High temperature brazing is a specialized joining process used to bond materials, typically metals or ceramics, at elevated temperatures. This process involves the use of a filler metal that melts at a temperature above 450°C (842°F) and flows into the joint by capillary action, creating a strong, durable bond. High temperature brazing is commonly used in industries where components must withstand extreme conditions, such as aerospace, automotive, and energy sectors. The process requires precise control of temperature and environment, often carried out in a high temperature furnace to ensure optimal results.
Key Points Explained:
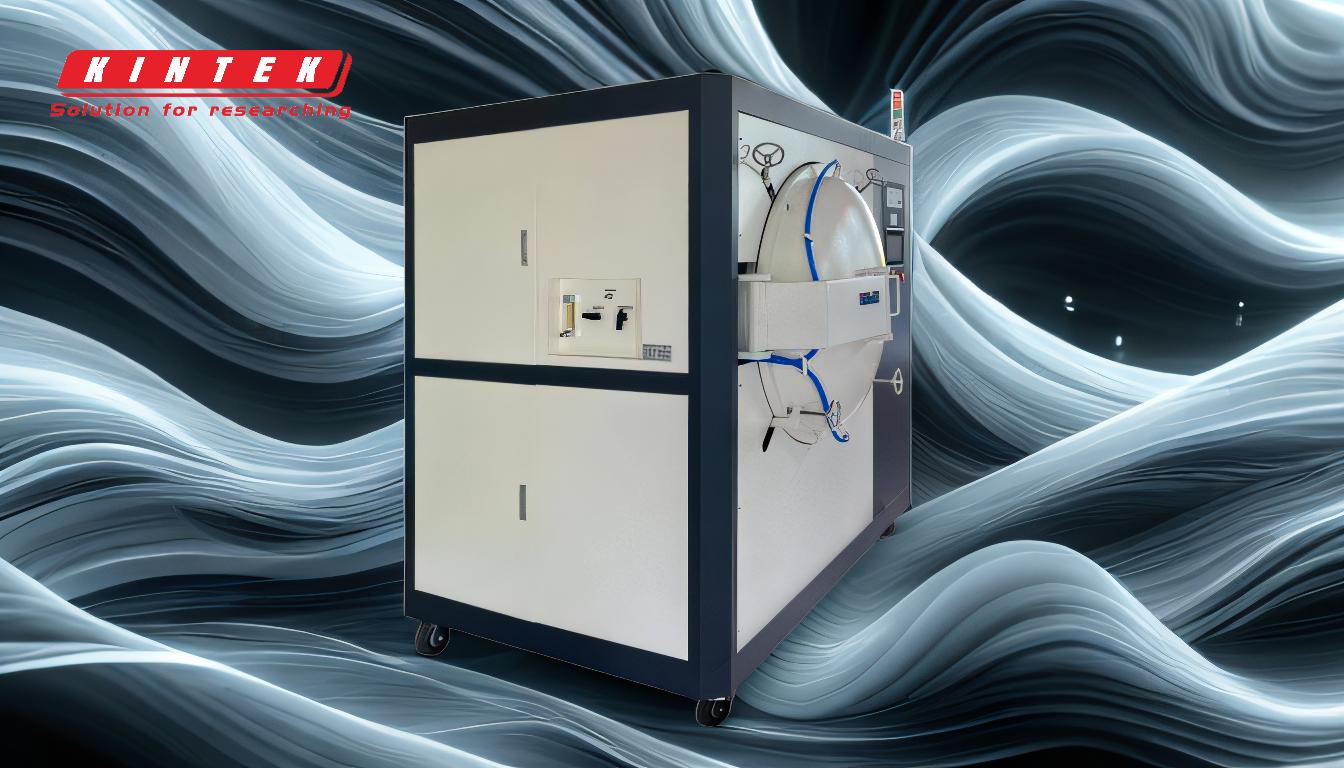
-
Definition of High Temperature Brazing:
- High temperature brazing is a metal-joining process where a filler metal with a melting point above 450°C is used to bond two or more base materials.
- The filler metal flows into the joint by capillary action, creating a strong and durable bond.
-
Applications of High Temperature Brazing:
- Aerospace Industry: Used for joining components that must withstand high stress and temperature, such as turbine blades and heat exchangers.
- Automotive Industry: Applied in the manufacturing of exhaust systems and other high-temperature components.
- Energy Sector: Utilized in the production of solar panels, nuclear reactors, and other energy-related equipment.
- Electronics: Used for bonding components in high-power electronic devices that generate significant heat.
-
Materials Involved:
- Base Materials: Typically metals like stainless steel, nickel alloys, titanium, and ceramics.
- Filler Metals: Commonly used filler metals include silver, copper, nickel, and gold-based alloys, chosen based on the required properties of the joint.
-
Process Requirements:
- Temperature Control: Precise temperature control is crucial, often achieved using a high temperature furnace.
- Atmosphere Control: The process may require a controlled atmosphere, such as vacuum or inert gas, to prevent oxidation and ensure a clean joint.
- Surface Preparation: Proper cleaning and preparation of the surfaces to be joined are essential for achieving a strong bond.
-
Advantages of High Temperature Brazing:
- Strong Joints: Produces joints with high strength and durability.
- Versatility: Can join dissimilar materials and complex geometries.
- Minimal Distortion: The process causes minimal distortion to the base materials, preserving their structural integrity.
-
Challenges and Considerations:
- Material Compatibility: Ensuring compatibility between the base materials and the filler metal is critical.
- Process Control: Requires precise control of temperature and atmosphere to achieve consistent results.
- Cost: The process can be more expensive than other joining methods due to the need for specialized equipment and materials.
-
Future Trends:
- Advanced Materials: Development of new filler metals and base materials to enhance performance and expand application possibilities.
- Automation: Increasing use of automated systems for improved precision and efficiency.
- Sustainability: Focus on environmentally friendly processes and materials to reduce the environmental impact.
In summary, high temperature brazing is a critical process in various high-tech industries, offering strong, durable joints for components that must endure extreme conditions. The use of a high temperature furnace is essential for achieving the precise temperature control required for successful brazing. As technology advances, we can expect further innovations in materials and processes, enhancing the capabilities and applications of high temperature brazing.
Summary Table:
Aspect | Details |
---|---|
Definition | Joining process using filler metals melting above 450°C for strong bonds. |
Applications | Aerospace, automotive, energy, and electronics industries. |
Materials | Base: Stainless steel, nickel alloys, titanium. Filler: Silver, copper, etc. |
Process Requirements | Precise temperature control, controlled atmosphere, surface preparation. |
Advantages | Strong joints, versatility, minimal distortion. |
Challenges | Material compatibility, process control, cost. |
Future Trends | Advanced materials, automation, sustainability. |
Discover how high temperature brazing can enhance your projects—contact our experts today!