Heat treatment of steel involves controlled heating and cooling processes to alter its physical and mechanical properties, making it suitable for specific applications. The four primary heat treatment methods for steel are hardening, tempering, annealing, and normalizing. Each method serves a distinct purpose: hardening increases strength and wear resistance, tempering reduces brittleness, annealing improves ductility and reduces internal stresses, and normalizing refines grain structure for uniformity. These processes are essential in industries like manufacturing, construction, and automotive, where steel's performance under stress, wear, and temperature is critical. Understanding these treatments helps in selecting the right method for achieving desired material properties.
Key Points Explained:
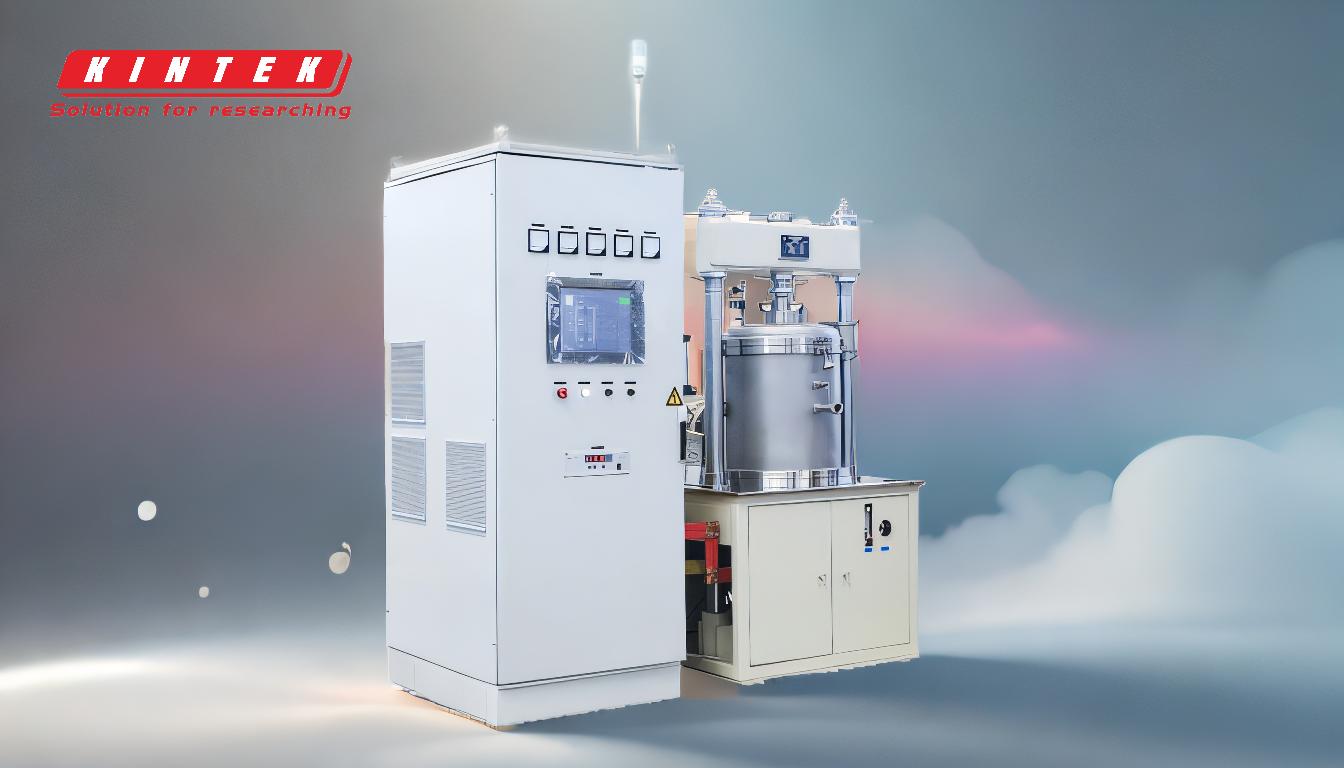
-
Hardening
- Purpose: Increases the hardness and strength of steel by transforming its microstructure into martensite, a hard and brittle phase.
- Process: Steel is heated to a temperature above its critical point (austenitizing temperature) and then rapidly cooled, typically through quenching in water, oil, or air.
- Applications: Used for tools, gears, and components requiring high wear resistance and strength.
- Considerations: Hardening can make steel brittle, so it is often followed by tempering to reduce brittleness.
-
Tempering
- Purpose: Reduces the brittleness of hardened steel while maintaining its hardness and strength.
- Process: Hardened steel is reheated to a temperature below its critical point and then cooled slowly. The temperature and duration of tempering determine the final properties.
- Applications: Commonly used for cutting tools, springs, and structural components that require a balance of hardness and toughness.
- Considerations: Higher tempering temperatures increase toughness but reduce hardness, so the process must be carefully controlled.
-
Annealing
- Purpose: Improves ductility, reduces hardness, and eliminates internal stresses in steel, making it easier to machine or form.
- Process: Steel is heated to a temperature above its critical point, held at that temperature for a period, and then slowly cooled, often in a furnace.
- Applications: Used for components that require extensive machining or cold working, such as forgings and castings.
- Considerations: Annealing can result in a softer material, which may not be suitable for high-strength applications without further treatment.
-
Normalizing
- Purpose: Refines the grain structure of steel, improving its mechanical properties and uniformity.
- Process: Steel is heated to a temperature above its critical point and then cooled in air, which is faster than annealing but slower than quenching.
- Applications: Used for parts that require a uniform structure and improved mechanical properties, such as structural components and large forgings.
- Considerations: Normalizing produces a harder and stronger material than annealing but with less ductility.
Each of these heat treatment methods plays a critical role in tailoring steel's properties to meet specific industrial requirements. By understanding the purpose, process, and applications of hardening, tempering, annealing, and normalizing, manufacturers and engineers can select the appropriate treatment to achieve the desired balance of strength, toughness, and workability in steel components.
Summary Table:
Method | Purpose | Process | Applications | Considerations |
---|---|---|---|---|
Hardening | Increases hardness and strength, transforms microstructure into martensite. | Heated above critical point, rapidly cooled (quenched in water, oil, or air). | Tools, gears, high-wear components. | Can make steel brittle; often followed by tempering. |
Tempering | Reduces brittleness while maintaining hardness and strength. | Reheated below critical point, cooled slowly. | Cutting tools, springs, structural components. | Higher tempering temps increase toughness but reduce hardness. |
Annealing | Improves ductility, reduces hardness, eliminates internal stresses. | Heated above critical point, held, then slowly cooled (often in a furnace). | Components requiring machining or cold working (e.g., forgings, castings). | Results in softer material; may not suit high-strength applications. |
Normalizing | Refines grain structure, improves mechanical properties and uniformity. | Heated above critical point, cooled in air (faster than annealing, slower than quenching). | Structural components, large forgings. | Produces harder, stronger material than annealing but with less ductility. |
Need help selecting the right heat treatment method for your steel components? Contact our experts today!