Isostatic pressing of polymers is a manufacturing process that involves applying uniform pressure from all directions to a polymer material, typically in powder form, enclosed in a flexible mold. This technique ensures even compaction and density distribution, resulting in high-quality, dense products. The process can be performed using either the wet-bag or dry-bag technique, depending on the application. Cold isostatic pressing, a subset of this process, is particularly useful for shaping and consolidating powdered polymers, creating intricate shapes, and achieving high green density. It is widely used in industries such as battery production, where it helps create solid electrolytes and other components.
Key Points Explained:
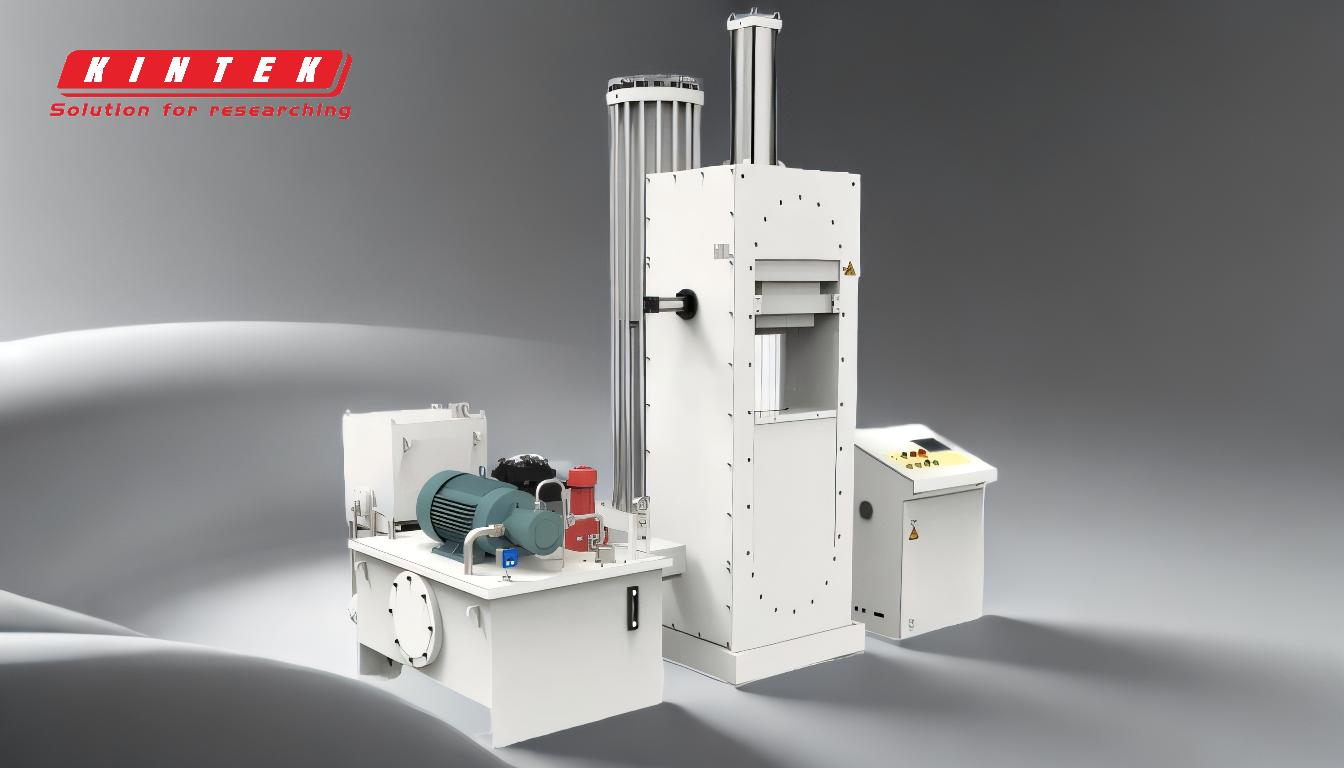
-
Definition of Isostatic Pressing:
- Isostatic pressing is a process where a material, such as polymer powder, is placed in a flexible mold and subjected to uniform hydrostatic pressure from all directions. This ensures even compaction and density distribution, leading to high-quality products. The process can be performed using either the wet-bag or dry-bag technique.
-
Wet-Bag vs. Dry-Bag Techniques:
- Wet-Bag Technique: In this method, the flexible mold containing the polymer powder is submerged in a pressure vessel filled with a pressurizing fluid. The pressure is applied uniformly from all sides, and the mold is removed after pressing.
- Dry-Bag Technique: Here, the flexible mold is fixed inside the pressure vessel, and the powder is loaded without removing the mold. This technique is more suitable for continuous production and is often used in industries where precision and repeatability are crucial.
-
Applications in Polymer Processing:
- Isostatic pressing is used to create thin, dense solid electrolyte layers and integrate multiple layers (cathode, solid electrolyte, and anode) into a dense, tri-layer system. This is particularly useful in the production of solid-state batteries (SSBs).
- The process is also employed to produce garnet-based ultra-thin flexible composite solid electrolyte membranes, which are essential for advanced battery technologies.
-
Cold Isostatic Pressing:
- Cold isostatic pressing (CIP) involves subjecting the polymer material to uniform pressure from all sides by immersing it in a high-pressure fluid medium. This method is effective for shaping and consolidating powdered materials, creating intricate shapes, and achieving high green density.
- CIP is commonly used for parts that are too large to be pressed in uniaxial presses and do not require high precision in the sintered state. It is also used for wear and metal forming tools.
-
Advantages of Isostatic Pressing:
- Uniform Pressure Distribution: The pressure transmitted by the medium is equal in all directions, ensuring uniform compaction force and density distribution.
- Minimal Friction: The friction between the powder and the die wall is minimal, which further enhances the uniformity of the final product.
- Improved Product Performance: The uniform density and compaction lead to improved mechanical properties and overall performance of the polymer product.
-
Steps in the Isostatic Pressing Process:
- Loading: The polymer powder is loaded into a flexible mold.
- Sealing: The mold is sealed to prevent leakage of the powder or pressurizing fluid.
- Pressurizing: The sealed mold is placed in a pressure vessel, and uniform pressure is applied via a liquid medium.
- Depressurizing: After the desired pressure is achieved, the pressure is released.
- Removing: The compacted polymer body is removed from the mold.
-
Industrial Uses:
- Isostatic pressing is widely used in the densification of metals, ceramics, composites, and polymers. In battery production, it is used for the compaction of cathode, anode, composite materials, ceramics, carbon-based materials, and solid electrolytes.
- The cold isostatic pressing machine is particularly valuable in industries requiring high-density, complex-shaped components.
In summary, isostatic pressing of polymers, especially through cold isostatic pressing, offers a versatile and efficient method for producing high-density, uniform components. Its applications span various industries, including battery production, where it plays a crucial role in creating advanced materials like solid electrolytes. The process's ability to deliver uniform pressure and minimal friction ensures superior product performance and quality.
Summary Table:
Aspect | Details |
---|---|
Definition | Uniform hydrostatic pressure applied to polymer powder in a flexible mold. |
Techniques | Wet-bag (submerged mold) or dry-bag (fixed mold). |
Applications | Solid-state batteries, garnet-based electrolyte membranes, and more. |
Cold Isostatic Pressing | Shapes and consolidates powdered polymers for high-density components. |
Advantages | Uniform density, minimal friction, and improved product performance. |
Process Steps | Loading, sealing, pressurizing, depressurizing, and removing. |
Industrial Uses | Densification of metals, ceramics, composites, and polymers. |
Discover how isostatic pressing can enhance your polymer manufacturing—contact us today!