The materials used for acid lining and basic lining in electric induction furnaces are chosen based on the type of metal being melted and the specific requirements of the furnace operation. Acid linings are typically used for melting non-ferrous metals, while basic linings are employed for ferrous metals. The choice of lining material is critical for ensuring the efficiency, safety, and longevity of the furnace. Acid linings are often made from silica-based materials, whereas basic linings may include magnesia or dolomite. Additionally, other materials like chrome-magnesia, alumina-chrome, and silicon carbide can be used depending on the specific application. The lining must withstand high temperatures, thermal shocks, and chemical interactions with the molten metal.
Key Points Explained:
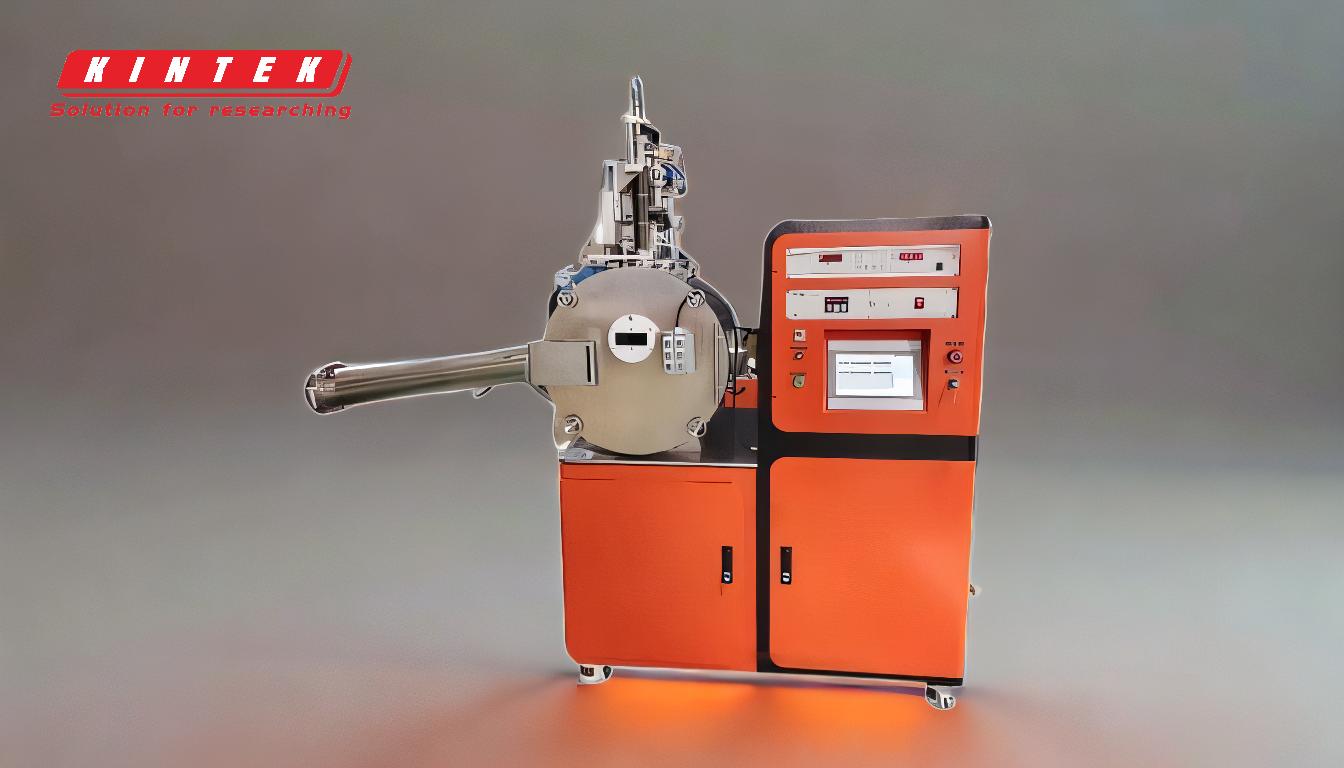
-
Acid Lining Materials:
- Primary Material: Silica (SiO₂) is the most common material used for acid linings. It is suitable for melting non-ferrous metals such as copper, brass, and bronze.
- Properties: Silica-based linings are highly resistant to acidic slags and provide good thermal insulation. They are also cost-effective and widely available.
- Applications: Acid linings are ideal for melting metals that do not require high levels of deoxidation or desulfurization, which are processes typically associated with ferrous metals.
-
Basic Lining Materials:
- Primary Materials: Basic linings are typically made from magnesia (MgO) or dolomite (a mixture of calcium carbonate and magnesium carbonate). These materials are used for melting ferrous metals like steel and iron.
- Properties: Magnesia and dolomite linings are highly resistant to basic slags and can withstand the high temperatures and chemical reactions involved in melting ferrous metals. They also provide excellent thermal stability and durability.
- Applications: Basic linings are essential for processes that involve the removal of impurities like phosphorus and sulfur from ferrous metals. They are also used in applications where the slag is basic in nature.
-
Other Lining Materials:
- Chrome-Magnesia: This material is a combination of chromium oxide (Cr₂O₃) and magnesia (MgO). It offers excellent resistance to both acidic and basic slags, making it versatile for various melting applications.
- Alumina-Chrome: This material combines alumina (Al₂O₃) with chromium oxide. It is known for its high thermal stability and resistance to thermal shock, making it suitable for high-temperature applications.
- Silicon Carbide (SiC): Silicon carbide is used in linings where high thermal conductivity and resistance to wear are required. It is particularly useful in furnaces that operate at very high temperatures or where the lining is subject to mechanical stress.
-
Importance of Lining Material Selection:
- Thermal Insulation: The lining material must provide adequate thermal insulation to maintain the furnace's efficiency and reduce energy consumption.
- Chemical Resistance: The material must resist chemical reactions with the molten metal and slag, which can degrade the lining over time.
- Thermal Shock Resistance: The lining must withstand rapid temperature changes without cracking or breaking, which is crucial for maintaining the integrity of the furnace.
- Mechanical Strength: The lining must have sufficient mechanical strength to contain the molten metal and withstand the mechanical stresses during operation.
-
Maintenance and Lifespan:
- Degradation Over Time: Refractory linings degrade over time due to thermal cycling, chemical reactions, and mechanical wear. The operational life of the lining, known as lining life, is a critical factor in furnace maintenance.
- Repair and Replacement: Regular inspection and maintenance are necessary to extend the lining's life. When the lining reaches the end of its operational life, it must be repaired or replaced to ensure the continued safe and efficient operation of the furnace.
-
Special Considerations for Aluminum Furnaces:
- High Frequency and Vibration: Aluminum melting furnaces operate at high frequencies and experience high vibration frequencies of the molten aluminum. This requires linings with excellent thermal shock resistance and mechanical stability.
- Penetrability of Aluminum: Aluminum has strong penetrability, which can lead to the erosion of the lining. Special linings designed for aluminum furnaces are required to withstand these conditions.
- Lining Life: Good quality linings for aluminum furnaces can typically be used for more than 300 heat cycles before needing replacement.
By understanding the specific requirements of the metal being melted and the operational conditions of the furnace, the appropriate lining material can be selected to ensure optimal performance and longevity of the induction furnace.
Summary Table:
Lining Type | Primary Materials | Properties | Applications |
---|---|---|---|
Acid Lining | Silica (SiO₂) | Resistant to acidic slags, thermal insulation, cost-effective | Non-ferrous metals (copper, brass, bronze) |
Basic Lining | Magnesia (MgO), Dolomite | Resistant to basic slags, thermal stability, durability | Ferrous metals (steel, iron) |
Other Materials | Chrome-Magnesia, Alumina-Chrome, Silicon Carbide | Versatile, high thermal stability, wear resistance | High-temperature and specialized applications |
Need help selecting the right lining material for your induction furnace? Contact our experts today for tailored solutions!