Brazing, while a widely used joining technique, has several disadvantages that can affect the quality, efficiency, and cost of the process. These disadvantages vary depending on the type of brazing method used, such as vacuum brazing or hand brazing. Key issues include reduced material hardness, high technical and process requirements, energy consumption, long processing times, and challenges related to oxidation and flux residues. Understanding these drawbacks is crucial for anyone considering brazing as a joining method, as they can impact the final product's performance and the overall production process.
Key Points Explained:
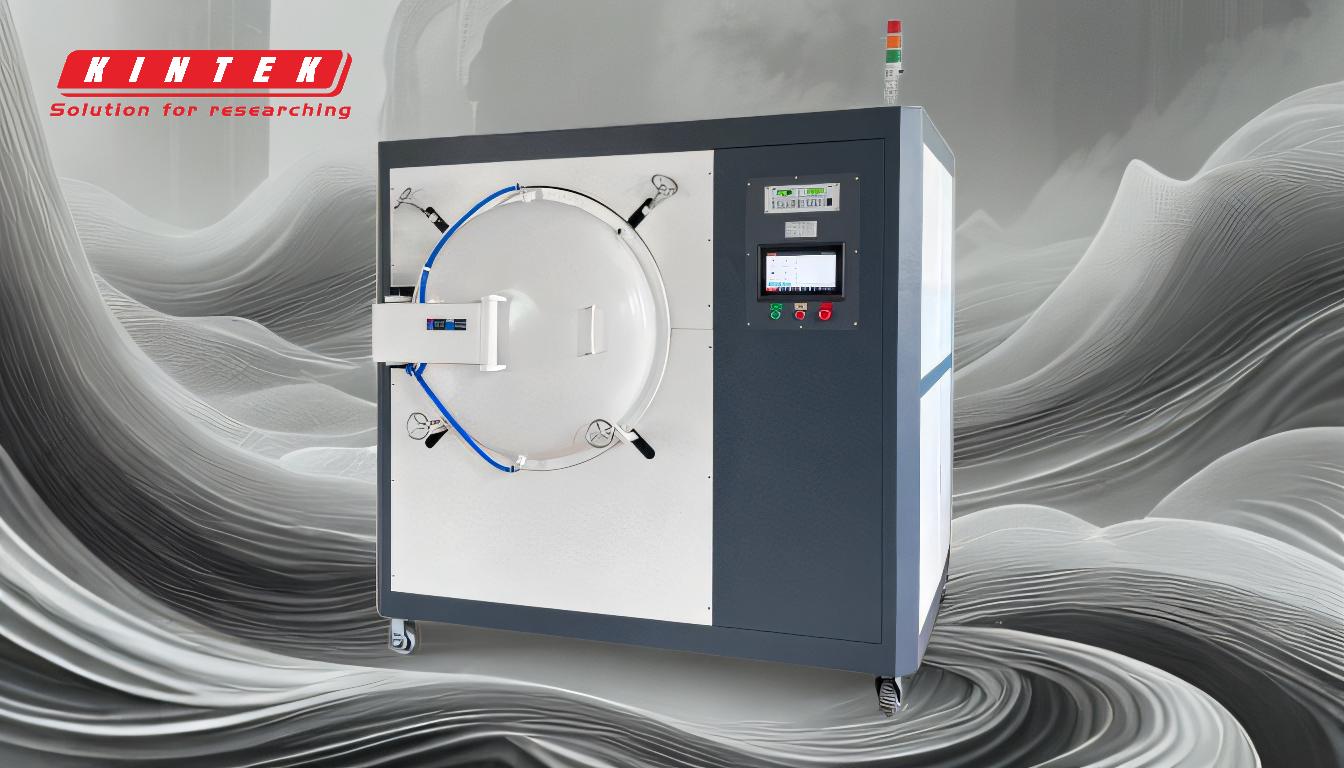
-
Reduced Material Hardness After High-Temperature Welding:
- In vacuum brazing, the high temperatures required to melt the filler material can lead to a reduction in the hardness of the base metal. This is particularly problematic for materials that rely on their hardness for structural integrity or wear resistance. The softening of the material can compromise the strength and durability of the joint, making it less suitable for high-stress applications.
-
High Process Requirements and Technical Difficulty:
- Brazing, especially vacuum brazing, demands precise control over temperature, atmosphere, and filler material placement. This requires specialized equipment and skilled operators, increasing the complexity and cost of the process. The need for a controlled environment, such as a vacuum or inert gas atmosphere, adds to the technical challenges and limits the accessibility of the process for smaller operations.
-
High Energy Consumption:
- The brazing process, particularly vacuum brazing, consumes a significant amount of energy due to the need for high temperatures and controlled environments. This not only increases operational costs but also has environmental implications, making it less sustainable compared to other joining methods.
-
Long Processing Time:
- Brazing often requires extended heating and cooling cycles to ensure proper joint formation and to prevent thermal stress. This can lead to longer production times, reducing throughput and efficiency. In industries where time is a critical factor, this can be a significant disadvantage.
-
High Cleaning and Environmental Protection Costs:
- Before brazing, materials often need to be thoroughly cleaned to remove oxides, oils, and other contaminants that could impair joint quality. Additionally, the use of fluxes in some brazing processes can leave residues that require post-brazing cleaning. These steps add to the overall cost and complexity of the process, and the disposal of cleaning agents and flux residues can have environmental implications.
-
Overheating and Weakening of Base Metal in Hand Brazing:
- When brazing is performed manually with a torch in an open environment, there is a risk of overheating the base metal. This can lead to localized weakening and oxidation, resulting in a joint that is both mechanically weaker and less visually appealing. The uneven heating can also cause distortion or warping of the components.
-
Oxidation and Flux Residues:
- In open-air brazing, oxidation of the base metal is a common issue, which can weaken the joint and reduce its aesthetic quality. To prevent oxidation, fluxes are often used, but these can leave behind residues that are difficult to remove and can cause voids in the joint. These voids can act as stress concentrators, further reducing the joint's strength.
In summary, while brazing offers several advantages, such as the ability to join dissimilar materials and create strong, leak-tight joints, it also comes with significant disadvantages. These include material softening, high technical and energy requirements, long processing times, and issues related to oxidation and flux residues. Understanding these drawbacks is essential for making informed decisions about whether brazing is the right joining method for a particular application.
Summary Table:
Disadvantage | Description |
---|---|
Reduced Material Hardness | High temperatures in vacuum brazing soften base metal, reducing strength. |
High Process Requirements | Requires precise temperature control, specialized equipment, and skilled labor. |
High Energy Consumption | Significant energy use increases costs and environmental impact. |
Long Processing Time | Extended heating and cooling cycles reduce production efficiency. |
High Cleaning and Environmental Costs | Pre- and post-brazing cleaning adds complexity and cost. |
Overheating in Hand Brazing | Manual torch brazing risks weakening and warping the base metal. |
Oxidation and Flux Residues | Open-air brazing causes oxidation; flux residues weaken joints. |
Need help deciding if brazing is right for your application? Contact our experts today for tailored advice!