Graphene production on a large scale involves a variety of techniques, each with its own advantages and limitations. The two primary approaches are the "top-down" and "bottom-up" methods. The top-down method involves deriving graphene from graphite, while the bottom-up method focuses on building graphene from carbon-containing precursors. Among these, chemical vapor deposition (CVD) stands out as the most promising technique for producing high-quality graphene on large areas. Other methods like mechanical exfoliation, liquid-phase exfoliation, and sublimation of silicon carbide (SiC) are also used but are less suitable for large-scale production due to cost, scalability, or quality issues.
Key Points Explained:
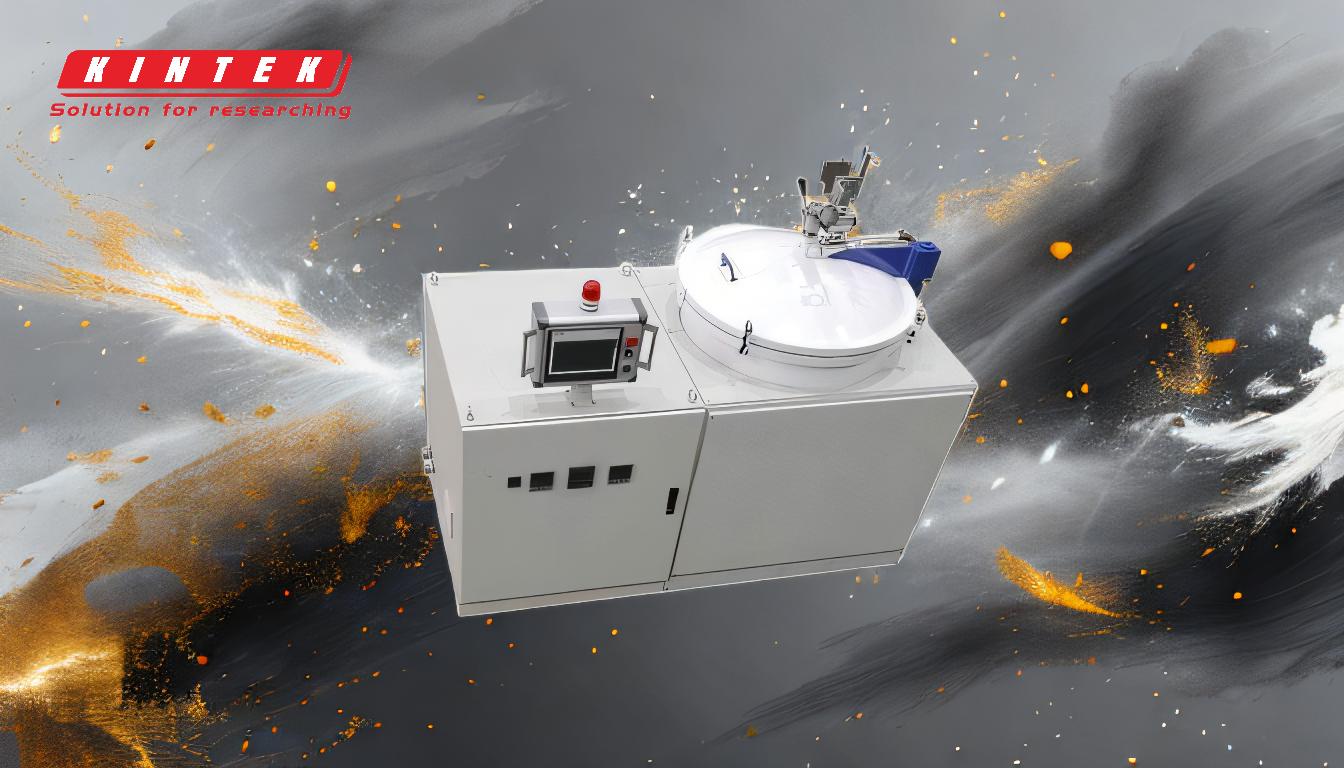
-
Top-Down Methods:
- Mechanical Exfoliation: This method involves peeling layers of graphene from graphite using adhesive tape. While it produces high-quality graphene, it is not scalable and is primarily used for fundamental research.
- Liquid-Phase Exfoliation: This technique involves dispersing graphite in a liquid medium and applying ultrasonic energy to exfoliate graphene layers. It is more scalable than mechanical exfoliation but often results in graphene with lower electrical quality.
- Chemical Oxidation: This method involves oxidizing graphite to produce graphene oxide, which is then reduced to graphene. While scalable, the process can introduce defects and impurities, affecting the graphene's quality.
-
Bottom-Up Methods:
- Chemical Vapor Deposition (CVD): CVD is the most promising method for large-scale graphene production. It involves decomposing carbon-containing gases on a metal substrate (usually copper or nickel) to form graphene layers. CVD produces high-quality graphene and can be scaled up for industrial applications.
- Epitaxial Growth: This method involves growing graphene on a silicon carbide (SiC) substrate at high temperatures. While it produces high-quality graphene, the process is expensive and not easily scalable.
- Arc Discharging: This technique involves creating an arc between two graphite electrodes in an inert gas atmosphere. While it can produce graphene, the process is less controlled and less suitable for large-scale production.
-
Challenges and Considerations:
- Scalability: While methods like CVD and liquid-phase exfoliation are more scalable, they still face challenges in terms of cost, uniformity, and quality control.
- Quality: The quality of graphene produced varies significantly between methods. CVD generally produces the highest quality graphene, but other methods may be sufficient for less demanding applications.
- Cost: The cost of production is a significant factor, especially for industrial applications. CVD, while promising, is still relatively expensive compared to other methods.
-
Future Directions:
- Improving CVD Techniques: Ongoing research aims to make CVD more cost-effective and scalable, potentially by optimizing the process or using alternative substrates.
- Hybrid Methods: Combining different methods, such as using liquid-phase exfoliation followed by CVD, could offer a balance between scalability and quality.
- New Materials: Research into new carbon-containing precursors or alternative substrates could further improve the efficiency and cost-effectiveness of graphene production.
In conclusion, while several methods exist for producing graphene on a large scale, chemical vapor deposition (CVD) is currently the most promising due to its ability to produce high-quality graphene in a scalable manner. However, challenges remain in terms of cost and quality control, and ongoing research is focused on overcoming these barriers to make large-scale graphene production more feasible for industrial applications.
Summary Table:
Method | Description | Scalability | Quality | Cost |
---|---|---|---|---|
Top-Down Methods | ||||
Mechanical Exfoliation | Peeling graphene layers from graphite using adhesive tape. | Low | High | High |
Liquid-Phase Exfoliation | Dispersing graphite in liquid and applying ultrasonic energy to exfoliate layers. | Medium | Medium | Medium |
Chemical Oxidation | Oxidizing graphite to produce graphene oxide, then reducing it to graphene. | High | Low to Medium | Low to Medium |
Bottom-Up Methods | ||||
Chemical Vapor Deposition (CVD) | Decomposing carbon gases on a metal substrate to form graphene. | High | High | High |
Epitaxial Growth | Growing graphene on a silicon carbide (SiC) substrate at high temperatures. | Low | High | Very High |
Arc Discharging | Creating an arc between graphite electrodes in an inert gas atmosphere. | Low | Medium | Medium |
Interested in large-scale graphene production? Contact our experts today to learn more about the best methods for your needs!