Sintering is a critical process in ceramic manufacturing, where high temperatures are used to densify ceramic powders or green billets, transforming them into durable, high-strength materials. High-temperature sintering, specifically, involves heating ceramic materials at elevated temperatures, often above their standard sintering temperature, to enhance their physical properties. This process results in the bonding of solid particles, grain growth, and reduction of voids, leading to increased density, reduced porosity, and improved mechanical strength. The process is essential for producing ceramics that are resistant to extreme conditions, such as high temperatures, UV rays, and abrasion. High-temperature sintering is more energy-intensive and costly but yields superior material properties, making it ideal for applications requiring high durability and performance.
Key Points Explained:
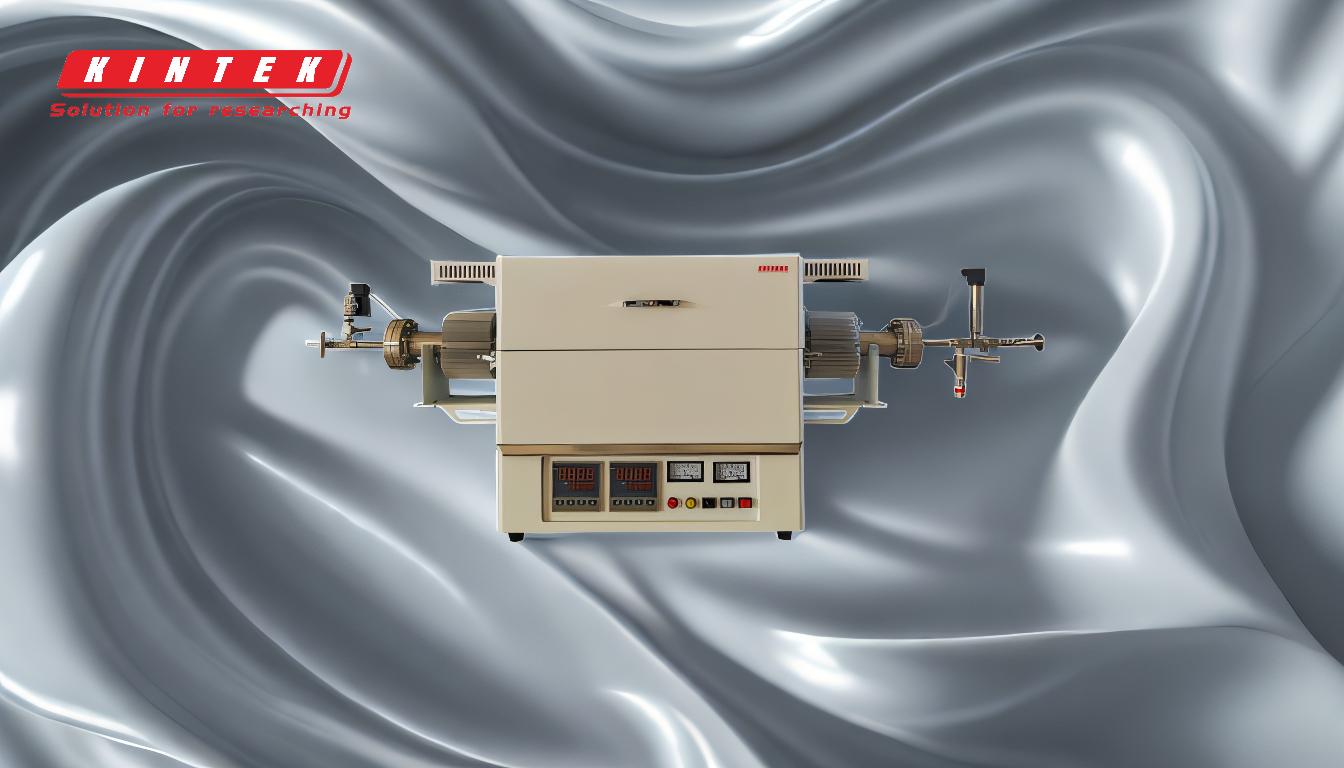
-
Definition of High-Temperature Sintering:
- High-temperature sintering is a process where ceramic materials are heated to temperatures significantly higher than their standard sintering temperature (often 100-250 °F higher). This elevated temperature facilitates the bonding of ceramic particles, leading to the formation of a dense, strong, and durable polycrystalline structure.
- The process is particularly effective in reducing porosity and increasing the density of the ceramic material, which enhances its mechanical properties.
-
Steps Involved in High-Temperature Sintering:
- Mixing and Slurry Formation: Water, binder, deflocculant, and unfired ceramic powder are mixed to form a slurry.
- Spray Drying: The slurry is spray-dried to create a fine powder.
- Pressing: The spray-dried powder is pressed into a mold to form a green body.
- Binder Burn-Off: The green body is heated at a low temperature to remove the binder.
- High-Temperature Sintering: The green body is then sintered at high temperatures, typically above 2050 °F, to fuse the ceramic particles and create a dense, strong material.
-
Benefits of High-Temperature Sintering:
- Enhanced Material Properties: High-temperature sintering improves tensile strength, bending fatigue strength, and impact energy, making the ceramic material more durable and resistant to mechanical stress.
- Reduced Porosity: The process significantly reduces the porosity of the ceramic, leading to a denser and more uniform structure.
- Improved Resistance to Environmental Factors: Sintered ceramics are highly resistant to UV rays, extreme temperatures, water, stains, and abrasion, making them suitable for harsh environments.
-
Applications of High-Temperature Sintered Ceramics:
- Industrial Components: High-temperature sintered ceramics are used to manufacture gears, bearings, rotors, and other components that require high strength and durability.
- Pottery and Decorative Items: The process is also used in the production of high-quality pottery and decorative ceramic items, where durability and aesthetic appeal are important.
- Advanced Ceramics: In industries such as aerospace, automotive, and electronics, high-temperature sintered ceramics are used for components that must withstand extreme conditions and high performance requirements.
-
Challenges and Considerations:
- Energy Intensity: High-temperature sintering requires more energy compared to standard sintering processes, making it more expensive.
- Equipment Requirements: The process demands specialized furnaces capable of reaching and maintaining extremely high temperatures, which can be costly to operate and maintain.
- Material Shrinkage: The sintering process causes the ceramic material to shrink as the particles bond and the structure consolidates, which must be accounted for in the design and manufacturing process.
-
Comparison with Standard Sintering:
- Temperature: High-temperature sintering involves heating the material at temperatures 100-250 °F higher than standard sintering, which typically occurs around 2050 °F for iron-heavy metals.
- Material Properties: While standard sintering also improves material properties, high-temperature sintering offers superior enhancements in strength, density, and durability.
- Cost: High-temperature sintering is more expensive due to the increased energy consumption and specialized equipment required.
In summary, high-temperature sintering is a specialized process that significantly enhances the properties of ceramic materials, making them suitable for demanding applications. Despite its higher cost and energy requirements, the process is invaluable for producing high-performance ceramics that meet the rigorous demands of various industries.
Summary Table:
Aspect | Details |
---|---|
Definition | Heating ceramics above standard sintering temps (100-250 °F higher) for enhanced properties. |
Key Steps | Mixing, spray drying, pressing, binder burn-off, and high-temperature sintering. |
Benefits | Increased strength, reduced porosity, and improved resistance to extreme conditions. |
Applications | Industrial components, pottery, aerospace, automotive, and electronics. |
Challenges | High energy use, specialized equipment, and material shrinkage. |
Comparison with Standard | Higher temps, superior properties, but more costly and energy-intensive. |
Ready to enhance your ceramic manufacturing process? Contact us today to learn more about high-temperature sintering solutions!