RF magnetron sputtering is a highly versatile and efficient thin film deposition technique that offers numerous advantages over traditional methods. It is particularly beneficial for depositing a wide range of materials, including insulators, and is known for its high deposition rates, film purity, and uniformity. The process is also suitable for heat-sensitive substrates, making it ideal for applications in microelectronics, semiconductors, and optical coatings. By utilizing magnetic fields to concentrate plasma near the target surface, RF magnetron sputtering enhances ion bombardment and sputtering rates without increasing operating pressure, resulting in a more efficient and controlled deposition process.
Key Points Explained:
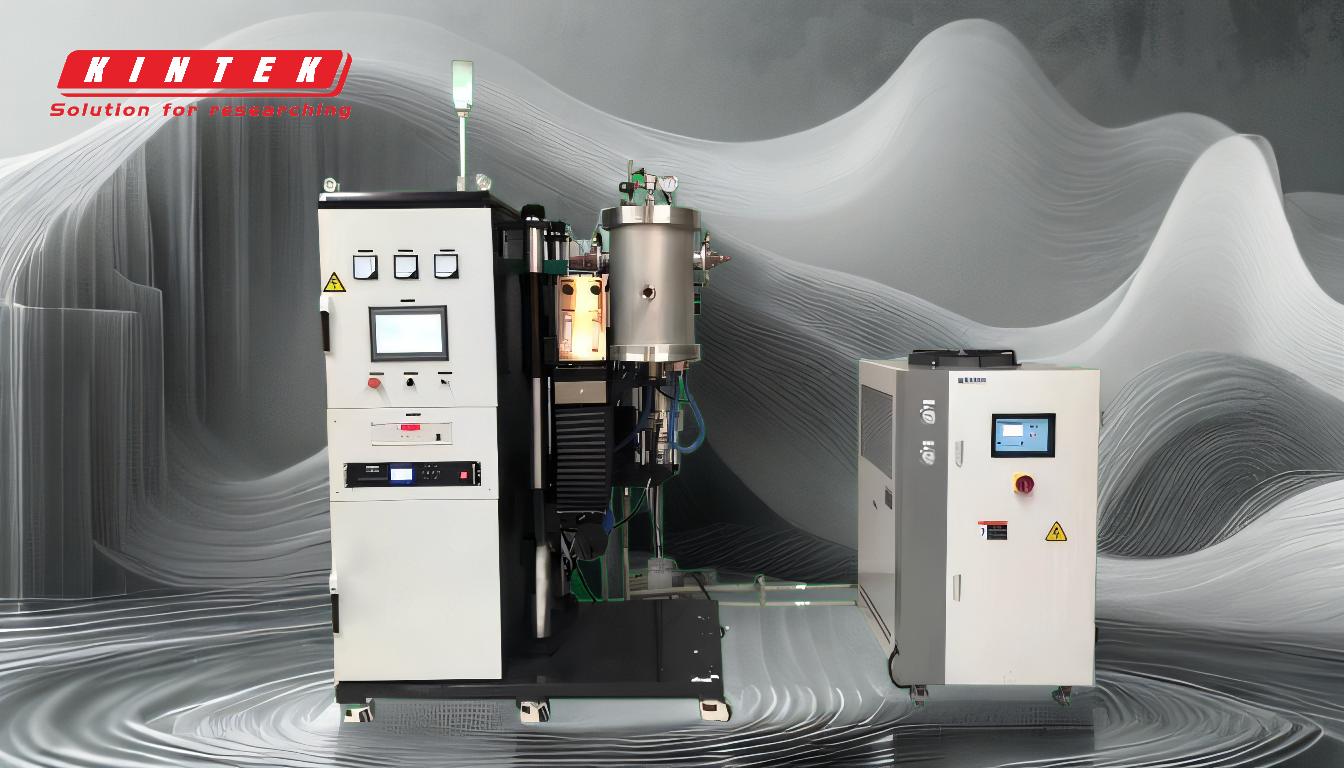
-
Versatility in Material Deposition:
- RF magnetron sputtering can deposit a wide variety of materials, including metals, alloys, oxides, and insulating materials. This is because the technique does not require the sputtering target to be conductive, unlike DC sputtering. This makes it suitable for applications where non-conductive materials like ceramics or polymers need to be deposited.
-
High Deposition Rates:
- The use of magnetic fields in RF magnetron sputtering traps electrons near the target surface, intensifying the plasma and increasing ion bombardment. This leads to faster sputtering rates compared to conventional sputtering methods, making the process more efficient and time-saving.
-
Film Purity and Compactness:
- The films produced by RF magnetron sputtering are known for their high purity and density. The process minimizes contamination, resulting in films with excellent mechanical and optical properties. This is particularly important in applications like semiconductor manufacturing and optical coatings, where film quality is critical.
-
Uniformity and Large-Area Coverage:
- RF magnetron sputtering provides uniform film deposition over large-area substrates. This is achieved through precise control of the sputtering parameters, such as power, pressure, and target-substrate distance. The uniformity ensures consistent film properties across the entire substrate, which is essential for industrial-scale production.
-
Low-Temperature Deposition:
- One of the standout advantages of RF magnetron sputtering is its ability to deposit films at low temperatures. This makes it suitable for heat-sensitive substrates, such as polymers or certain semiconductors, which could be damaged by high-temperature processes.
-
Control Over Film Properties:
- The process allows for precise control over film properties, such as thickness, particle size, and composition. By adjusting parameters like power, gas pressure, and target material, manufacturers can tailor the film to meet specific requirements, such as enhanced adhesion, optical transparency, or electrical conductivity.
-
Minimal Substrate Damage:
- The RF magnetron sputtering process minimizes damage to the substrate due to the lower operating pressure and controlled ion bombardment. This is particularly beneficial for delicate substrates or when depositing thin films that require a smooth and defect-free surface.
-
Industrial Scalability:
- RF magnetron sputtering is easily scalable for industrial applications. The process is repeatable, and the equipment can be adapted for large-scale production, making it a cost-effective solution for manufacturing high-quality thin films in bulk.
-
Combination of Materials:
- The technique allows for the simultaneous sputtering of different materials, enabling the creation of composite films or multilayered structures. This is useful in applications requiring specific material properties, such as wear-resistant coatings or multifunctional optical films.
-
Advancements and Research:
- RF magnetron sputtering continues to evolve with ongoing research and technological advancements. Improvements in power supplies, target materials, and process control are further enhancing its capabilities, making it a cutting-edge solution for modern thin film deposition challenges.
In summary, RF magnetron sputtering is a highly advantageous technique for thin film deposition, offering versatility, efficiency, and precision. Its ability to handle a wide range of materials, produce high-quality films, and operate at low temperatures makes it a preferred choice for various industrial and research applications.
Summary Table:
Advantage | Description |
---|---|
Versatility | Deposits metals, alloys, oxides, and insulators, including non-conductive materials. |
High Deposition Rates | Faster sputtering rates due to intensified plasma and ion bombardment. |
Film Purity & Compactness | Produces high-purity, dense films with excellent mechanical and optical properties. |
Uniformity | Ensures uniform film deposition over large-area substrates. |
Low-Temperature Deposition | Suitable for heat-sensitive substrates like polymers and semiconductors. |
Control Over Film Properties | Precise control of thickness, composition, and particle size for tailored applications. |
Minimal Substrate Damage | Reduces substrate damage with controlled ion bombardment and low operating pressure. |
Industrial Scalability | Easily scalable for large-scale production, making it cost-effective for industrial applications. |
Combination of Materials | Enables creation of composite or multilayered films for specific material properties. |
Advancements & Research | Continuously evolving with improvements in power supplies, target materials, and process control. |
Unlock the full potential of RF magnetron sputtering for your applications—contact our experts today!