Heat treatment processes are essential for altering the mechanical and physical properties of steel, making it suitable for various applications. These processes involve precise heating and cooling cycles to manipulate the microstructure of the steel, thereby enhancing properties such as hardness, strength, ductility, toughness, and wear resistance. Common heat treatment methods include annealing, case hardening, tempering, carburizing, precipitation hardening, and quenching. Each process targets specific properties, such as increasing surface hardness, improving ductility, or enhancing wear resistance, by controlling factors like temperature, cooling rate, and atmosphere. These treatments ensure that steel meets the desired performance criteria for its intended use.
Key Points Explained:
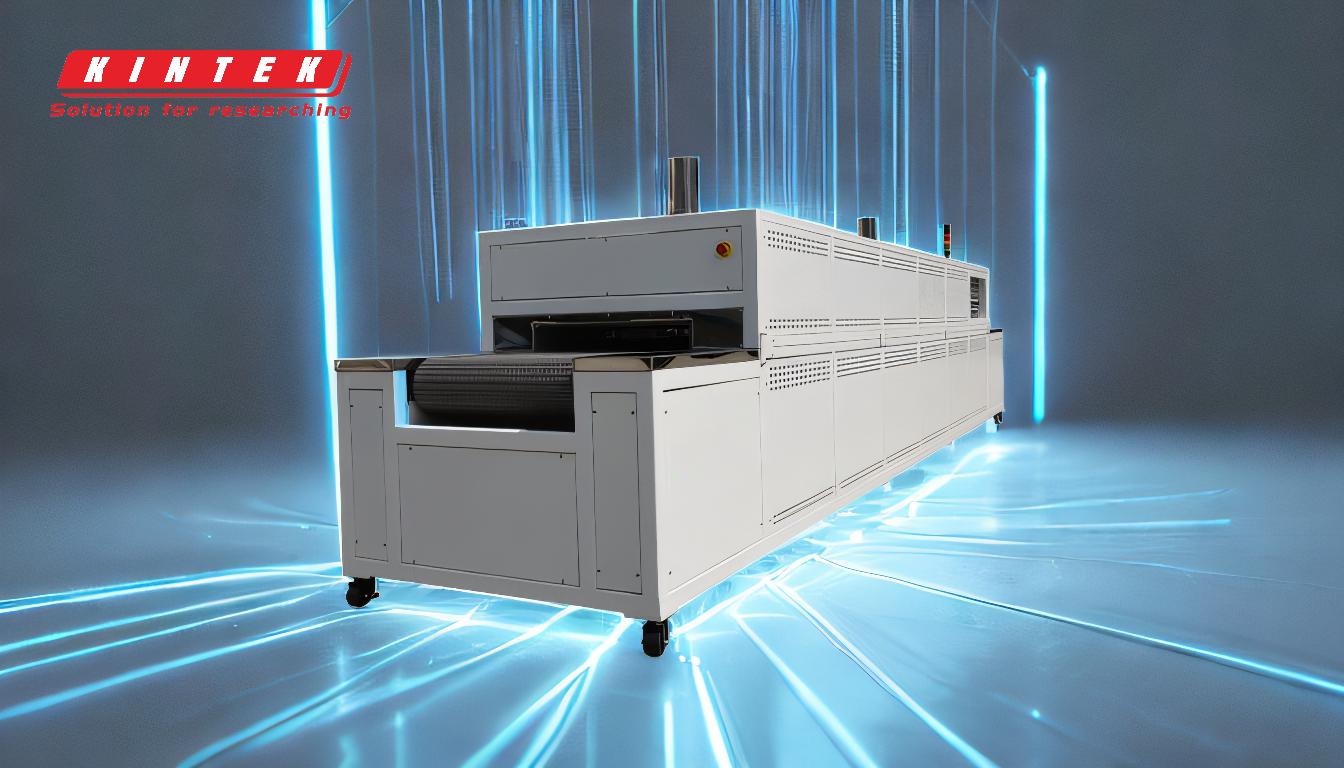
-
Annealing:
- Purpose: Softens steel, improves ductility, and reduces internal stresses.
- Process: The steel is heated to a specific temperature (above its recrystallization temperature) and then slowly cooled in a furnace.
- Outcome: Results in a more workable material with improved machinability and reduced brittleness.
-
Case Hardening:
- Purpose: Increases surface hardness while maintaining a tough core.
- Process: The surface of the steel is infused with carbon or nitrogen (via carburizing or nitriding) and then hardened through quenching.
- Outcome: Enhances wear resistance and durability, making it ideal for components like gears and bearings.
-
Tempering:
- Purpose: Balances hardness and toughness.
- Process: After hardening, the steel is reheated to a lower temperature and then cooled at a controlled rate.
- Outcome: Reduces brittleness and improves toughness, making the steel less prone to cracking under stress.
-
Carburizing:
- Purpose: Increases surface hardness by adding carbon to the steel's surface.
- Process: The steel is heated in a carbon-rich environment, allowing carbon atoms to diffuse into the surface.
- Outcome: Creates a hard, wear-resistant surface while maintaining a softer, tougher core.
-
Precipitation Hardening:
- Purpose: Increases strength and hardness through the formation of precipitates.
- Process: The steel is heated to a high temperature, cooled, and then aged at a lower temperature to allow precipitates to form.
- Outcome: Enhances strength and hardness without significantly reducing ductility.
-
Quenching:
- Purpose: Rapidly cools steel to achieve high hardness.
- Process: The steel is heated to a high temperature and then rapidly cooled in water, oil, or air.
- Outcome: Produces a hard, brittle structure that can be tempered to achieve the desired balance of hardness and toughness.
-
Brazing:
- Purpose: Joins metals using a filler material.
- Process: Metals are heated to a high temperature in a controlled atmosphere (e.g., pure hydrogen or dissociated ammonia) to melt the filler material.
- Outcome: Creates strong, durable joints without melting the base metals.
-
Bright Annealing:
- Purpose: Minimizes oxidation and maintains a bright surface finish.
- Process: Steel is annealed in a protective atmosphere (e.g., pure hydrogen, nitrogen, or argon) to prevent oxidation.
- Outcome: Produces a clean, oxidation-free surface with improved physical properties.
-
Through-Hardening:
- Purpose: Hardens the entire cross-section of the steel.
- Process: The steel is heated uniformly and then quenched to achieve consistent hardness throughout.
- Outcome: Provides uniform hardness and strength, suitable for components requiring high wear resistance.
-
Sintering:
- Purpose: Bonds metal particles at high temperatures.
- Process: Metal powders are heated to just below their melting point in a protective atmosphere.
- Outcome: Creates a dense, strong material with controlled porosity, often used in powder metallurgy.
By understanding these heat treatment processes, manufacturers can tailor the properties of steel to meet specific application requirements, ensuring optimal performance and longevity.
Summary Table:
Process | Purpose | Outcome |
---|---|---|
Annealing | Softens steel, improves ductility, reduces internal stresses | Workable material with improved machinability and reduced brittleness |
Case Hardening | Increases surface hardness while maintaining a tough core | Enhanced wear resistance and durability for components like gears |
Tempering | Balances hardness and toughness | Reduced brittleness, improved toughness, and less prone to cracking |
Carburizing | Increases surface hardness by adding carbon | Hard, wear-resistant surface with a softer, tougher core |
Precipitation Hardening | Increases strength and hardness through precipitate formation | Enhanced strength and hardness without significant ductility loss |
Quenching | Rapidly cools steel to achieve high hardness | Hard, brittle structure that can be tempered for balance |
Brazing | Joins metals using a filler material | Strong, durable joints without melting base metals |
Bright Annealing | Minimizes oxidation and maintains a bright surface finish | Clean, oxidation-free surface with improved physical properties |
Through-Hardening | Hardens the entire cross-section of the steel | Uniform hardness and strength for high wear resistance |
Sintering | Bonds metal particles at high temperatures | Dense, strong material with controlled porosity for powder metallurgy |
Optimize your steel with the right heat treatment—contact our experts today for tailored solutions!