Brazing is a versatile joining process used across various industries due to its ability to create strong, leak-proof, and durable bonds between dissimilar materials. It is particularly advantageous for applications requiring precision, consistency, and the ability to join metals that are difficult to weld. Common uses include metal housings, electromechanical components, pipe fittings, automotive engine parts, HVAC systems, and complex assemblies like hydraulic fittings and heat exchangers. Vacuum brazing, in particular, is ideal for intricate components, as it minimizes distortion and ensures high-quality results, making it suitable for industries like aerospace, medical, and scientific engineering.
Key Points Explained:
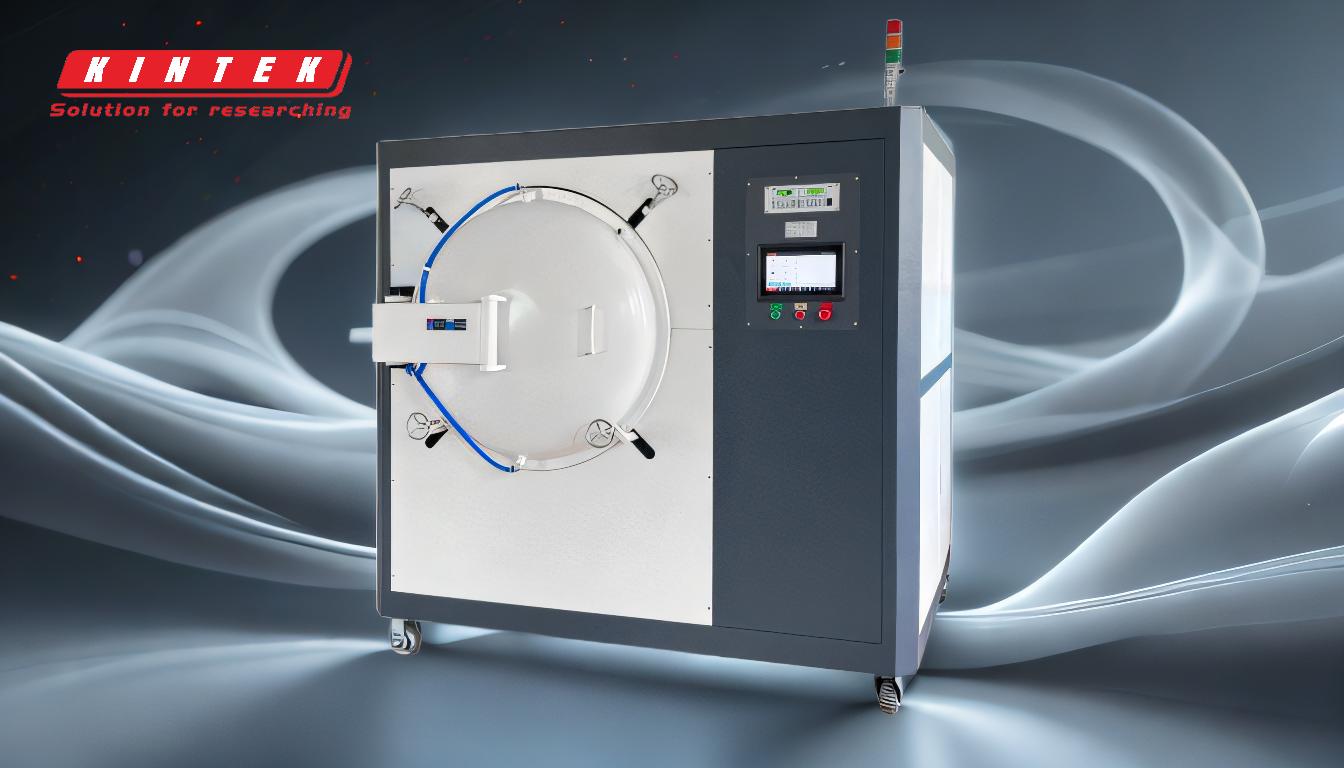
-
Versatility in Joining Dissimilar Materials:
- Brazing is highly effective for joining dissimilar metals, such as copper to steel or aluminum to stainless steel, which are often challenging to weld. This makes it a preferred method in industries like HVAC and automotive manufacturing, where different materials are frequently combined.
-
Strong and Leak-Proof Joints:
- The brazing process creates joints that are not only strong but also leak-proof, making it ideal for applications like pipe fittings, hydraulic systems, and heat exchangers, where sealing integrity is critical.
-
Precision and Consistency in Complex Components:
- Vacuum brazing, in particular, offers precise control over the heat cycle, reducing the risk of part distortion. This makes it suitable for complex components in industries like aerospace and medical engineering, where high precision and reproducibility are essential.
-
Wide Range of Applications:
- Brazing is used in a variety of industries and applications, including:
- Automotive: Engine components, fuel systems, and exhaust systems.
- HVAC: Heat exchangers and refrigeration systems.
- Electromechanical: Housings and assemblies for electronic devices.
- Medical and Scientific: Instruments and equipment requiring high precision and reliability.
- Brazing is used in a variety of industries and applications, including:
-
Cost-Effective for Mass Production:
- Brazing is a scalable process, making it cost-effective for mass production. Its ability to reproduce parts consistently at scale is particularly beneficial for industries like automotive and general engineering.
-
Minimal Distortion and High-Quality Results:
- Unlike welding, brazing operates at lower temperatures, reducing the risk of warping or distortion in the base materials. This ensures high-quality, consistent results, especially in vacuum brazing, which is critical for industries like aerospace and medical device manufacturing.
By understanding these key points, equipment and consumable purchasers can better evaluate whether brazing is the right joining method for their specific applications. Its ability to join dissimilar materials, create strong and leak-proof joints, and produce high-quality results makes it a valuable process across a wide range of industries.
Summary Table:
Key Benefits of Brazing | Applications |
---|---|
Joins dissimilar materials | HVAC systems, automotive components, electromechanical assemblies |
Creates strong, leak-proof joints | Pipe fittings, hydraulic systems, heat exchangers |
Precision in complex components | Aerospace, medical, and scientific engineering |
Cost-effective for mass production | Automotive manufacturing, general engineering |
Minimal distortion, high quality | Intricate components in aerospace and medical device manufacturing |
Want to learn more about how brazing can benefit your industry? Contact us today for expert advice!