Sintering is a critical process in materials science and manufacturing, where powder particles are fused together through diffusion reactions to form a solid piece. This process is driven by the reduction in surface energy as particles form necks and densify. Sintering typically occurs in stages: shaping the powder with a bonding agent, removing the bonding agent through heating, and then fusing the particles at high temperatures. The process can be enhanced by using specialized equipment like vacuum or hot press sintering furnaces, which prevent oxidation and contamination, ensuring high-quality results. Sintering is widely used in industries such as metallurgy and ceramics, where it transforms powdered materials into durable, functional components.
Key Points Explained:
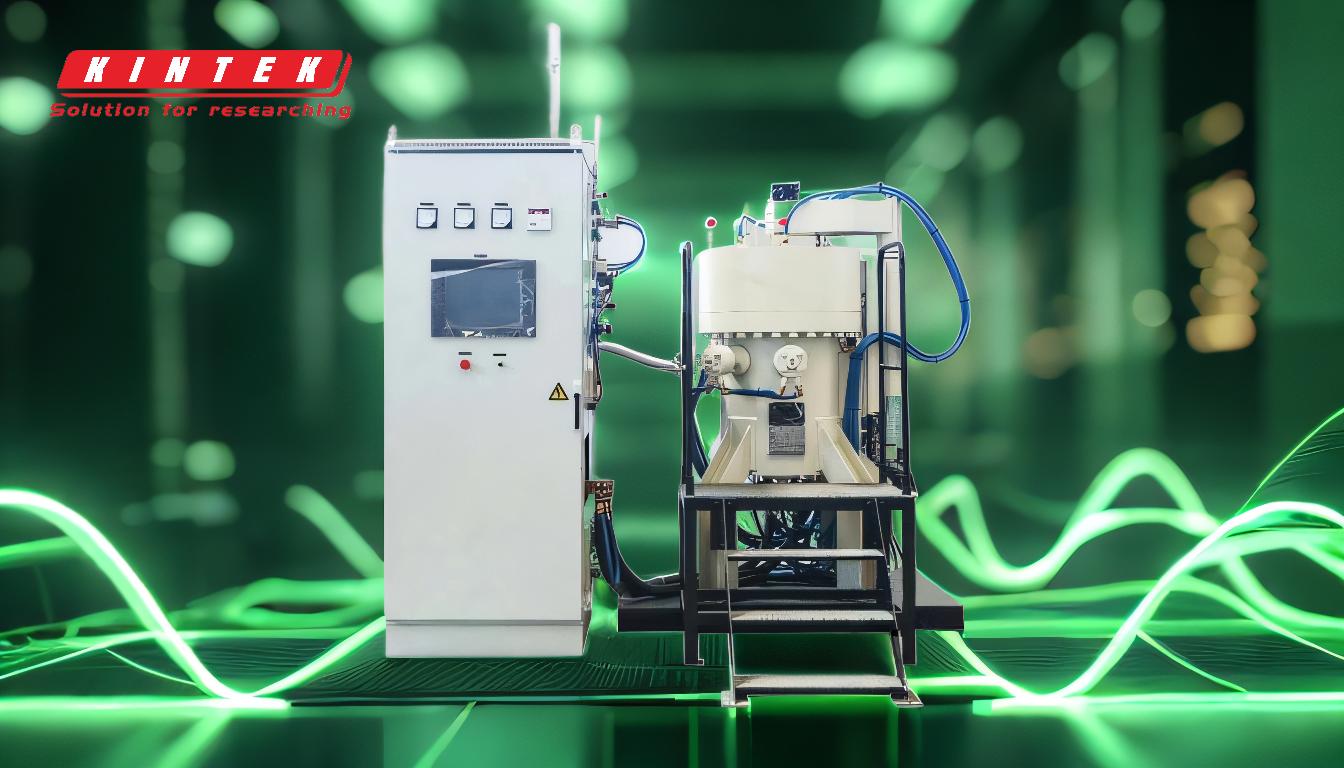
-
Definition of Sintering:
- Sintering is a process where powder particles are joined together through diffusion reactions. The primary driving force is the reduction in surface energy, which occurs as particles form necks and densify. This process is essential for creating solid materials from powdered precursors.
-
Stages of the Sintering Process:
- Stage 1: Shaping: A powder blend is mixed with a bonding agent (e.g., water, wax, or polymer) and formed into a desired shape. The bonding agent temporarily holds the particles together.
- Stage 2: Removal of Bonding Agent: The green part is heated, causing the bonding agent to evaporate or burn away. This step prepares the material for the final fusion stage.
- Stage 3: Fusion: The temperature is raised to a point where the primary particles begin to melt at their surfaces, fusing together. Alternatively, an intermediate bonding agent (e.g., bronze) may melt and bond the particles without altering the primary material.
-
Role of Sintering Furnaces:
- Sintering furnaces, such as vacuum sintering furnaces and hot press sintering furnaces, play a crucial role in the sintering process. These furnaces create controlled environments (e.g., vacuum or high-pressure conditions) to prevent oxidation and contamination, ensuring high-quality sintering. For example, a vacuum sintering furnace heats materials in a vacuum state, allowing chemical reactions and crystallization to occur without interference from air or impurities.
-
Applications of Sintering:
- Metallurgy: In steel manufacturing, sintering involves using powdered iron mixed with coke. The mixture is ignited, and air is drawn through it to initiate combustion, forming lumps suitable for blast furnace use.
- Ceramics: Sintering is used to produce ceramic materials with high density and strength. The process is often enhanced by vacuum or hot press sintering furnaces to achieve optimal results.
-
Importance of Environmental Control:
- Sintering requires precise control of temperature, pressure, and atmosphere. For example, a vacuum environment prevents oxidation, while water vapor can help cool the workpiece and form harmless by-products like CO or CO2. These controls are essential for achieving the desired material properties.
-
Interruptions and Quality Assurance:
- Interruptions, such as power failures, can disrupt the sintering process. Modern sintering equipment includes monitoring systems to ensure the process is completed correctly, guaranteeing the final product's density and stability.
-
Hot Press Sintering:
- A hot press sintering furnace combines high temperature and high pressure in a vacuum environment to fuse ceramic powders into solid materials. This method is particularly effective for producing high-density, high-strength components.
-
Benefits of Sintering:
- Sintering reduces porous spaces between particles, creating solid, durable materials. The process requires less heat and pressure than melting, making it energy-efficient and cost-effective for producing complex shapes and high-performance materials.
By understanding these key points, purchasers of sintering equipment and consumables can make informed decisions about the tools and materials needed for their specific applications.
Summary Table:
Key Aspect | Details |
---|---|
Definition | Fusing powder particles through diffusion to reduce surface energy. |
Stages | 1. Shaping with bonding agent 2. Removing bonding agent 3. Fusion |
Equipment | Vacuum or hot press sintering furnaces for controlled environments. |
Applications | Metallurgy, ceramics, and high-performance materials. |
Benefits | Energy-efficient, cost-effective, and produces durable, complex shapes. |
Discover how sintering can enhance your manufacturing process—contact our experts today!