Induction heating is a process that uses electromagnetic induction to generate heat in conductive materials. It involves passing an alternating current through a coil, creating a transient magnetic field. This magnetic field induces eddy currents in nearby conductive materials, which flow against the material's resistivity, generating heat through Joule heating. This non-contact method is efficient for heating metals and is widely used in industrial applications such as melting metals and creating alloys. The process relies on the principles of electromagnetic induction and Joule heating, making it a precise and controllable heating technique.
Key Points Explained:
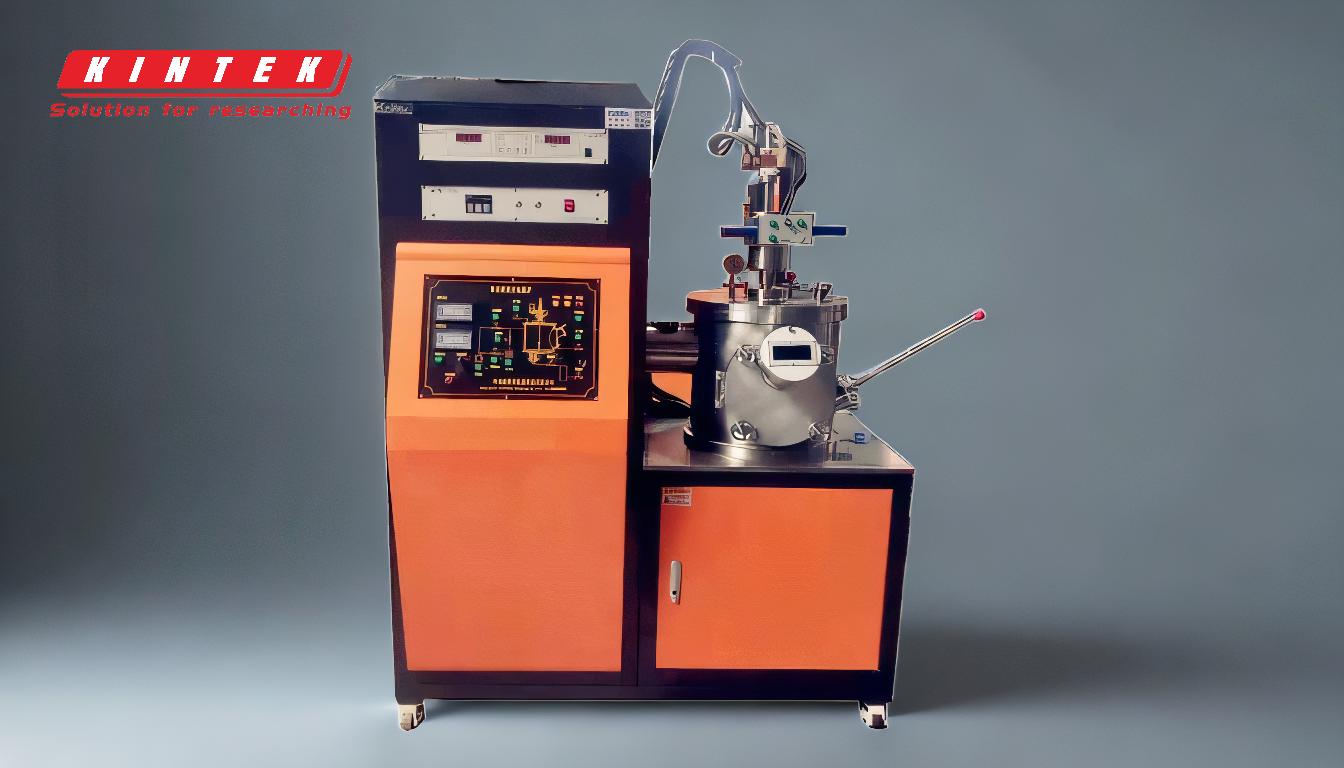
-
Electromagnetic Induction:
- Induction heating relies on the principle of electromagnetic induction, where an alternating current (AC) passes through a solenoid (coil).
- The alternating current generates a transient magnetic field around the coil, which changes direction and magnitude with the frequency of the AC.
- According to Maxwell’s equations, this changing magnetic field induces electric currents, known as eddy currents, in nearby conductive materials.
-
Eddy Currents:
- Eddy currents are loops of electrical current induced within the conductive material by the changing magnetic field.
- These currents flow in closed loops within the material, opposing the change in the magnetic field (Lenz's Law).
- The magnitude of the eddy currents depends on the material's conductivity, the strength of the magnetic field, and the frequency of the alternating current.
-
Joule Heating:
- As the eddy currents flow through the conductive material, they encounter resistance, which is a property of the material known as resistivity.
- The flow of eddy currents against the material's resistivity generates heat through Joule heating (also known as resistive heating).
- The heat generated is proportional to the square of the current (I²R), where I is the current and R is the resistance.
-
Non-Contact Heating:
- Induction heating is a non-contact process, meaning the heat is generated directly within the material without any physical contact between the heating source (coil) and the material.
- This makes induction heating highly efficient, as there is minimal heat loss to the surrounding environment.
- The non-contact nature also allows for precise control over the heating process, making it suitable for applications requiring localized heating.
-
Applications of Induction Heating:
- Melting Metals: Induction heating is commonly used in foundries to melt metals such as steel, iron, and aluminum. The process allows for precise temperature control and uniform heating.
- Creating Alloys: Induction heating is used in the production of alloys, where different metals are melted and mixed to create materials with specific properties.
- Heat Treatment: Induction heating is used for heat treatment processes such as hardening, annealing, and tempering, where precise control over temperature and heating time is required.
- Brazing and Soldering: Induction heating is used in brazing and soldering applications, where it provides localized heating to join metal parts without overheating the entire assembly.
-
Advantages of Induction Heating:
- Efficiency: Induction heating is highly efficient, as the heat is generated directly within the material, reducing energy loss.
- Precision: The process allows for precise control over the heating area and temperature, making it suitable for applications requiring localized heating.
- Speed: Induction heating can rapidly heat materials, reducing processing time compared to conventional heating methods.
- Safety: Since induction heating is a non-contact process, it reduces the risk of burns and other safety hazards associated with traditional heating methods.
-
Factors Affecting Induction Heating:
- Frequency of Alternating Current: The frequency of the AC affects the depth of penetration of the eddy currents into the material. Higher frequencies result in shallower penetration, suitable for surface heating, while lower frequencies penetrate deeper, suitable for bulk heating.
- Material Properties: The conductivity and magnetic permeability of the material affect the efficiency of induction heating. Materials with high conductivity and permeability heat more effectively.
- Coil Design: The design of the induction coil, including its shape, size, and number of turns, affects the distribution and intensity of the magnetic field, influencing the heating pattern.
In summary, induction heating is a versatile and efficient method for heating conductive materials, relying on the principles of electromagnetic induction and Joule heating. Its non-contact nature, precision, and speed make it a valuable technology in various industrial applications.
Summary Table:
Key Aspect | Details |
---|---|
Principle | Electromagnetic induction and Joule heating |
Process | Alternating current creates a magnetic field, inducing eddy currents |
Heat Generation | Eddy currents flow against material resistivity, generating heat |
Non-Contact Heating | Heat is generated within the material, no direct contact required |
Applications | Melting metals, creating alloys, heat treatment, brazing, and soldering |
Advantages | High efficiency, precision, speed, and safety |
Factors Affecting Heating | AC frequency, material properties, and coil design |
Discover how induction heating can revolutionize your industrial processes—contact us today for expert advice!