Normalizing is a heat treatment process used to refine the grain structure of metals, improve mechanical properties, and relieve internal stresses. It involves heating the material to a temperature between 750-980°C (1320-1796°F), depending on the carbon content, holding it at that temperature for a specific duration, and then cooling it in air. This process enhances ductility, toughness, and uniformity in the material's microstructure. Normalizing is often applied to steels and other metals to prepare them for further processing or to achieve desired mechanical properties. It is distinct from other heat treatment methods like annealing, quenching, or tempering, as it involves faster cooling rates, which result in a finer grain structure.
Key Points Explained:
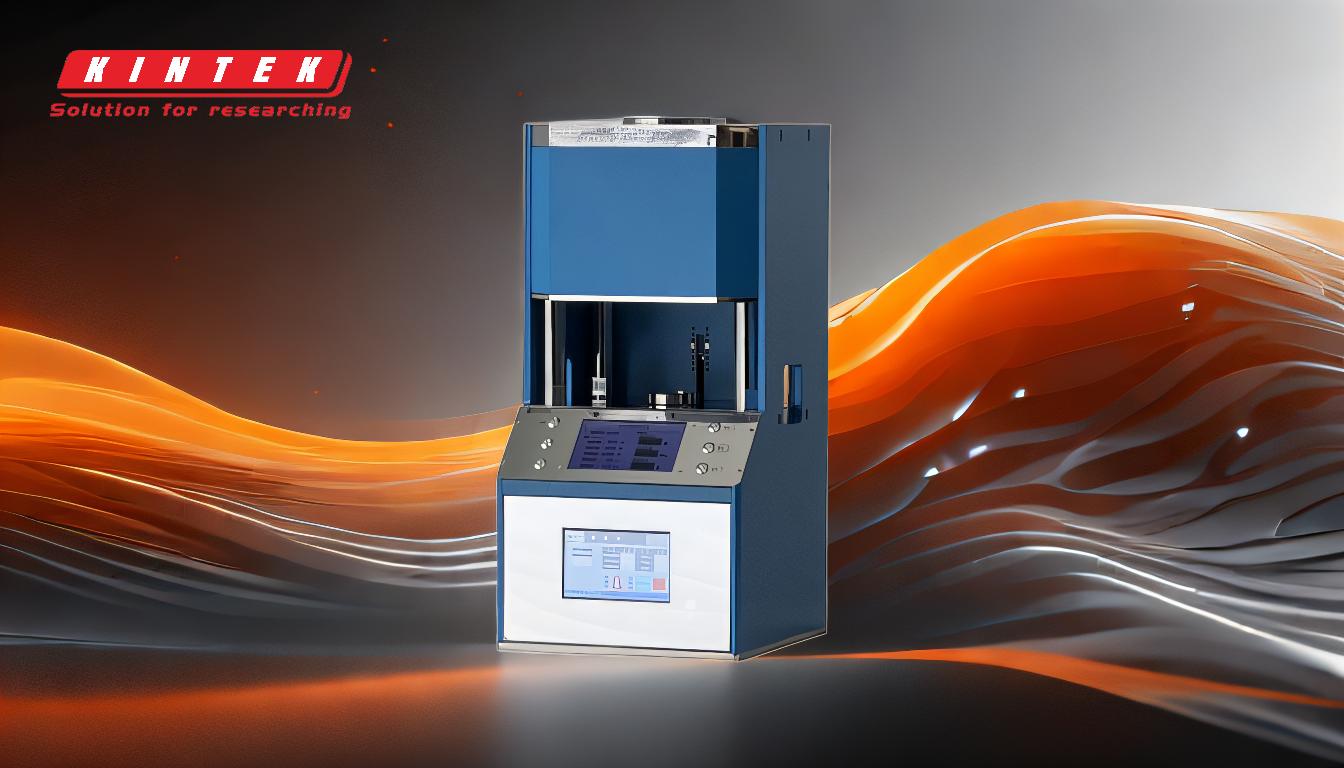
-
Definition and Purpose of Normalizing:
- Normalizing is a heat treatment process aimed at refining the grain structure of metals.
- It improves mechanical properties such as ductility, toughness, and uniformity in the microstructure.
- It also helps relieve internal stresses caused by prior manufacturing processes like casting, forging, or welding.
-
Temperature Range for Normalizing:
- The material is heated to a temperature range of 750-980°C (1320-1796°F).
- The exact temperature depends on the carbon content of the metal. Higher carbon content typically requires lower temperatures within this range.
-
Cooling Process:
- After heating, the material is cooled in still air, which is faster than the controlled cooling used in annealing.
- This faster cooling rate results in a finer grain structure compared to annealing, leading to improved mechanical properties.
-
Comparison with Other Heat Treatment Methods:
- Annealing: Involves slower cooling rates, resulting in softer and more ductile materials but with coarser grain structures.
- Quenching: Involves rapid cooling, often in water or oil, to achieve high hardness but may lead to brittleness.
- Tempering: Follows quenching to reduce brittleness and improve toughness by reheating to a lower temperature.
- Normalizing strikes a balance between annealing and quenching, offering improved mechanical properties without excessive brittleness.
-
Applications of Normalizing:
- Commonly used for steels and other metals to prepare them for further machining or heat treatment.
- Ideal for improving the mechanical properties of components subjected to high stress or wear.
- Often applied to forgings, castings, and welded structures to ensure uniformity and relieve internal stresses.
-
Advantages of Normalizing:
- Enhances ductility and toughness, making the material more suitable for forming and machining.
- Produces a more uniform microstructure, which improves consistency in mechanical properties.
- Relieves internal stresses, reducing the risk of distortion or cracking during subsequent processing.
-
Limitations of Normalizing:
- Not suitable for all materials, as some alloys may require specific heat treatment processes.
- The faster cooling rate may not be ideal for achieving the softest possible material, which is often required for certain applications.
By understanding these key points, a purchaser of equipment or consumables can make informed decisions about when and how to use normalizing as part of their manufacturing or processing workflow.
Summary Table:
Aspect | Details |
---|---|
Purpose | Refines grain structure, improves mechanical properties, relieves stresses. |
Temperature Range | 750-980°C (1320-1796°F), depending on carbon content. |
Cooling Process | Air cooling, faster than annealing, results in finer grain structure. |
Applications | Steels, forgings, castings, welded structures. |
Advantages | Enhances ductility, toughness, and uniformity; relieves internal stresses. |
Limitations | Not suitable for all materials; may not achieve softest material. |
Discover how normalizing can optimize your metal processing—contact us today for expert guidance!