Brazing is a versatile joining technique used to create strong, leak-free joints between a wide variety of materials. It is particularly effective for joining exotic base metals such as aluminum, titanium, zirconium, niobium, molybdenum, and tantalum, as well as nickel and iron-based alloys containing aluminum or titanium. Additionally, brazing can join refractory metals, reactive metals, ceramics, and even beryllium. This method is ideal for small, complex parts, large or oddly-shaped components, mass-produced items, and parts that need to withstand high temperatures (350°C or higher). Industries like automotive manufacturing often rely on brazing due to its ability to produce durable and reliable joints.
Key Points Explained:
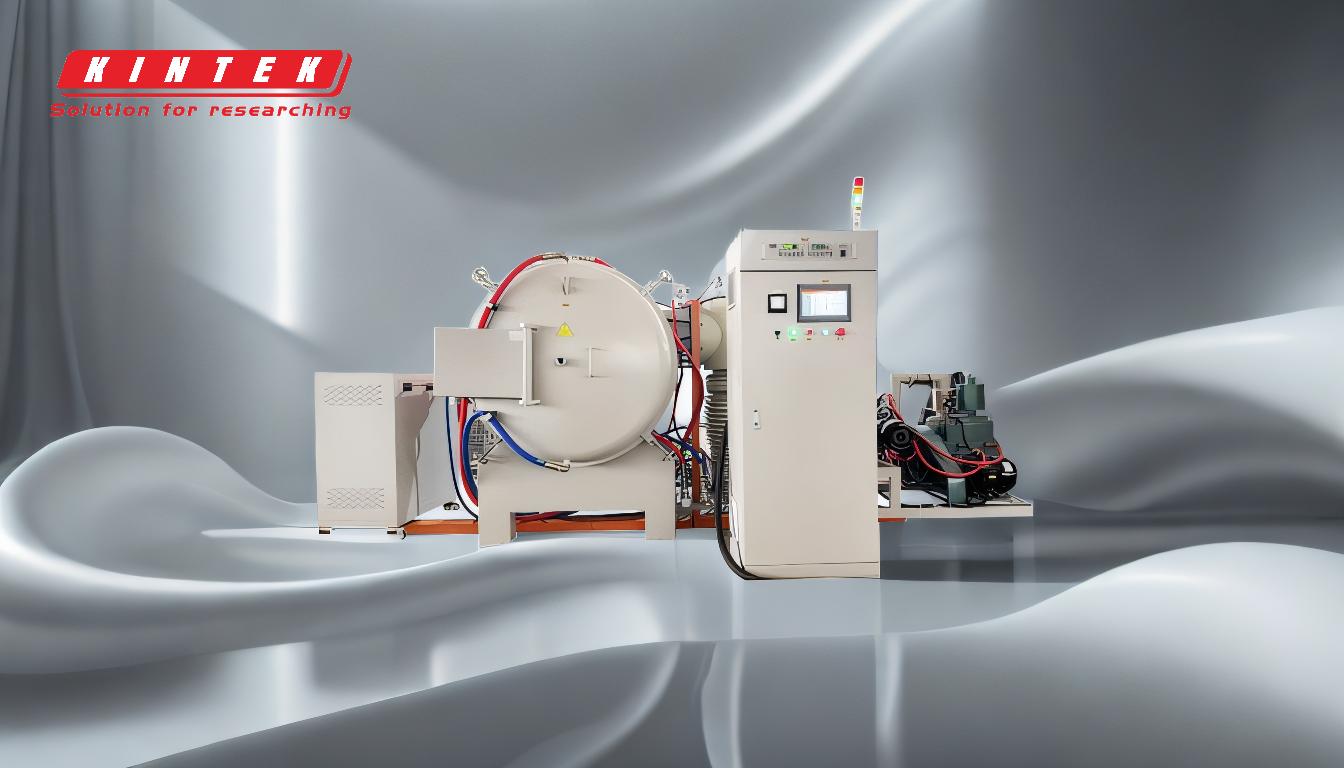
-
Materials Suitable for Brazing:
- Exotic Base Metals: Brazing can join materials like aluminum, titanium, zirconium, niobium, molybdenum, and tantalum. These metals are often challenging to weld due to their unique properties, but brazing provides a reliable alternative.
- Nickel and Iron-Based Alloys: Alloys containing aluminum or titanium, which are commonly used in high-performance applications, can be effectively joined using brazing.
- Refractory and Reactive Metals: These materials, known for their high melting points and resistance to wear, are well-suited for brazing.
- Ceramics and Beryllium: Brazing is one of the few methods capable of joining ceramics and beryllium, which are otherwise difficult to bond using traditional welding techniques.
-
Applications of Brazing:
- Small, Complex Parts: Brazing is ideal for intricate components where precision and strength are critical, such as in electronics or medical devices.
- Large, Oddly-Shaped Parts: The flexibility of brazing allows it to be used on large or irregularly shaped components, such as heat exchangers or aerospace structures.
- Mass-Produced Parts: Due to its efficiency and consistency, brazing is widely used in high-volume manufacturing, including automotive and appliance industries.
- High-Temperature Applications: Brazed joints can withstand extreme temperatures, making them suitable for use in engines, turbines, and other high-heat environments.
-
Advantages of Brazing:
- Strong, Leak-Free Joints: Brazing creates joints that are both mechanically strong and resistant to leakage, which is essential for applications like plumbing or refrigeration systems.
- Versatility: The ability to join dissimilar materials, such as metals to ceramics, makes brazing a highly versatile joining method.
- Durability: Brazed joints are resistant to thermal and mechanical stress, ensuring long-term performance in demanding conditions.
-
Industries Utilizing Brazing:
- Automotive: Many auto parts, such as radiators, air conditioning components, and exhaust systems, are joined using brazing due to its reliability and ability to handle high temperatures.
- Aerospace: The aerospace industry relies on brazing for joining lightweight and high-strength materials used in aircraft and spacecraft.
- Electronics: Brazing is used to create precise and durable connections in electronic components and circuit boards.
- Energy: In power generation and renewable energy systems, brazing is employed to join components that must endure extreme conditions.
By leveraging the unique properties of brazing, manufacturers can achieve high-quality, durable joints across a wide range of materials and applications.
Summary Table:
Category | Materials/Applications |
---|---|
Exotic Base Metals | Aluminum, titanium, zirconium, niobium, molybdenum, tantalum |
Nickel & Iron Alloys | Alloys containing aluminum or titanium |
Refractory Metals | High melting point metals, reactive metals |
Ceramics & Beryllium | Ceramics, beryllium |
Applications | Small/complex parts, large/oddly-shaped components, mass-produced items, high-temp uses |
Industries | Automotive, aerospace, electronics, energy |
Unlock the potential of brazing for your projects—contact our experts today to learn more!