Carbon coating is a process used to modify the surface properties of materials, often to enhance their chemical stability, structural integrity, and performance in applications like energy storage. The process can be broadly categorized into wet chemical methods and dry coating methods. Wet chemical methods involve traditional techniques such as hydrothermal/solvothermal, sol-gel, and chemical polymerization, which are widely used in market production. Dry coating methods, on the other hand, are more cost-effective and environmentally friendly, involving mechanical coating of larger particles with nanoparticles to form a core-shell structure. Techniques like chemical vapor deposition (CVD), atomic layer deposition (ALD), and physical vapor deposition (PVD) fall under this category. A specific dry coating method, thermal evaporation, involves heating a carbon source (like a thread or rod) to its evaporation temperature in a vacuum system, depositing a fine stream of carbon onto specimens. This method is commonly used for X-ray microanalysis and creating specimen support films on TEM grids.
Key Points Explained:
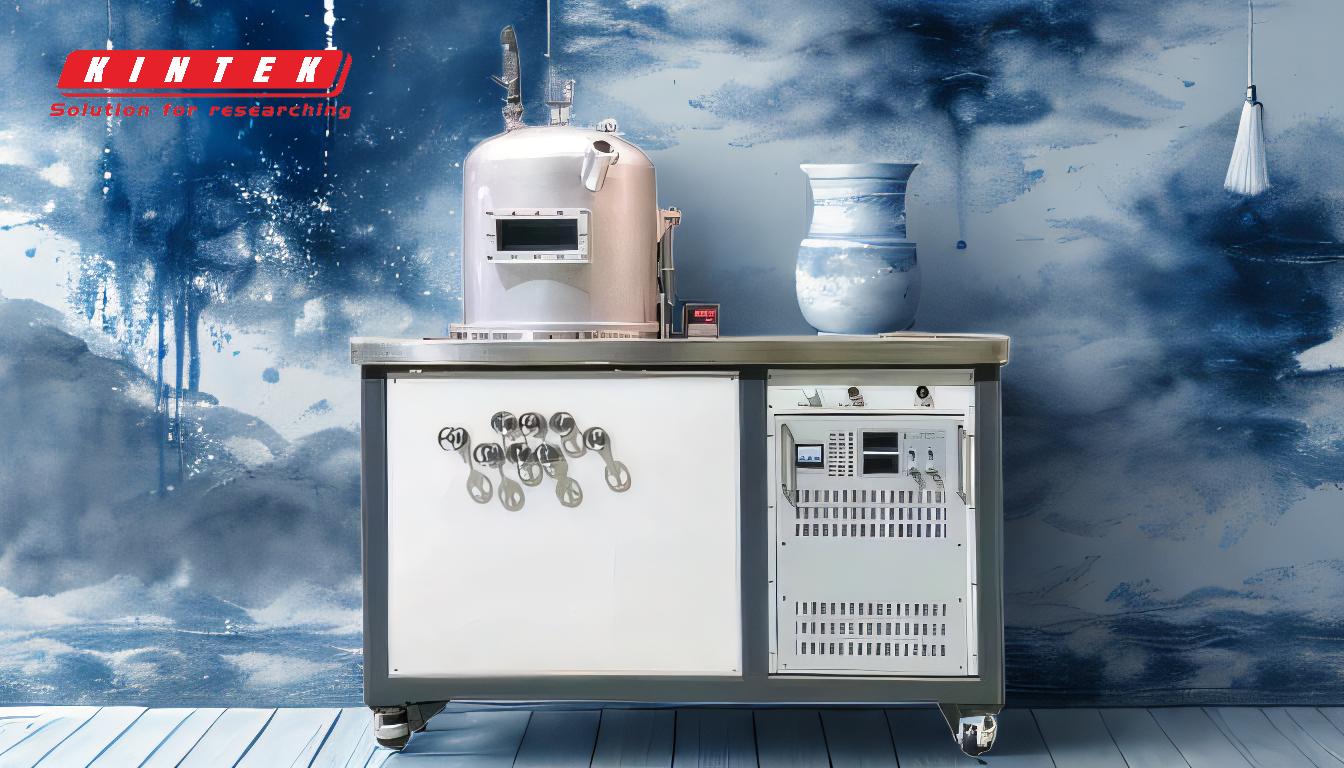
-
Mechanisms of Carbon Coating:
- Modifying Surface Chemical Stability: Carbon coating can alter the surface chemistry of a material, making it more resistant to chemical reactions that could degrade its performance.
- Enhancing Structural Stability: The coating can provide additional structural support, preventing the material from breaking down under stress.
- Improving Li-ion Diffusion: In battery applications, carbon coating can facilitate the movement of lithium ions, enhancing the efficiency and lifespan of the battery.
-
Dry Coating Methods:
- Thermal Evaporation: This technique involves heating a carbon source, such as a thread or rod, to its evaporation temperature in a vacuum system. The carbon then deposits onto the specimen in a fine stream. This method is particularly useful for X-ray microanalysis and creating specimen support films on TEM grids.
- Carbon Rod Coating: In this procedure, two carbon rods with a pointed contact area are used. A current flows between the rods, generating high heat at the contact point, causing carbon to evaporate. This can be done with either a ramping or pulsating current. The process involves outgassing to remove chemical binders, followed by carbon deposition under vacuum conditions.
- Chemical Vapor Deposition (CVD): This method involves the use of a chemical reaction to produce a thin film of carbon on the substrate. The process is carried out in a vacuum chamber where a precursor gas is introduced, and the reaction occurs on the heated substrate surface.
- Atomic Layer Deposition (ALD): ALD is a more precise version of CVD, where the deposition occurs layer by layer, allowing for extremely thin and uniform coatings.
- Physical Vapor Deposition (PVD): This method involves the physical transfer of material from a source to the substrate, typically through processes like sputtering or evaporation.
-
Wet Chemical Methods:
- Hydrothermal/Solvothermal: These methods involve the use of high-temperature and high-pressure conditions to deposit carbon coatings from a solution. The process is often used for creating coatings on electrode materials.
- Sol-Gel: This technique involves the transition of a solution (sol) into a gel-like state, which is then dried and heated to form a solid coating. The sol-gel process is versatile and can be used to create coatings with a variety of properties.
- Chemical Polymerization: This method involves the polymerization of monomers on the surface of the material to form a carbon coating. The process can be controlled to produce coatings with specific thicknesses and properties.
-
Applications of Carbon Coating:
- X-ray Microanalysis: Carbon coatings are used to prepare specimens for X-ray microanalysis, where the coating helps to prevent charging and improve the conductivity of the specimen.
- TEM Grids: Carbon coatings are also used to create support films on TEM grids, which are essential for the analysis of thin specimens in transmission electron microscopy.
- Battery Electrodes: In the field of energy storage, carbon coatings are applied to electrode materials to enhance their performance by improving conductivity and stability.
-
Environmental and Economic Considerations:
- Cost-Effectiveness: Dry coating methods are generally more cost-effective than wet chemical methods, as they often require less material and energy.
- Environmental Friendliness: Dry coating methods are also more environmentally friendly, as they typically produce less waste and use fewer hazardous chemicals compared to wet chemical methods.
In summary, carbon coating is a versatile process with a wide range of applications, from enhancing the performance of battery electrodes to preparing specimens for advanced microscopy. The choice of method depends on the specific requirements of the application, with both wet chemical and dry coating methods offering unique advantages.
Summary Table:
Aspect | Details |
---|---|
Mechanisms | Modifies surface stability, enhances structural integrity, improves Li-ion diffusion. |
Dry Coating Methods | Thermal evaporation, CVD, ALD, PVD. Cost-effective and eco-friendly. |
Wet Chemical Methods | Hydrothermal/solvothermal, sol-gel, chemical polymerization. Widely used. |
Applications | X-ray microanalysis, TEM grids, battery electrodes. |
Environmental Benefits | Dry methods reduce waste and hazardous chemicals. |
Discover how carbon coating can optimize your materials—contact our experts today!