Press forging and hammer forging are two distinct methods used in metalworking, each with its own set of advantages and disadvantages. Press forging, in particular, offers several benefits over hammer forging, making it a preferred choice in many industrial applications. Below is a detailed exploration of the advantages of press forging over hammer forging.
Key Points Explained:
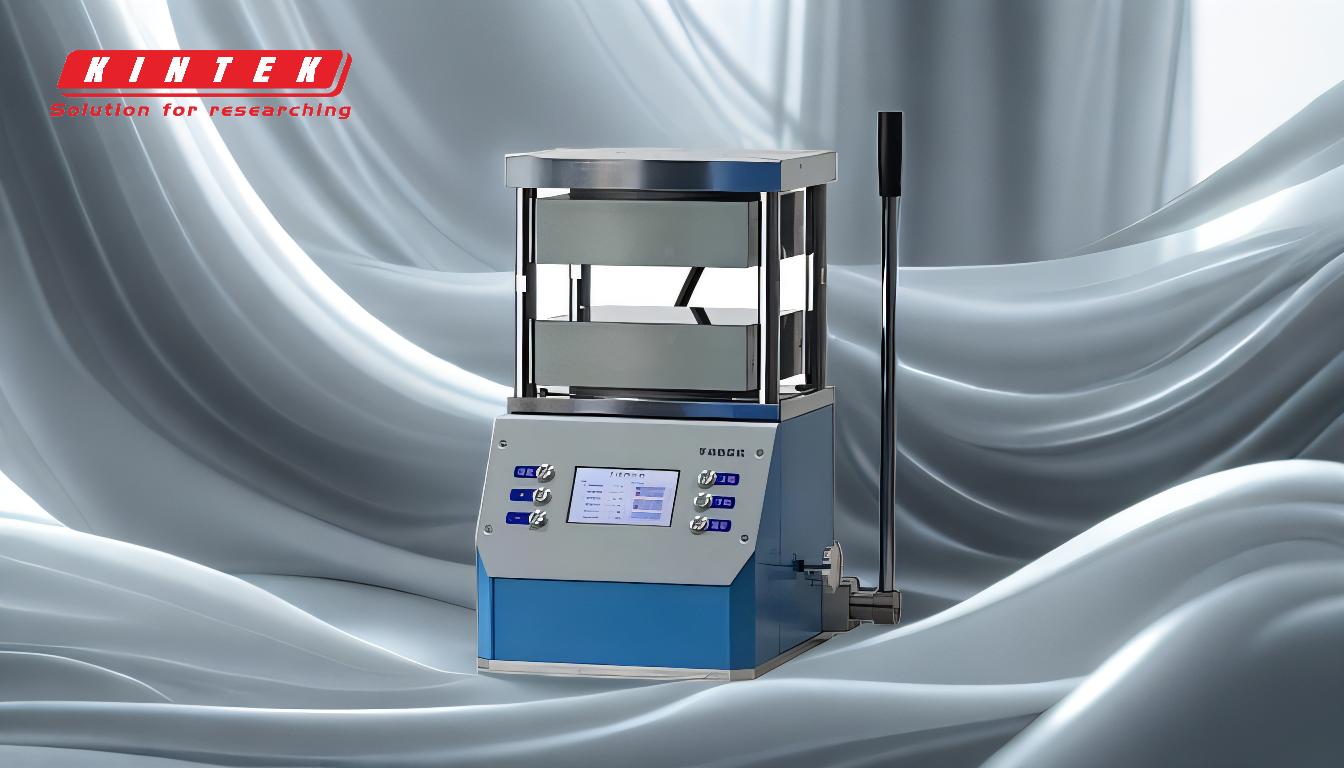
-
Speed and Cost Efficiency:
- Press Forging: The press forging process is generally quicker and less expensive compared to hammer forging. This is because press forging involves a continuous application of pressure, which can be more efficiently controlled and automated, leading to faster production times and lower labor costs.
- Hammer Forging: In contrast, hammer forging involves repeated blows to shape the metal, which can be more time-consuming and labor-intensive.
-
Grain Flow and Strength:
- Press Forging: One of the significant advantages of press forging is the enhancement of grain flow within the metal. The continuous pressure applied during press forging compresses the grain structure, leading to a more uniform and aligned grain flow. This results in a final piece that is stronger and more durable.
- Hammer Forging: While hammer forging also affects grain flow, the repeated impacts can sometimes lead to less uniform grain structures, potentially compromising the strength of the final product.
-
Stress Reduction:
- Press Forging: The process of press forging reduces stress on corners and fillets of the forged piece. This is due to the even distribution of pressure, which minimizes the risk of stress concentration points that could lead to failure under load.
- Hammer Forging: The repeated impacts in hammer forging can create localized stress points, especially in complex geometries, which might require additional post-forging treatments to mitigate.
-
Metallurgical Defects:
- Press Forging: Press forging minimizes metallurgical defects such as porosity and alloy segregation. The controlled application of pressure ensures a more homogeneous material structure, which improves the piece's response to heat treatment and reduces the likelihood of defects.
- Hammer Forging: The impact nature of hammer forging can sometimes lead to internal defects like porosity, especially if the forging process is not meticulously controlled.
-
Machining Time:
- Press Forging: Due to the superior grain structure and reduced metallurgical defects, press-forged parts often require less machining time. The more precise and uniform shape achieved through press forging means that less material needs to be removed during machining, saving time and costs.
- Hammer Forging: Parts produced by hammer forging may require more extensive machining to achieve the desired final dimensions and surface finish, increasing both time and cost.
-
Precision and Consistency:
- Press Forging: Press forging allows for greater precision and consistency in the final product. The controlled application of pressure ensures that each piece is forged to exact specifications, which is particularly important for high-precision components.
- Hammer Forging: While hammer forging can also produce precise parts, the variability introduced by the repeated impacts can lead to slight inconsistencies between pieces.
-
Automation and Scalability:
- Press Forging: The process is more amenable to automation, making it easier to scale up production. Automated press forging lines can produce large quantities of parts with minimal human intervention, leading to higher efficiency and lower costs.
- Hammer Forging: Automation is more challenging with hammer forging due to the nature of the process, which relies on repeated impacts. This can limit the scalability of hammer forging operations.
In summary, press forging offers several advantages over hammer forging, including speed and cost efficiency, enhanced grain flow and strength, reduced stress on the final piece, minimized metallurgical defects, reduced machining time, greater precision and consistency, and better scalability through automation. These benefits make press forging a preferred method in many industrial applications where high-quality, durable, and precisely manufactured parts are required.
Summary Table:
Aspect | Press Forging | Hammer Forging |
---|---|---|
Speed and Cost | Faster and less expensive due to continuous pressure and automation. | Time-consuming and labor-intensive due to repeated blows. |
Grain Flow & Strength | Enhanced grain flow for stronger, more durable parts. | Less uniform grain structure, potentially compromising strength. |
Stress Reduction | Even pressure reduces stress on corners and fillets. | Repeated impacts create localized stress points, requiring post-forging treatments. |
Metallurgical Defects | Minimizes defects like porosity and alloy segregation. | Higher risk of internal defects like porosity. |
Machining Time | Reduced machining time due to precise and uniform shapes. | More extensive machining required for final dimensions and finish. |
**Precision & Consistency | Greater precision and consistency in final products. | Slight inconsistencies due to repeated impacts. |
**Automation & Scalability | Easier to automate and scale for large production. | Limited scalability due to reliance on repeated impacts. |
Ready to optimize your metalworking process with press forging? Contact us today to learn more!