Heat treatment is a critical process in metallurgy and manufacturing that involves heating and cooling metals under controlled conditions to alter their physical and mechanical properties. The primary function of heat treatment is to enhance the usability, durability, and safety of metals for specific applications. It can make metals harder, stronger, and more resistant to impact, or softer and more ductile, depending on the desired outcome. Heat treatment is essential in industries such as aerospace, automotive, and manufacturing, where it improves grain structure, reduces stress, enhances strength, and increases fatigue life. This process ensures that metals meet the rigorous demands of their intended applications, making it indispensable for producing high-quality, reliable components.
Key Points Explained:
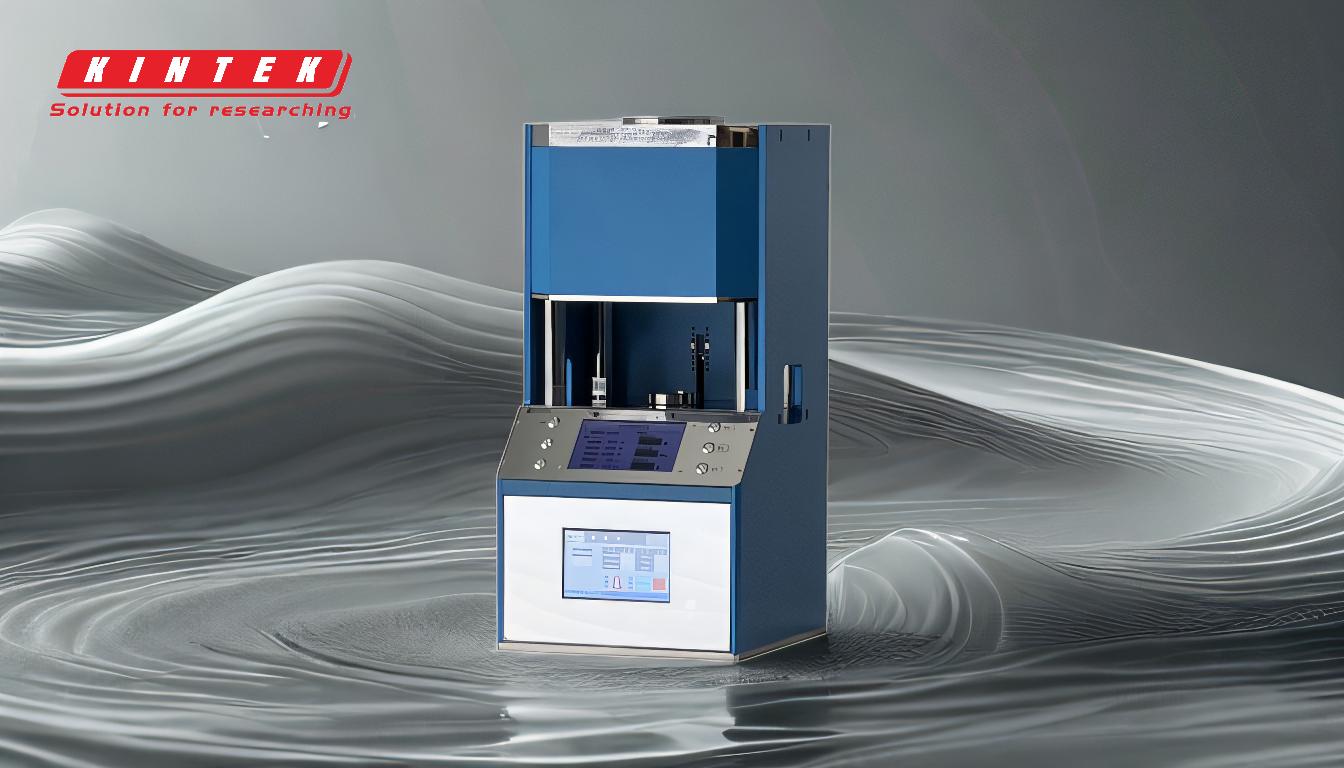
-
Altering Mechanical Properties:
- Heat treatment is primarily used to modify the mechanical properties of metals, such as hardness, strength, ductility, and toughness. By carefully controlling the heating and cooling processes, manufacturers can tailor these properties to meet specific requirements. For example, hardening a metal increases its resistance to wear and deformation, while annealing (softening) improves its formability and machinability.
-
Enhancing Performance and Durability:
- The process improves the overall performance and durability of metal components. For instance, in aerospace applications, heat treatment ensures that alloys can withstand extreme conditions by improving their grain structure, reducing internal stresses, and enhancing fatigue life. This makes the components more reliable and longer-lasting.
-
Improving Surface Properties:
- Heat treatment can create a hard surface on softer metals, increasing their resistance to abrasion and wear. Techniques like case hardening or surface hardening are used to achieve this, making the outer layer of the metal more durable while maintaining a softer, more ductile core.
-
Achieving Desired Chemical and Physical Reactions:
- The controlled heating and cooling processes induce specific chemical and physical reactions within the metal. These reactions can alter the microstructure of the material, leading to improvements in properties such as corrosion resistance, electrical conductivity, and thermal stability.
-
Versatility Across Metals:
- Heat treatment is applicable to both ferrous (iron-based) and non-ferrous metals (e.g., aluminum, copper, titanium). This versatility allows manufacturers to enhance the properties of a wide range of materials, making them suitable for diverse industrial applications.
-
Critical for Manufacturing Processes:
- In manufacturing, heat treatment is often a preparatory step that ensures metals are in the optimal condition for subsequent processes like machining, welding, or forming. For example, in gear manufacturing, heat treatment is essential for producing gears that are strong, durable, and capable of withstanding high stresses.
-
Ensuring Safety and Reliability:
- By improving the mechanical and physical properties of metals, heat treatment ensures that components are safe and reliable for their intended use. This is particularly important in industries like aerospace and automotive, where failure of a single component can have catastrophic consequences.
-
Customization for Specific Applications:
- Heat treatment processes can be customized to achieve specific outcomes based on the application. For instance, quenching and tempering are used to balance hardness and toughness, while processes like normalizing refine the grain structure to improve uniformity and strength.
In summary, heat treatment is a versatile and essential process that enhances the properties of metals, making them more suitable for a wide range of industrial applications. By altering mechanical properties, improving performance, and ensuring safety, heat treatment plays a crucial role in the manufacturing and engineering sectors.
Summary Table:
Key Benefits of Heat Treatment | Description |
---|---|
Alters Mechanical Properties | Modifies hardness, strength, ductility, and toughness for specific needs. |
Enhances Performance & Durability | Improves grain structure, reduces stress, and increases fatigue life. |
Improves Surface Properties | Creates hard surfaces on softer metals for abrasion resistance. |
Achieves Chemical & Physical Reactions | Alters microstructure for better corrosion resistance and thermal stability. |
Versatile Across Metals | Applicable to both ferrous and non-ferrous metals. |
Critical for Manufacturing | Prepares metals for machining, welding, or forming. |
Ensures Safety & Reliability | Makes components safe and reliable for high-stress applications. |
Customizable for Specific Needs | Tailored processes like quenching, tempering, and normalizing. |
Optimize your metal components with expert heat treatment solutions—contact us today!