Carbon nanotubes (CNTs) can indeed be used as catalyst supports due to their unique structural, electrical, and mechanical properties. Their high surface area, excellent conductivity, and chemical stability make them an ideal candidate for supporting catalytic materials. CNTs can enhance the dispersion and stability of catalysts, improve electron transfer during reactions, and provide a robust framework for various catalytic processes. This makes them particularly useful in applications such as fuel cells, hydrogen production, and environmental remediation. However, challenges such as cost, scalability, and functionalization methods need to be addressed to fully leverage their potential in industrial applications.
Key Points Explained:
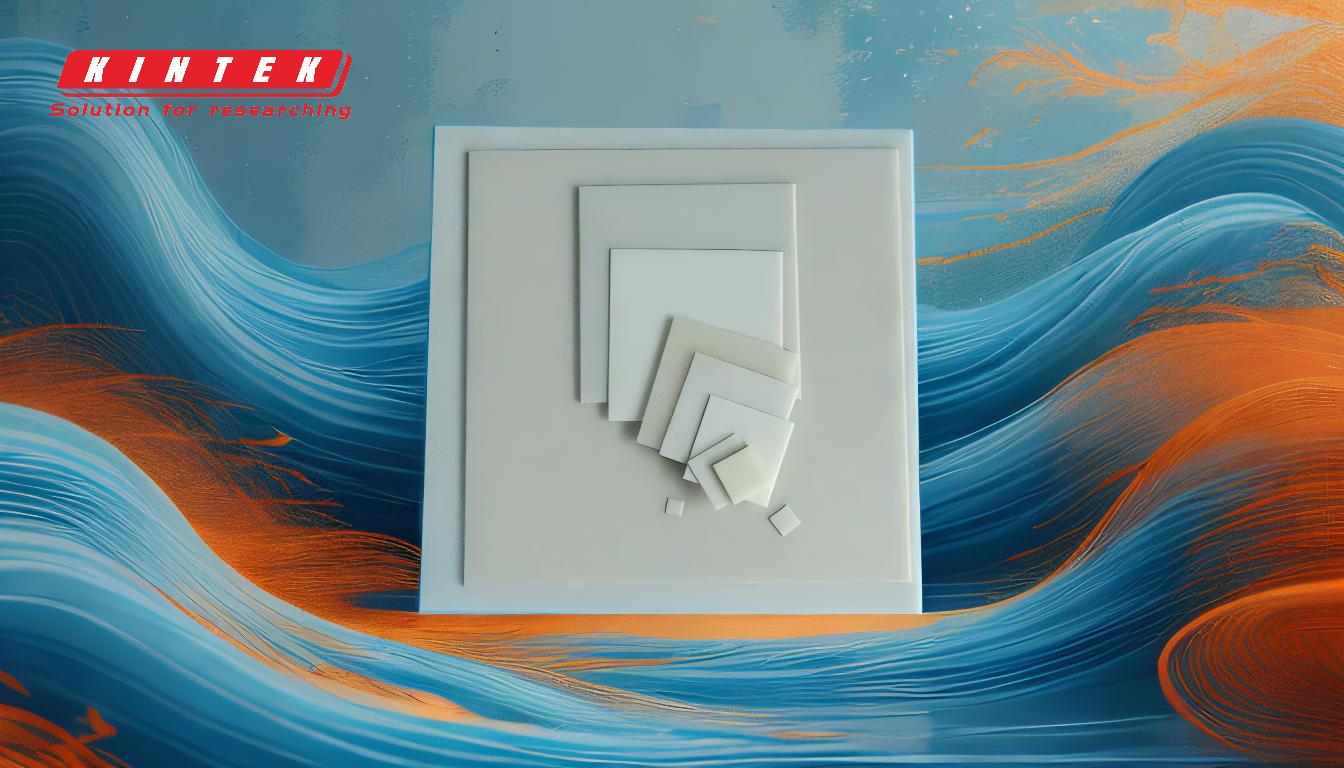
-
High Surface Area and Porosity:
- Carbon nanotubes possess a high surface area and porous structure, which allows for efficient dispersion of catalytic nanoparticles. This maximizes the active sites available for chemical reactions, enhancing the overall catalytic efficiency.
- The nanoscale dimensions of CNTs enable uniform distribution of catalysts, reducing agglomeration and improving performance.
-
Electrical Conductivity:
- CNTs are highly conductive, which facilitates electron transfer during catalytic reactions. This is particularly beneficial in electrochemical processes such as oxygen reduction reactions in fuel cells.
- The conductivity of CNTs can also help in stabilizing reactive intermediates, improving the reaction kinetics.
-
Chemical and Thermal Stability:
- Carbon nanotubes exhibit excellent chemical and thermal stability, making them suitable for use in harsh reaction environments. They can withstand high temperatures and corrosive conditions without significant degradation.
- This stability ensures the longevity and durability of the catalyst-support system, reducing the need for frequent replacements.
-
Functionalization and Surface Modification:
- The surface of CNTs can be chemically modified to introduce functional groups that enhance the binding of catalytic nanoparticles. This improves the adhesion and dispersion of the catalyst, leading to better performance.
- Functionalization can also tailor the surface properties of CNTs to specific reactions, increasing their versatility as catalyst supports.
-
Applications in Various Catalytic Processes:
- Fuel Cells: CNTs are used as supports for platinum and other noble metal catalysts in proton exchange membrane fuel cells (PEMFCs). They enhance the durability and activity of the catalysts, improving the efficiency of the fuel cells.
- Hydrogen Production: In water splitting reactions, CNTs support catalysts that facilitate hydrogen evolution, making them crucial for clean energy production.
- Environmental Remediation: CNTs are employed in catalytic processes for the degradation of pollutants and the removal of harmful substances from the environment.
-
Challenges and Limitations:
- Cost: The production of high-quality CNTs is still relatively expensive, which limits their widespread use in industrial applications.
- Scalability: Scaling up the synthesis and functionalization of CNTs for large-scale catalytic processes remains a challenge.
- Functionalization Techniques: Developing cost-effective and efficient methods for functionalizing CNTs without compromising their properties is an ongoing area of research.
-
Future Prospects:
- Advances in nanotechnology and materials science are expected to address the current limitations of CNTs, making them more accessible and cost-effective for industrial use.
- Research is focused on developing hybrid materials that combine CNTs with other nanomaterials to further enhance their catalytic properties.
- The integration of CNTs into sustainable and green chemistry practices is likely to expand their role in future catalytic applications.
In conclusion, carbon nanotubes offer significant advantages as catalyst supports due to their unique properties. While challenges remain, ongoing research and development are paving the way for their increased adoption in various catalytic processes.
Summary Table:
Property | Benefit |
---|---|
High Surface Area & Porosity | Maximizes active sites, improves dispersion, and reduces agglomeration. |
Electrical Conductivity | Enhances electron transfer, stabilizes intermediates, and improves kinetics. |
Chemical & Thermal Stability | Withstands harsh environments, ensuring durability and longevity. |
Functionalization | Tailors surface properties for specific reactions, improving performance. |
Applications | Fuel cells, hydrogen production, and environmental remediation. |
Discover how carbon nanotubes can revolutionize your catalytic processes—contact us today for expert advice!