The driving force for sintering a ceramic is primarily the reduction in surface energy, which occurs as particles bond and densify during the process. This reduction in surface energy is driven by the replacement of high-energy vapor-solid interfaces with lower-energy solid-solid interfaces, leading to a more thermodynamically stable state. Factors such as temperature, pressure, particle size, and composition influence the sintering kinetics and final material properties. The process involves material migration, grain boundary movement, and densification, resulting in a hard, polycrystalline structure with reduced porosity and increased strength.
Key Points Explained:
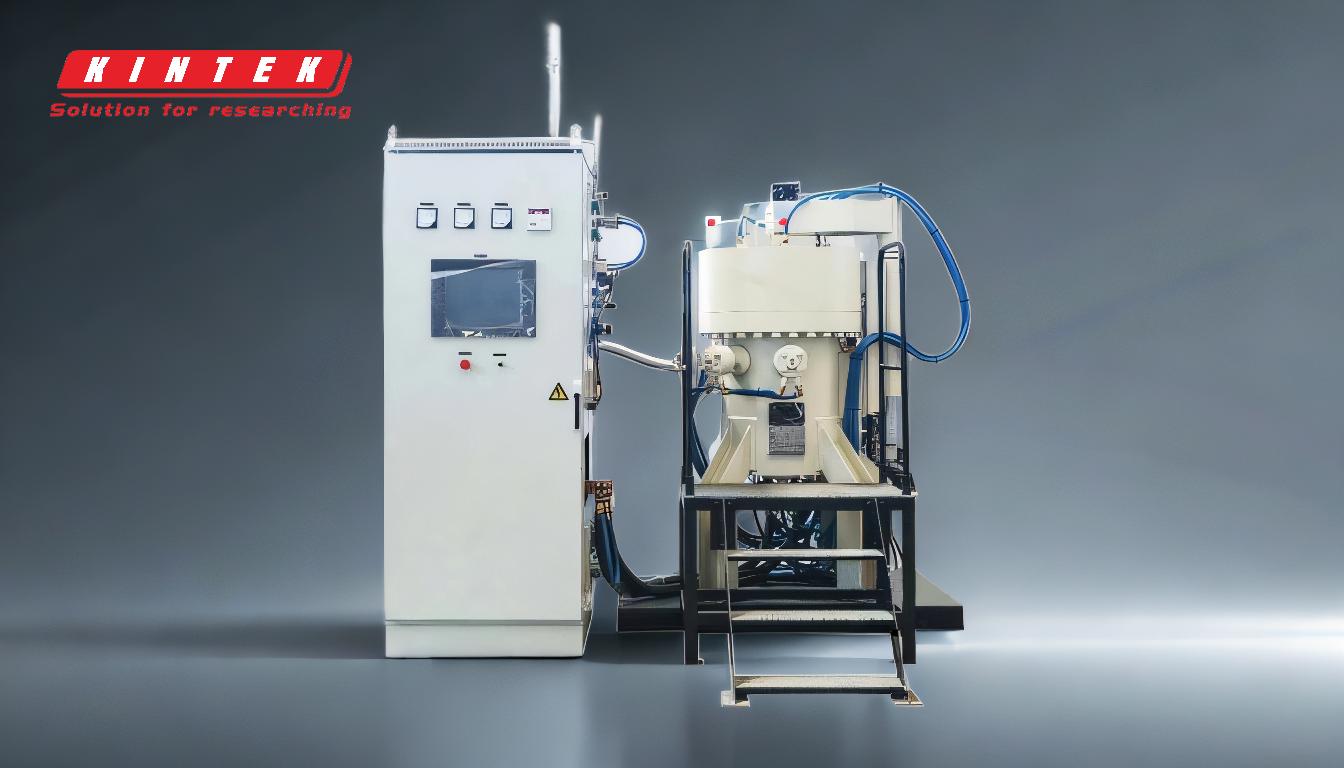
-
Reduction in Surface Energy:
- The primary driving force for sintering is the reduction in surface energy. This occurs as the high-energy vapor-solid interfaces between particles are replaced by lower-energy solid-solid interfaces.
- The formation of necks between particles and the subsequent densification of the material contribute to this reduction in surface energy.
-
Thermodynamic Stability:
- The sintering process aims to achieve a more thermodynamically stable state by minimizing the total free energy of the system.
- The decrease in surface area and surface free energy leads to a lower energy state, which is the driving force for densification.
-
Material Migration and Grain Boundary Movement:
- During sintering, material migration and grain boundary movement occur under high temperatures and a suitable atmosphere.
- These processes lead to the gradual densification of the ceramic material, forming a strong, polycrystalline structure.
-
Influence of Temperature and Heating Rate:
- Temperature plays a crucial role in determining the kinetics of sintering and the final material properties.
- The heating rate affects the densification process, with optimal rates promoting better densification and minimizing defects.
-
Role of Pressure:
- Applying pressure during sintering enhances particle rearrangement and helps eliminate porosity.
- Pressure can reduce the sintering time and improve the final density of the ceramic material.
-
Impact of Particle Size and Composition:
- Smaller particles have a higher surface area-to-volume ratio, which promotes faster sintering and better densification.
- Homogeneous compositions lead to more uniform sintering behavior, resulting in improved material properties.
-
Final Porosity and Density:
- The final porosity of sintered ceramics depends on the initial porosity of the green compact, as well as the temperature and duration of the sintering process.
- Pure oxide ceramics require longer sintering times and higher temperatures due to solid-state diffusion processes.
-
Formation of a Polycrystalline Sintered Body:
- As sintering progresses, solid particles bond, grains grow, and voids and grain boundaries decrease.
- This leads to volume shrinkage, increased density, and the formation of a hard, polycrystalline sintered body with a specific microstructure.
By understanding these key points, one can appreciate the complex interplay of factors that drive the sintering process and influence the final properties of ceramic materials.
Summary Table:
Key Factor | Impact on Sintering |
---|---|
Reduction in Surface Energy | Drives densification by replacing high-energy vapor-solid interfaces with solid-solid ones. |
Thermodynamic Stability | Minimizes free energy, leading to a more stable, lower-energy state. |
Temperature & Heating Rate | Affects sintering kinetics; optimal rates promote densification and reduce defects. |
Pressure | Enhances particle rearrangement, reduces porosity, and improves final density. |
Particle Size & Composition | Smaller particles and homogeneous compositions improve sintering uniformity and speed. |
Final Porosity & Density | Depends on initial porosity, temperature, and sintering duration. |
Want to optimize your ceramic sintering process? Contact our experts today for tailored solutions!