Annealing is a critical heat treatment process used to alter the microstructure of materials, particularly metals, to improve their mechanical and electrical properties. The process involves heating the material to a specific temperature, holding it there to allow defects to repair, and then cooling it slowly. To prevent oxidation and contamination during annealing, specific gases are used to create a protective atmosphere. The most commonly used gases for annealing are high-purity inert gases like argon (Ar) and ultra-high purity hydrogen (H2). These gases ensure a clean environment, free from impurities, and are often used in vacuum annealing processes with precise pressure ranges.
Key Points Explained:
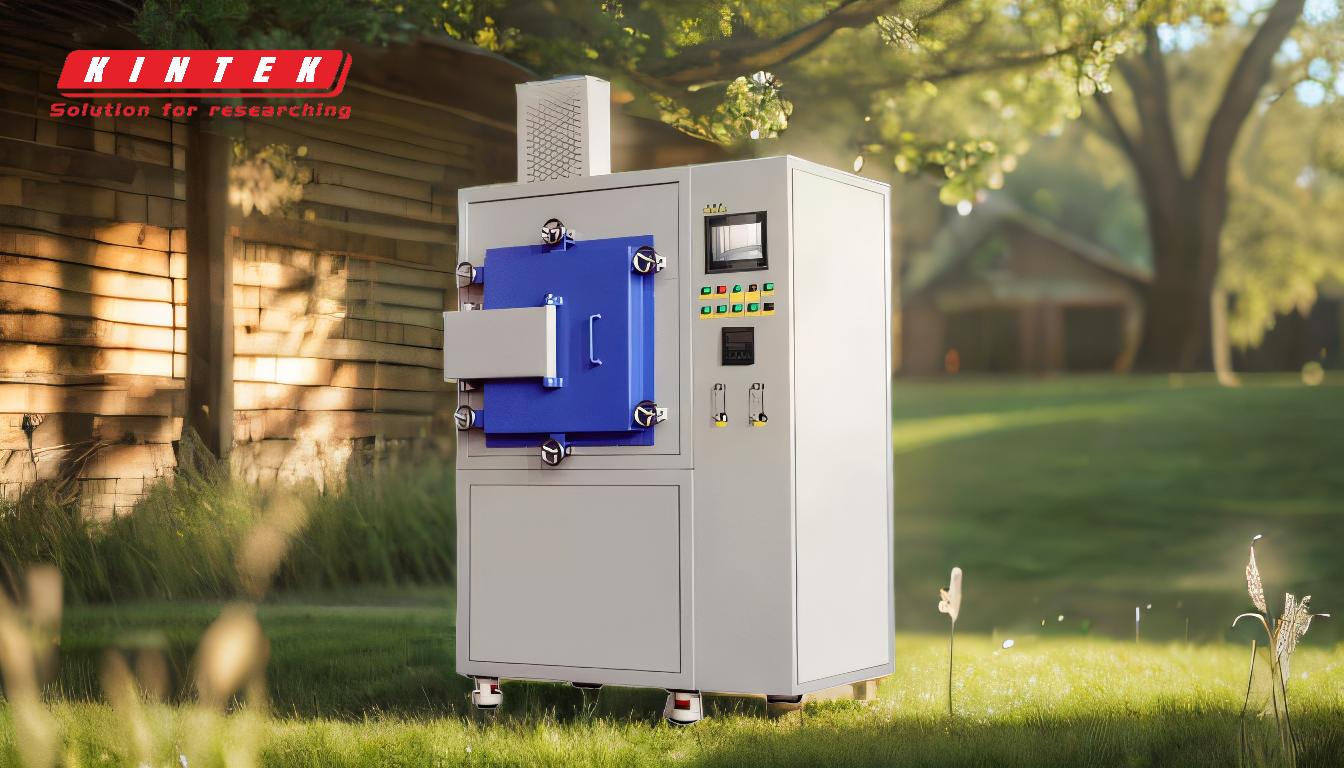
-
Purpose of Annealing:
- Annealing is primarily used to reduce hardness, increase ductility, and eliminate internal stresses in metals.
- It involves heating the metal to a temperature where its crystalline structure becomes fluid but remains solid, allowing defects to repair themselves.
-
Role of Gases in Annealing:
- Gases are used during annealing to create a protective atmosphere that prevents oxidation and contamination of the metal.
- The choice of gas depends on the material being annealed and the desired outcome of the process.
-
Common Gases Used in Annealing:
- Argon (Ar): An inert gas that does not react with the metal, making it ideal for creating a neutral atmosphere. It is often used in vacuum annealing processes.
- Hydrogen (H2): Ultra-high purity hydrogen is used in annealing processes, especially in hydrogen vacuum furnaces. It helps in reducing oxides on the metal surface, leading to a cleaner finish.
-
Purity and Pressure Requirements:
- High-purity inert gases with a purity of more than 99.99% are required for annealing to ensure no impurities affect the metal.
- The pressure range for these gases is typically between 0.05 to 0.07 MPa in vacuum annealing processes.
-
Applications of Different Gases:
- Argon: Commonly used for annealing stainless steels and other alloys where oxidation needs to be minimized.
- Hydrogen: Often used for annealing materials that benefit from oxide reduction, such as certain types of steels and non-ferrous metals.
-
Vacuum Annealing Process:
- In vacuum annealing, the metal is heated in a vacuum or low-pressure environment filled with high-purity inert gases.
- This process ensures that the metal is not exposed to any reactive gases, leading to a cleaner and more controlled annealing process.
-
Benefits of Using High-Purity Gases:
- Prevents oxidation and scaling of the metal surface.
- Ensures consistent and predictable results in the annealing process.
- Reduces the risk of contamination, which can affect the mechanical properties of the metal.
By using high-purity gases like argon and hydrogen in precise pressure ranges, the annealing process can be effectively controlled to achieve the desired material properties. This makes these gases essential components in the heat treatment of metals.
Summary Table:
Aspect | Details |
---|---|
Purpose of Annealing | Reduces hardness, increases ductility, and eliminates internal stresses. |
Common Gases | Argon (Ar) and Ultra-High Purity Hydrogen (H2). |
Purity Requirements | >99.99% purity to prevent impurities. |
Pressure Range | 0.05 to 0.07 MPa in vacuum annealing. |
Applications | Argon for stainless steels; Hydrogen for oxide reduction in steels/metals. |
Benefits | Prevents oxidation, ensures consistent results, and reduces contamination. |
Optimize your annealing process with high-purity gases—contact our experts today!