal's law, which states that pressure applied in an enclosed fluid is transmitted in all directions without any change in magnitude.
Role of static pressure produced by fluid or gas
During CIP, static pressure is produced by a fluid or gas, such as oil or water, which is used as the medium for applying pressure to the mold. The pressure is evenly distributed across the material, helping to reduce distortion, improve accuracy, and minimize the risk of air entrapment and voids.

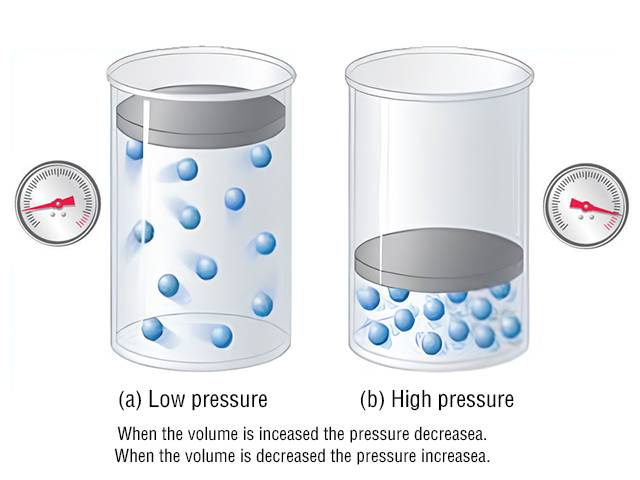
Use of a high-pressure pump in the process
To achieve the necessary pressure for CIP, a high-pressure pump is used to generate the required fluid pressure. This pump applies pressure typically ranging from 60,000 lbs/in² (400 MPa) to 150,000 lbs/in² (1000 MPa), depending on the specific application.
Resulting isotropic uniform pressure during pressing
The application of fluid pressure during CIP ensures that the pressure is transmitted uniformly in all directions throughout the material. This results in an isotropic uniform pressure, which helps to achieve a highly compact solid at the end of the process.
CIP is a versatile method that can be used for a variety of materials, including plastics, graphite, powdered metallurgy, ceramics, and sputtering targets. It is widely utilized in industries such as medical, aerospace, and automotive for the production of components with improved accuracy and strength.
Cold isostatic pressing is an effective technique for shaping and compacting powders into components of varying sizes and shapes. Its use of fluid pressure ensures uniformity and reduces the risk of defects. With its versatility and wide range of applications, CIP is a valuable process in various industries.
Applications of Isostatic Pressing Technology
Production of new alloy products
Isostatic pressing technology can be used to produce new alloy products that are difficult to produce using traditional casting methods. This process applies uniform pressure from all directions, allowing for the formation of complex shapes, including concave, hollow, and slender parts. The uniform pressure distribution results in a high-density distribution and increased strength of the final product. Additionally, isostatic pressing offers the advantage of lower mold costs compared to other forming processes.
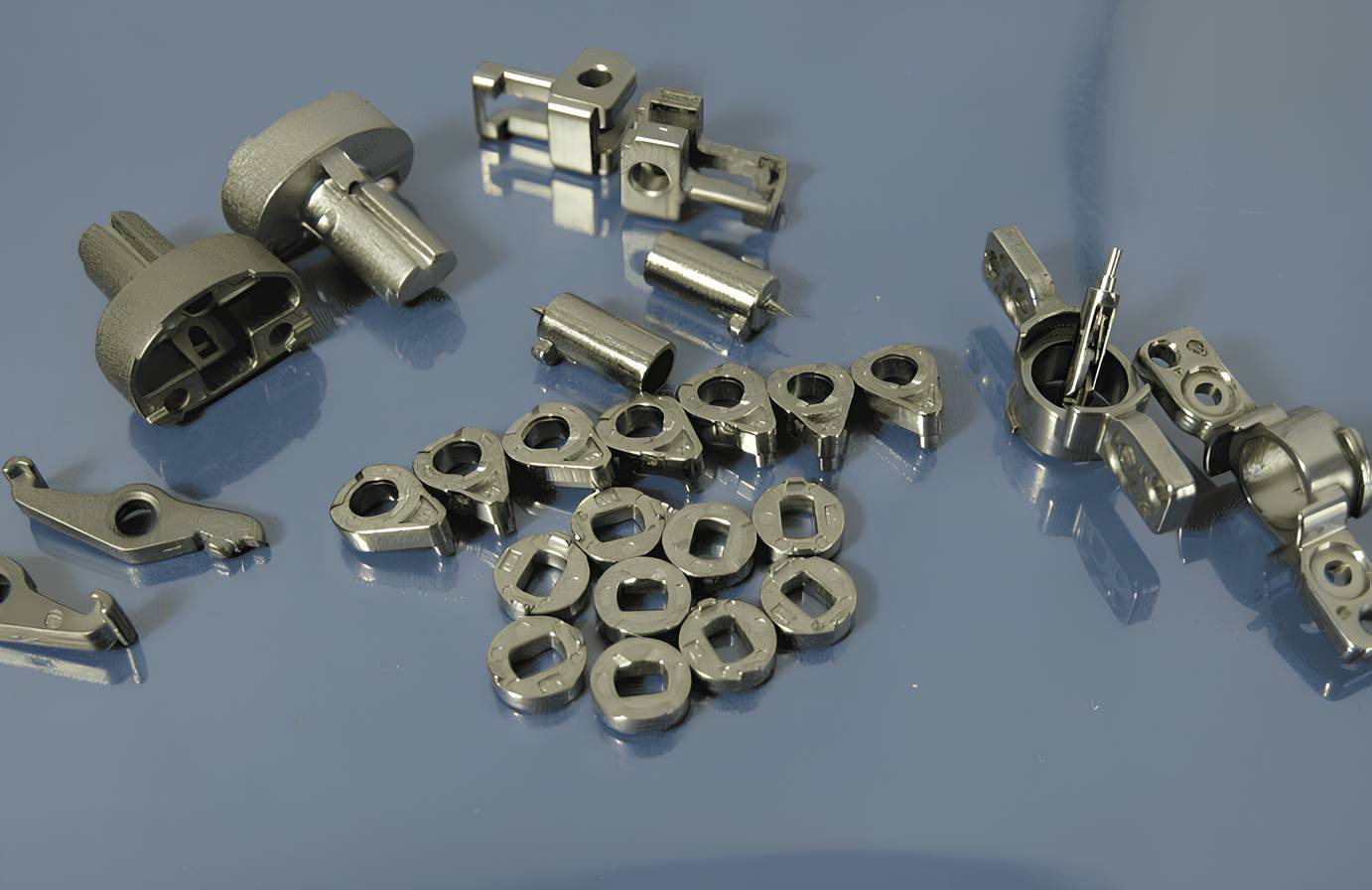
Forming process for zirconia ceramic and alumina ceramic products
Isostatic pressing is an ideal forming process for zirconia ceramic products and alumina ceramic products that require high performance and strength. This technique, also known as cold isostatic pressing (CIP), applies uniform pressure to the powder or blank using fluid or gas. It allows for the production of parts with precise dimensions and complex shapes, including those with concave or slender features. Isostatic pressing also offers the benefits of low friction loss and low forming pressure.
The isostatic pressing process has been widely adopted across various industries, including pharmaceuticals, explosives, chemicals, food, and nuclear fuel production. It is suitable for materials such as ceramics, metals, composites, plastics, and carbon. Isostatic pressing provides a cost-effective solution for consolidating powders and healing defects in castings. Furthermore, its ability to apply uniform pressure to products of any shape or size makes it particularly advantageous for ceramic and refractory applications, reducing the need for costly machining.
In summary, isostatic pressing technology offers numerous benefits for the production of new alloy products and the forming of zirconia ceramic and alumina ceramic products. Its ability to apply uniform pressure from all directions ensures high density and strength, while also allowing for the formation of complex shapes. This versatile technique has found applications across various industries and has become a valuable production tool.
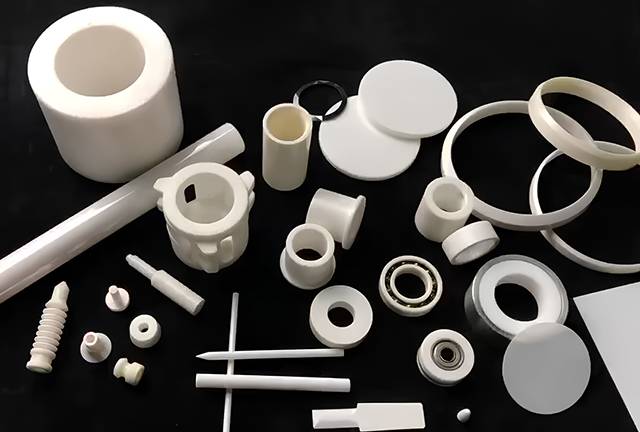
Advantages of Isostatic Pressing
Isostatic pressing offers several advantages over other production methods such as die compaction, extrusion, slip casting, and injection molding. These advantages include:
Capability to press parts with complex shapes
Isostatic pressing allows for the production of parts with intricate and complex shapes that are difficult or even impossible to achieve using other methods. This flexibility in shape allows for more design possibilities and innovation in product development.
Low friction loss and low forming pressure
Unlike other forming methods, isostatic pressing does not require the use of lubricants. This results in low friction loss during the pressing process. Additionally, the forming pressure required for isostatic pressing is lower compared to other methods, reducing the risk of material deformation or damage.
Uniform pressure distribution leading to uniform density and high billet strength
In isostatic pressing, the powder is compacted with the same pressure from all directions. This uniform pressure distribution ensures that the resulting compacted piece has a uniform density. This uniform density leads to consistent shrinkage during sintering or hot isostatic pressing, minimizing warping or distortion. Moreover, the high billet strength achieved through isostatic pressing ensures the durability and performance of the final product.
Isostatic pressing also offers other advantages such as:
-
Shape flexibility: Isostatic pressing allows for the production of shapes and dimensions that are difficult to achieve using other methods. It enables the fabrication of parts with internal shapes, threads, splines, serrations, and tapers.
-
Component size: Isostatic pressing can be used to produce a wide range of component sizes, from massive near-net PM shapes to small MIM parts.
-
Low tooling cost: Isostatic pressing has lower tooling costs compared to other manufacturing methods, making it more economical for short production runs.
-
Enhanced alloying possibilities: Isostatic pressing allows for the enhancement of alloying elements without inducing segregation in the material, resulting in improved material properties.
-
Reduced lead times: Isostatic pressing enables the economic production of complex shapes from prototype to production quantities, significantly reducing lead times compared to traditional methods like forgings or machined components.
-
Material and machining costs: Near-net shape parts produced through isostatic pressing reduce material and machining costs, making it a cost-effective manufacturing option.
In conclusion, the advantages of isostatic pressing make it a versatile and efficient production method for parts with complex shapes, ensuring uniform density and high strength. Its flexibility, cost-effectiveness, and ability to work with a wide range of materials make it an attractive option for various industries.
Cost Efficiency of Isostatic Pressing
Lower Mold Cost
Isostatic pressing is a method commonly used to achieve high compact densities and access shapes that cannot be compacted in uniaxial presses. When it comes to cost efficiency, one advantage of isostatic pressing is the lower mold cost compared to other methods.
In hot isostatic pressing, the tooling cost and complexity of the process are higher than for uniaxial pressing. However, isostatic pressing allows for somewhat complex shapes to be engineered into elastomeric molds if desired. This means that even with the higher tooling cost, the flexibility in mold design can result in cost savings in certain cases.
On the other hand, cold isostatic pressing can achieve more uniform densities due to minimized friction effects. While pressure vessels used in this method are typically limited to pressures of 415 MPa (60 ksi), the lower mold cost makes it an attractive option for cost-conscious businesses. Additionally, cold isostatic pressing can be automated, although the production rates are lower compared to die pressing.
It's important to note that the cost efficiency of isostatic pressing may vary depending on the specific requirements of the project. Factors such as desired shape, part size, and production volume will influence the overall cost. Therefore, it's advisable to consult with experts in the field to determine the most cost-effective approach for your specific needs.
Overall, isostatic pressing offers cost efficiency advantages, particularly in terms of lower mold cost. By considering the unique characteristics of isostatic pressing and comparing them to other methods, businesses can make informed decisions to optimize cost-efficiency in their manufacturing processes.
Conclusion
In conclusion, the process of zirconia ceramic cold isostatic pressing offers numerous benefits and applications for businesses. By understanding the process of isostatic pressing and the role of static pressure, companies can effectively produce new alloy products and form zirconia ceramic and alumina ceramic products. The advantages of isostatic pressing, including the capability to press parts with complex shapes, low friction loss, and uniform pressure distribution, result in uniform density and high billet strength. Moreover, isostatic pressing proves to be cost-efficient with lower mold costs. Overall, incorporating isostatic pressing technology can greatly enhance productivity and quality in various industries.
CONTACT US FOR A FREE CONSULTATION
KINTEK LAB SOLUTION's products and services have been recognized by customers around the world. Our staff will be happy to assist with any inquiry you might have. Contact us for a free consultation and talk to a product specialist to find the most suitable solution for your application needs!