Controlling the heat of an induction heater involves precise manipulation of electrical parameters to achieve desired heating outcomes. The primary methods include adjusting the strength of the applied current, which influences the eddy currents and hysteresis effects in the material. Advanced control systems, such as single-phase sinusoidal pulse width modulation (SPWM) digital signal processor (DSP)-based inverters, are used to regulate the frequency and waveform of the current. This ensures localized and consistent heating, with minimal temperature differences between the core and surface of the material. Additionally, the ability to control molten metal states or solidification processes further highlights the versatility of induction heating systems.
Key Points Explained:
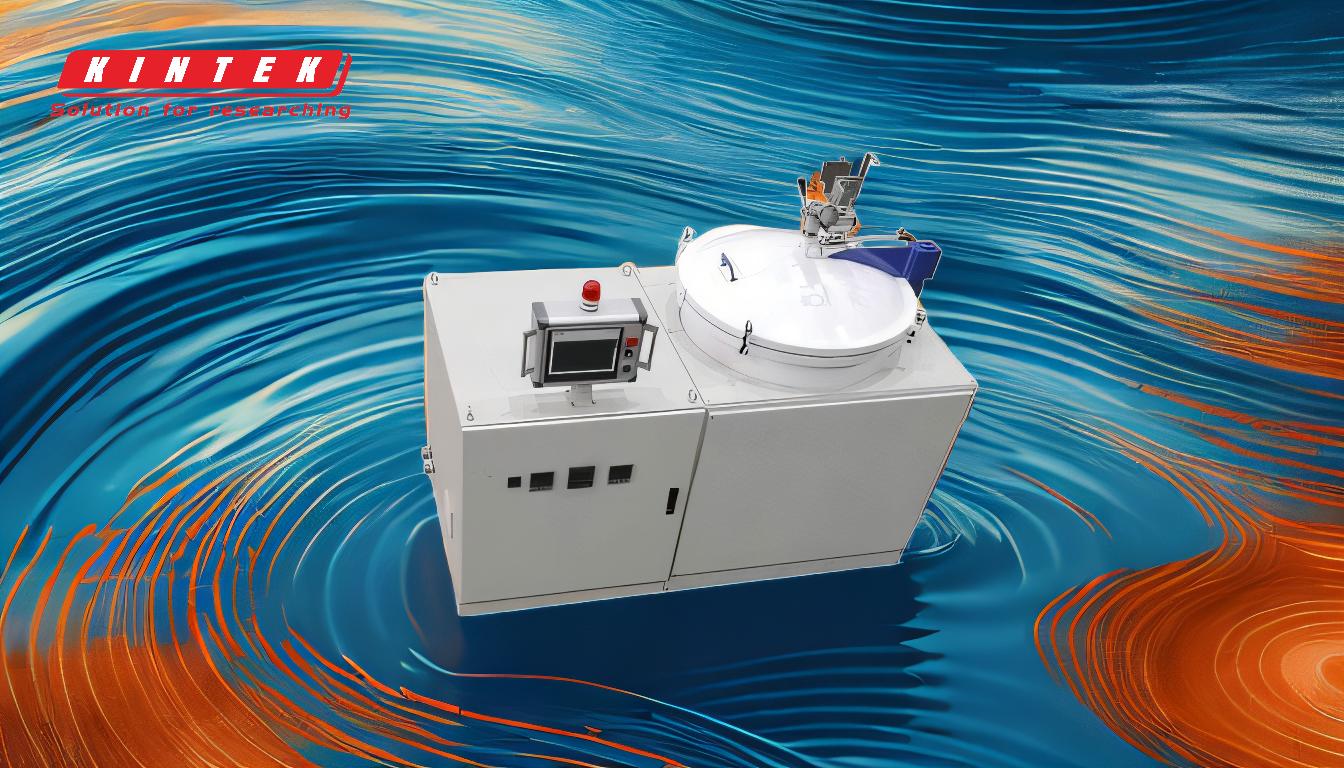
-
Control via Current Strength:
- The heating temperature in induction heating is directly influenced by the strength of the applied current.
- By increasing or decreasing the current, the intensity of the eddy currents generated within the material can be controlled.
- Eddy currents flow opposite to the material's electrical resistivity, creating localized heating.
- This allows for precise temperature adjustments, making it ideal for applications requiring fine-tuned heat control.
-
Hysteresis Effect:
- In magnetic materials, heat is also generated due to hysteresis, which is the internal friction caused by resistance to the changing magnetic field.
- This effect is particularly significant in ferromagnetic materials, where the magnetic domains realign with the alternating magnetic field, producing additional heat.
- Controlling the current strength indirectly influences the hysteresis effect, providing another layer of temperature regulation.
-
Advanced Control Systems (SPWM and DSP):
- Single-phase sinusoidal pulse width modulation (SPWM) digital signal processor (DSP)-based inverters are used to control the induction heating coil.
- The DSP stores commands to generate specific waveforms, enabling precise control over the frequency and amplitude of the current.
- This technology ensures consistent and accurate heating, reducing temperature variations and improving energy efficiency.
-
Temperature Uniformity and Accuracy:
- Induction furnaces are designed to minimize temperature differences between the core and surface of the material.
- This uniformity is achieved through precise control of the heating process, ensuring consistent results across the entire workpiece.
- High temperature control accuracy is a hallmark of induction heating, making it suitable for applications requiring strict thermal management.
-
Molten Metal Control:
- Induction heating systems can also control the state of molten metal by adjusting current parameters.
- This capability allows for maintaining the metal in a liquid state or controlling its solidification process with high precision.
- Such control is critical in metallurgical processes, where specific cooling rates and temperature profiles are required to achieve desired material properties.
By leveraging these methods and technologies, induction heating systems offer unparalleled control over heat generation and distribution, making them indispensable in industries requiring precise thermal management.
Summary Table:
Method | Key Features | Applications |
---|---|---|
Control via Current Strength | Adjusts eddy currents for localized heating; ideal for fine-tuned temperature control. | Precision heating in manufacturing, labs, and material processing. |
Hysteresis Effect | Generates heat in magnetic materials; influenced by current strength. | Ferromagnetic material heating, such as in steel and alloy processing. |
Advanced Control Systems | SPWM and DSP-based inverters regulate frequency and waveform for consistent heating. | High-efficiency heating in industrial and metallurgical applications. |
Temperature Uniformity | Minimizes core-to-surface temperature differences; ensures consistent results. | Applications requiring strict thermal management, like aerospace and electronics. |
Molten Metal Control | Adjusts current to control molten metal states and solidification processes. | Metallurgical processes requiring precise cooling rates and material properties. |
Achieve precise thermal control with advanced induction heating systems—contact our experts today to learn more!