Metal casting, a widely used manufacturing process, has both environmental benefits and drawbacks. While it enables the production of complex metal components with high precision, it also poses environmental challenges due to emissions, energy consumption, and waste generation. The environmental impact largely depends on the materials used, energy sources, and pollution control measures implemented. Below is a detailed analysis of the environmental aspects of metal casting.
Key Points Explained:
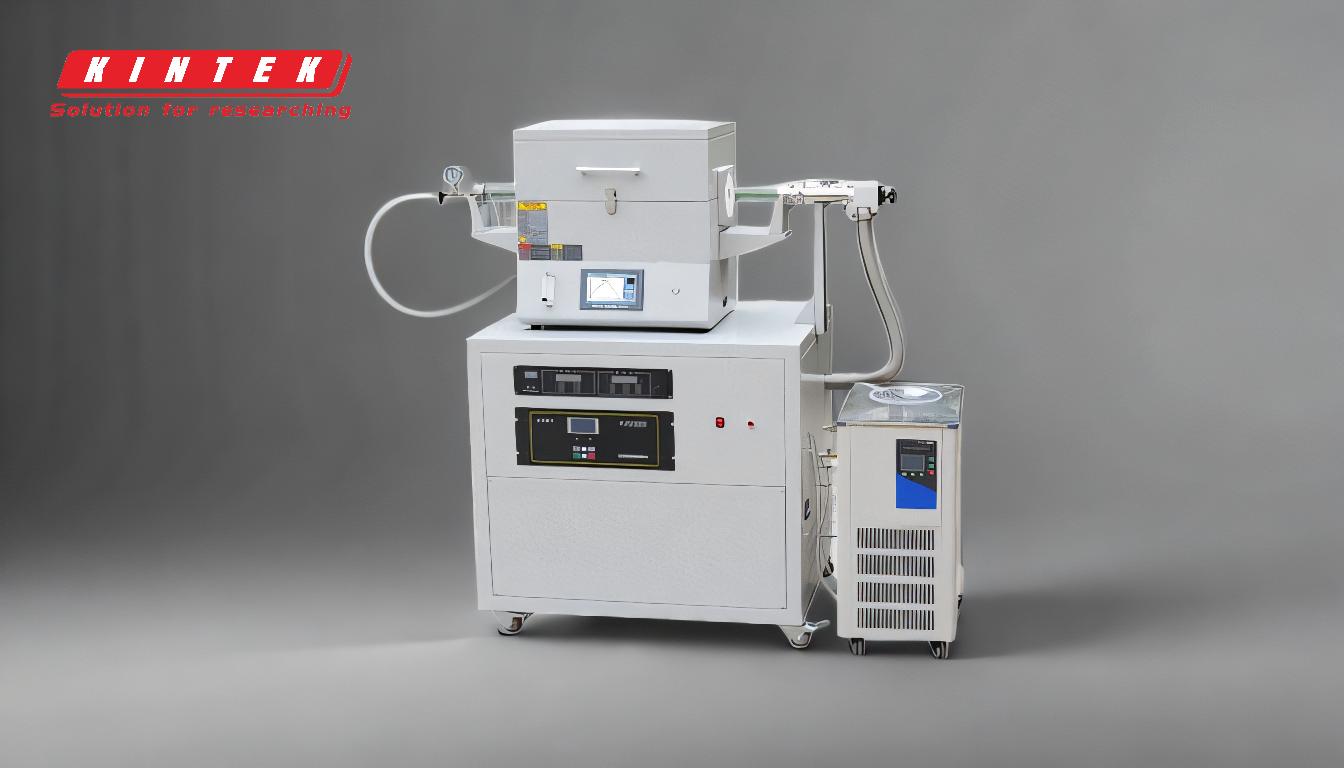
-
Energy Consumption and Emissions
- Metal casting processes, especially those involving crucible furnaces, often rely on fossil fuels like coal, natural gas, or oil as heat sources.
- The combustion of these fuels releases greenhouse gases (GHGs) such as carbon dioxide (CO₂), nitrogen oxides (NOₓ), and sulfur oxides (SOₓ), contributing to climate change and air pollution.
- Electric furnaces, while cleaner, still depend on the energy mix of the grid, which may include fossil fuels unless renewable energy sources are utilized.
- The energy-intensive nature of melting metals makes metal casting a significant contributor to industrial carbon footprints.
-
Pollution Control Measures
- Modern foundries often implement pollution control technologies to mitigate emissions.
- Examples include scrubbers, filters, and electrostatic precipitators to capture particulate matter and harmful gases.
- Recycling systems for waste gases and heat recovery systems can improve energy efficiency and reduce environmental impact.
- However, these measures require additional investment and operational costs, which may not be feasible for all foundries, especially smaller ones.
-
Material Waste and Recycling
- Metal casting generates waste materials such as slag, dross, and unused sand from molds.
- Slag and dross, byproducts of the melting process, can be recycled to recover valuable metals, reducing the need for virgin materials.
- Foundry sand, used in mold-making, can often be reclaimed and reused, minimizing waste.
- The recycling of scrap metal in casting processes significantly reduces the environmental impact compared to mining and refining raw ores.
-
Use of Sustainable Materials
- The choice of metals and alloys can influence the environmental footprint of casting.
- Lightweight metals like aluminum and magnesium require less energy to melt compared to heavier metals like steel or iron.
- The use of recycled metals reduces energy consumption and emissions associated with primary metal production.
- However, some alloys may contain toxic elements (e.g., lead or cadmium), which can pose environmental and health risks if not properly managed.
-
Water Usage and Contamination
- Metal casting processes often require water for cooling and cleaning purposes.
- Contaminated water from casting operations can contain heavy metals, oils, and chemicals, which must be treated before discharge to prevent environmental harm.
- Water recycling systems can help reduce water consumption and minimize contamination risks.
-
Comparison with Alternative Manufacturing Methods
- Compared to other manufacturing processes like machining or additive manufacturing, metal casting can be more energy-intensive due to the high temperatures required for melting metals.
- However, casting often produces less material waste than machining, as it shapes components directly from molten metal rather than removing material from a solid block.
- Additive manufacturing (3D printing) is generally more energy-efficient and produces less waste, but it may not be suitable for large-scale production or certain types of metal components.
-
Regulatory and Industry Standards
- Environmental regulations play a crucial role in minimizing the impact of metal casting.
- Foundries must comply with emissions limits, waste disposal guidelines, and energy efficiency standards set by local and international authorities.
- Industry initiatives, such as the adoption of green manufacturing practices and certifications, encourage foundries to reduce their environmental footprint.
-
Potential for Improvement
- Advances in technology, such as induction furnaces and renewable energy integration, can make metal casting more environmentally friendly.
- The development of biodegradable or reusable mold materials can further reduce waste.
- Collaboration between industry stakeholders, researchers, and policymakers is essential to drive innovation and promote sustainable practices in metal casting.
In conclusion, metal casting is not inherently environmentally friendly due to its energy intensity, emissions, and waste generation. However, with the adoption of sustainable practices, advanced technologies, and stringent pollution control measures, its environmental impact can be significantly reduced. The industry's future lies in balancing economic efficiency with environmental responsibility, ensuring that metal casting remains a viable and sustainable manufacturing method.
Summary Table:
Aspect | Impact | Mitigation Strategies |
---|---|---|
Energy Consumption | High energy use, reliance on fossil fuels, GHG emissions | Use of electric furnaces, renewable energy sources, and heat recovery systems |
Pollution Control | Emissions of particulate matter and harmful gases | Scrubbers, filters, electrostatic precipitators, and recycling systems |
Material Waste | Generation of slag, dross, and mold waste | Recycling of metals, reclamation of foundry sand, and reuse of scrap materials |
Sustainable Materials | Use of lightweight metals and recycled alloys | Avoidance of toxic elements, adoption of eco-friendly alloys |
Water Usage | Water contamination with heavy metals and chemicals | Water recycling systems and treatment of contaminated water |
Regulatory Compliance | Need to meet emissions and waste disposal standards | Adoption of green manufacturing practices and certifications |
Future Improvements | Potential for induction furnaces, renewable energy, and reusable molds | Collaboration for innovation and sustainable practices |
Discover how to minimize the environmental impact of metal casting—contact our experts today for sustainable solutions!