Electric resistance heating is often touted as being 100% energy efficient because it converts all incoming electrical energy into heat. However, this statement requires a deeper understanding of what "efficiency" means in this context. While it is true that nearly all the electrical energy is converted to heat, the overall efficiency depends on factors such as the source of the electricity, energy losses during transmission, and the cost-effectiveness compared to other heating methods. This answer will explore the nuances of electric resistance heating efficiency and its practical implications.
Key Points Explained:
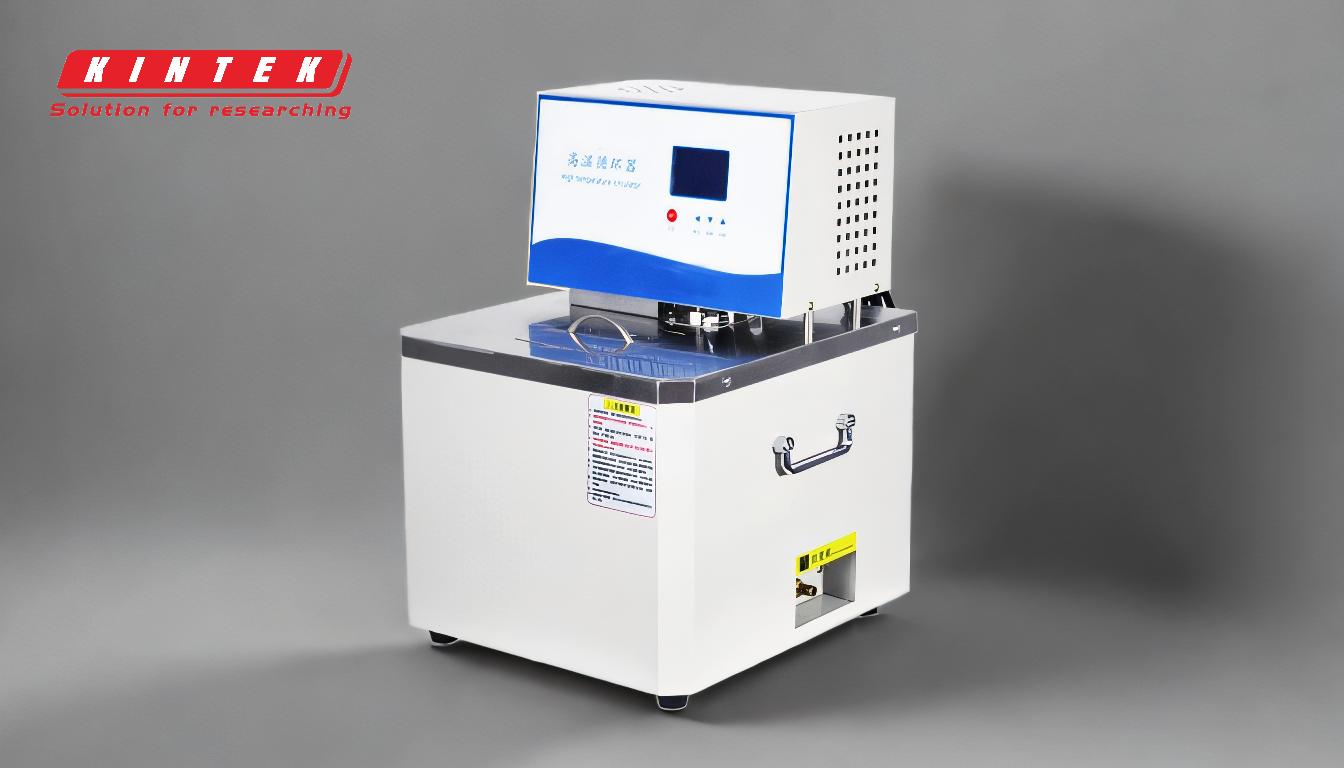
-
Understanding Efficiency in Electric Resistance Heating
- Electric resistance heating is considered 100% efficient because all the electrical energy is converted into heat within the heating element. This is due to the principle of Joule heating, where electrical resistance generates heat as current flows through the material.
- However, this efficiency is limited to the point of use. It does not account for the energy losses that occur during electricity generation and transmission from power plants to homes or businesses.
-
Energy Losses in Electricity Generation and Transmission
- The efficiency of electric resistance heating drops when considering the entire energy supply chain. Most electricity is generated in power plants, which often operate at efficiencies of 30-50% for fossil fuel-based plants and slightly higher for combined-cycle natural gas plants.
- Additionally, energy is lost during transmission and distribution due to resistance in power lines, which can reduce overall system efficiency by another 5-10%.
-
Comparison with Other Heating Methods
- Electric resistance heating is less efficient than heat pumps, which can achieve efficiencies of 200-300% by transferring heat rather than generating it. Heat pumps use electricity to move heat from a cooler space to a warmer one, making them more energy-efficient in moderate climates.
- In contrast, combustion-based heating systems (e.g., natural gas furnaces) have efficiencies ranging from 80-98%, but they directly burn fuel to produce heat, which can be more cost-effective depending on local energy prices.
-
Cost-Effectiveness of Electric Resistance Heating
- While electric resistance heating is 100% efficient at the point of use, it is often more expensive to operate than other heating methods due to the higher cost of electricity compared to natural gas or propane.
- The cost-effectiveness also depends on regional energy prices, insulation quality, and climate. In areas with low electricity costs or abundant renewable energy, electric resistance heating may be more viable.
-
Environmental Impact
- The environmental efficiency of electric resistance heating depends on the source of the electricity. If the electricity comes from renewable sources like wind, solar, or hydroelectric power, the environmental impact is minimal.
- However, if the electricity is generated from coal or natural gas, the carbon footprint of electric resistance heating can be significant due to the inefficiencies in power generation.
-
Practical Applications and Limitations
- Electric resistance heating is commonly used in space heaters, baseboard heaters, and electric furnaces. It is ideal for supplemental heating or in areas where other heating methods are impractical.
- Its limitations include high operating costs and inefficiency in poorly insulated spaces, where heat loss can offset the benefits of its 100% efficiency at the point of use.
In summary, while electric resistance heating is technically 100% efficient in converting electrical energy to heat, its overall efficiency and cost-effectiveness depend on broader factors like energy generation, transmission losses, and regional energy prices. It is best suited for specific applications where its simplicity and reliability outweigh its higher operational costs.
Summary Table:
Aspect | Details |
---|---|
Point-of-Use Efficiency | 100% efficient; all electrical energy is converted to heat. |
Energy Generation Losses | Power plants operate at 30-50% efficiency for fossil fuels. |
Transmission Losses | 5-10% energy lost during transmission and distribution. |
Comparison with Heat Pumps | Heat pumps are 200-300% efficient by transferring heat. |
Cost-Effectiveness | Higher operational costs compared to natural gas or propane heating. |
Environmental Impact | Minimal if powered by renewables; significant if powered by fossil fuels. |
Practical Applications | Ideal for supplemental heating or areas where other methods are impractical. |
Want to learn more about electric resistance heating? Contact our experts today for personalized advice!