Abnormal grain growth during sintering refers to the phenomenon where certain grains grow significantly larger than the surrounding grains, leading to a non-uniform microstructure. This occurs due to localized differences in grain boundary energy, mobility, or driving forces, often exacerbated by impurities, temperature gradients, or uneven densification. Abnormal grain growth is generally undesirable in ceramics and metals because it can degrade mechanical properties, such as hardness and strength, by disrupting the uniform grain structure. Understanding and controlling this phenomenon is critical for optimizing sintering processes and achieving high-quality, defect-free materials.
Key Points Explained:
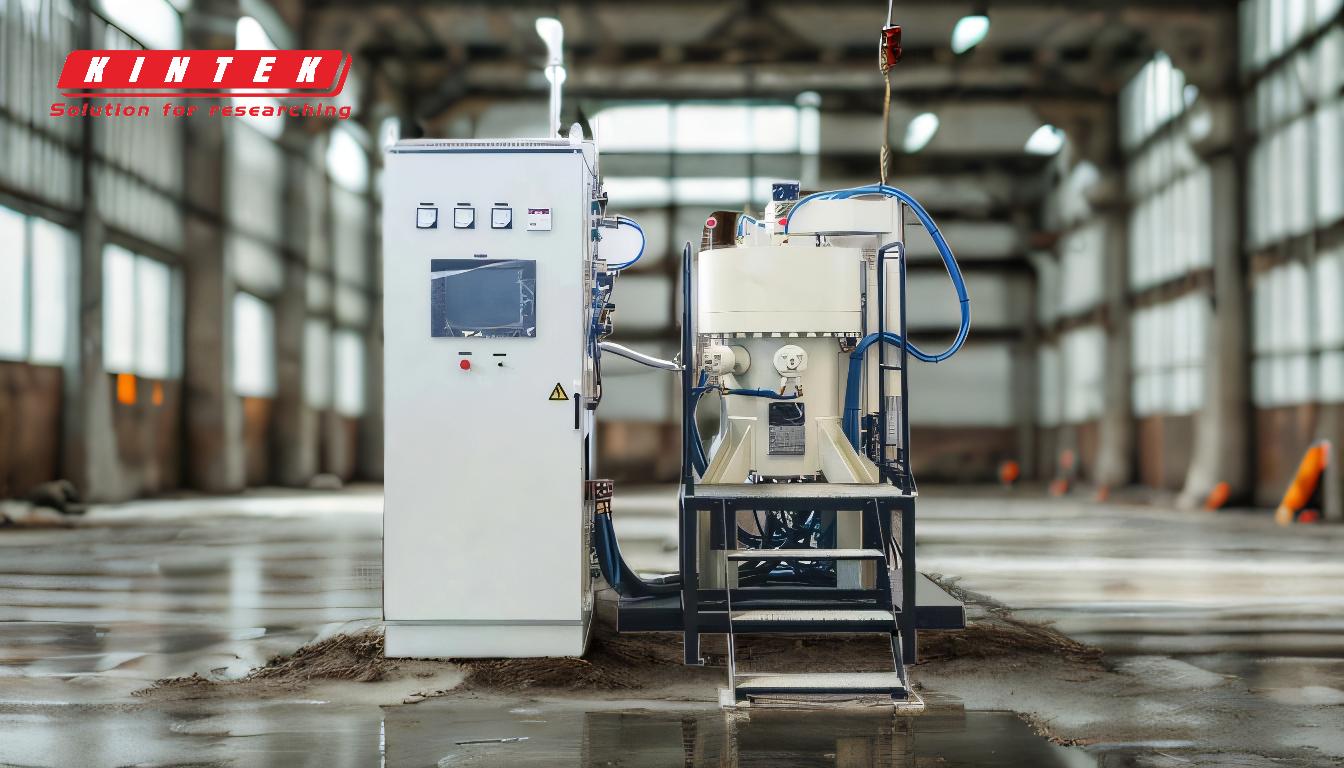
-
Definition of Abnormal Grain Growth:
- Abnormal grain growth (AGG) occurs when a few grains grow disproportionately larger than the surrounding matrix of grains during sintering.
- This is distinct from normal grain growth, where grains grow uniformly at a similar rate.
- AGG results in a bimodal grain size distribution, which can negatively impact material properties.
-
Causes of Abnormal Grain Growth:
- Localized Energy Differences: Variations in grain boundary energy or mobility can cause certain grains to grow faster.
- Impurities and Inclusions: Impurities or second-phase particles can pin grain boundaries, but if these pinning effects are uneven, they can trigger AGG.
- Temperature Gradients: Non-uniform heating during sintering can create regions where grains grow faster.
- Driving Forces: Differences in driving forces, such as surface energy or strain energy, can lead to selective grain growth.
-
Impact on Material Properties:
- Mechanical Properties: AGG can reduce hardness and strength due to the Hall-Petch effect, which states that finer grains generally lead to stronger materials.
- Density and Porosity: Rapidly growing grains can trap pores, leading to incomplete densification and reduced material performance.
- Thermal and Electrical Properties: Non-uniform grain sizes can affect thermal conductivity and electrical resistivity, making the material less predictable in applications.
-
Detection and Measurement:
- Microscopy: Techniques like scanning electron microscopy (SEM) or optical microscopy are used to observe grain size distribution and identify AGG.
- Dilatometry: Tools like Linseis push rod dilatometers can monitor dimensional changes during sintering, helping to detect uneven densification that may correlate with AGG.
-
Prevention and Control:
- Optimized Sintering Parameters: Controlling heating rates, holding times, and cooling rates can minimize temperature gradients and reduce the likelihood of AGG.
- Grain Growth Inhibitors: Adding dopants or second-phase particles can stabilize grain boundaries and prevent selective grain growth.
- Uniform Powder Compaction: Ensuring even density in the green body before sintering can reduce driving forces for AGG.
-
Relevance in Ceramics and Metals:
- In ceramics, AGG is particularly problematic because it can lead to reduced mechanical strength and increased brittleness.
- In metals, AGG can affect ductility and fatigue resistance, making it crucial to control in high-performance applications.
By understanding the mechanisms and consequences of abnormal grain growth, manufacturers can implement strategies to mitigate its effects and produce materials with consistent and desirable properties.
Summary Table:
Aspect | Details |
---|---|
Definition | Disproportionate growth of a few grains during sintering, leading to non-uniform microstructure. |
Causes | Localized energy differences, impurities, temperature gradients, uneven densification. |
Impact on Properties | Reduces hardness, strength, and density; affects thermal and electrical properties. |
Detection Methods | Microscopy (SEM, optical), dilatometry. |
Prevention Strategies | Optimized sintering parameters, grain growth inhibitors, uniform powder compaction. |
Relevance | Critical in ceramics (reduced strength) and metals (affects ductility, fatigue resistance). |
Need help controlling abnormal grain growth in your sintering process? Contact our experts today for tailored solutions!