The calcining zone in a kiln is a critical section where raw materials undergo a high-temperature chemical process known as calcination. This zone typically operates at temperatures ranging from 800℃ to 1200℃, facilitating the dissociation of calcium carbonate (CaCO3) into calcium oxide (CaO) and carbon dioxide (CO2). Calcination is essential in industries like ceramics, cement production, and metallurgy, as it transforms raw materials into their desired chemical states. The calcining zone is part of a kiln's structure, which is designed to maintain high temperatures and control heat distribution, ensuring efficient and precise chemical transformations.
Key Points Explained:
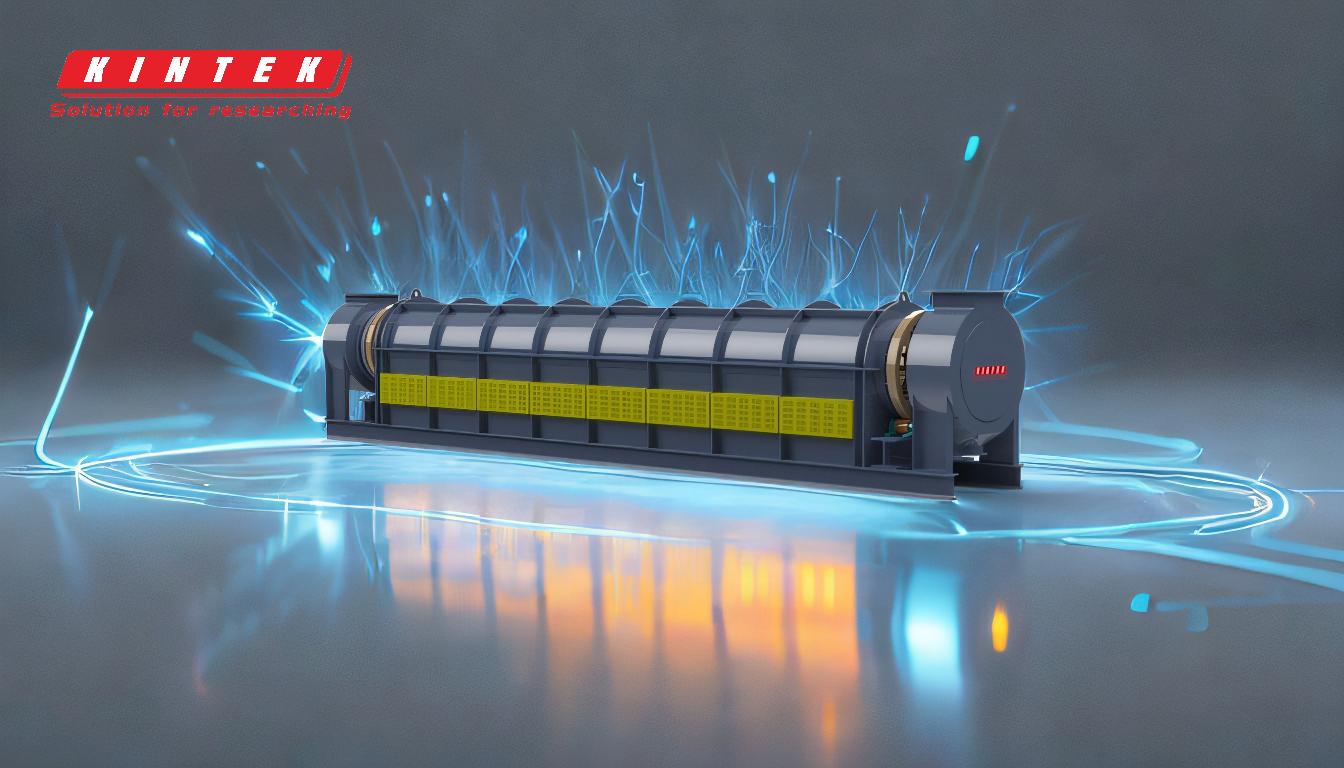
-
Definition of the Calcining Zone:
- The calcining zone is a specific section within a kiln where calcination occurs.
- Calcination is a thermal treatment process that involves heating materials to high temperatures to induce chemical dissociation or remove bound moisture.
-
Temperature Range:
- The calcining zone operates at temperatures between 800℃ and 1200℃.
- This temperature range is optimal for driving off carbon dioxide (CO2) from calcium carbonate (CaCO3), resulting in the formation of calcium oxide (CaO) or free lime.
-
Chemical Process in the Calcining Zone:
- The primary reaction in this zone is the dissociation of calcium carbonate:
[ \text{CaCO}_3 \rightarrow \text{CaO} + \text{CO}_2 ] - This reaction is endothermic, meaning it requires significant heat input to proceed.
- The primary reaction in this zone is the dissociation of calcium carbonate:
-
Role of Calcination:
- Calcination is used to create inorganic materials, such as calcium oxide, which is a key ingredient in cement and lime production.
- It can also remove bound moisture from materials, making it useful in processes like drying borax.
-
Kiln Structure and Function:
- Kilns are chambers made of refractory materials that can withstand high temperatures without melting.
- They provide precise control over heating and cooling cycles, ensuring consistent and efficient calcination.
-
Placement of the Calcining Zone in a Kiln:
- In a typical tunnel kiln, the calcining zone is part of a sequence of zones, including:
- Preheat Zone: Removes lubricants and organic materials.
- Sintering Zone: Facilitates diffusion and bonding of particles.
- Cooling Zone: Allows the sintered parts to cool gradually.
- In a typical tunnel kiln, the calcining zone is part of a sequence of zones, including:
-
Importance in Industrial Applications:
- The calcining zone is vital in industries such as cement production, ceramics, and metallurgy.
- It ensures the transformation of raw materials into usable products with the desired chemical and physical properties.
By understanding the calcining zone's role, temperature requirements, and chemical processes, industries can optimize their kiln operations for efficient and high-quality production.
Summary Table:
Aspect | Details |
---|---|
Definition | Section in a kiln where calcination occurs, a high-temperature chemical process. |
Temperature Range | 800℃ to 1200℃, optimal for dissociating calcium carbonate (CaCO3). |
Primary Reaction | CaCO3 → CaO + CO2 (endothermic reaction requiring significant heat input). |
Role of Calcination | Produces calcium oxide (CaO) for cement/lime and removes bound moisture. |
Kiln Structure | Made of refractory materials, designed for precise temperature control. |
Industrial Applications | Essential in cement production, ceramics, and metallurgy. |
Optimize your kiln operations with expert guidance—contact us today!