The length of time heat is applied during the annealing heat treatment process depends on the material being treated, the desired outcome, and the specific stage of annealing (recovery, recrystallization, or grain growth). Generally, the process involves heating the material to a specific temperature, holding it at that temperature for a predetermined time, and then cooling it slowly. The holding time can range from a few minutes to several hours, depending on factors like material type, thickness, and the annealing furnace's capabilities. For instance, rapid annealing furnaces offer precise temperature and time control, making them suitable for applications requiring strict accuracy, while traditional furnaces may require longer holding times for similar results.
Key Points Explained:
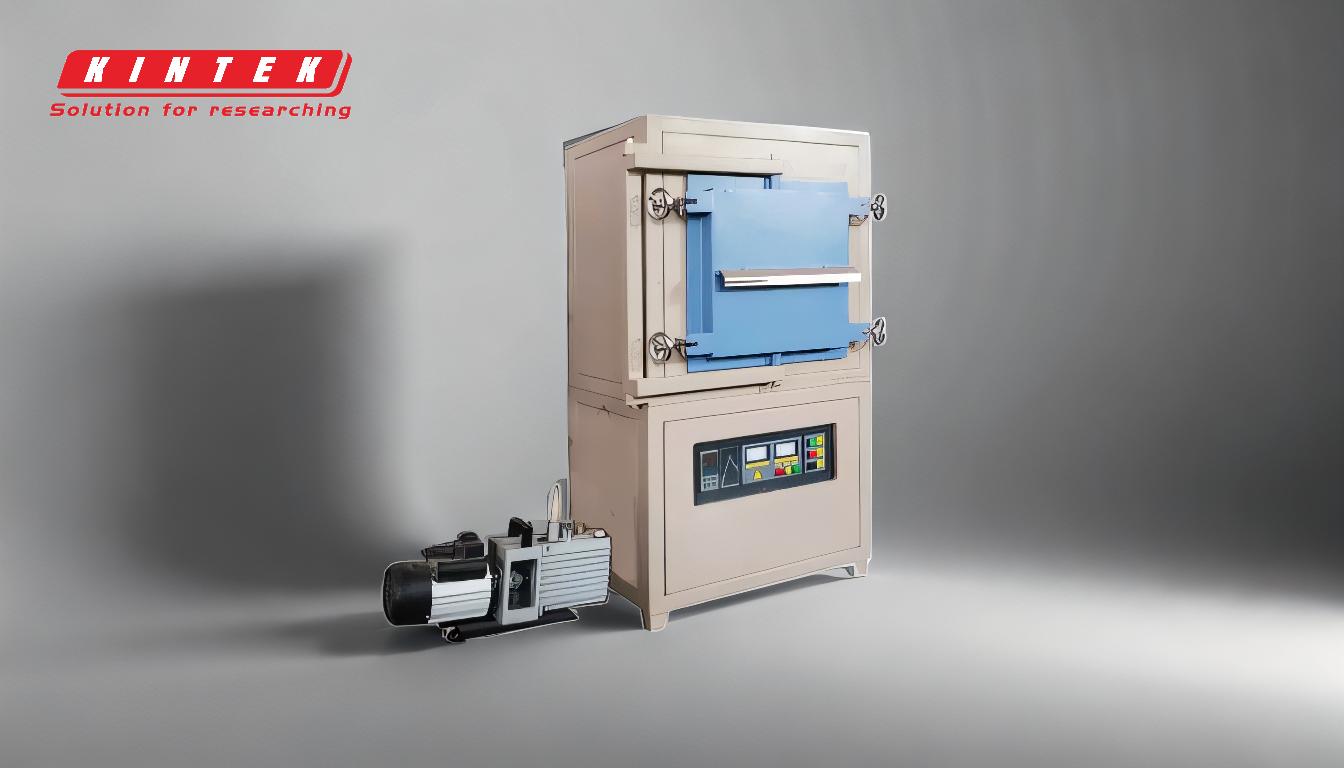
-
Purpose of Annealing Heat Treatment:
- Annealing is a heat treatment process used to alter the physical and sometimes chemical properties of a material to increase its ductility, reduce hardness, and improve machinability. The process involves heating the material to a specific temperature, holding it there for a set time, and then cooling it slowly.
-
Stages of Annealing:
- The annealing process typically consists of three stages:
- Recovery: The material is heated to relieve internal stresses without changing the grain structure. This stage occurs at lower temperatures and involves the removal of dislocations and internal stresses.
- Recrystallization: The material is heated above its recrystallization temperature but below its melting point. New strain-free grains nucleate and grow, replacing the deformed grains. This stage is crucial for restoring the material's ductility.
- Grain Growth: After recrystallization, if the material is held at the annealing temperature, the new grains continue to grow, making the material more pliable and easier to work with.
- The annealing process typically consists of three stages:
-
Factors Influencing Holding Time:
- The length of time heat is applied during annealing depends on several factors:
- Material Type: Different materials have different recrystallization temperatures and require varying holding times. For example, steel may require longer holding times compared to aluminum.
- Material Thickness: Thicker materials generally require longer holding times to ensure uniform heating throughout the material.
- Desired Outcome: The specific properties desired in the final product (e.g., ductility, hardness) can influence the holding time.
- Furnace Type: The type of annealing furnace used can also affect the holding time. Rapid annealing furnaces, with their high heating efficiency and precise temperature control, can reduce the required holding time compared to traditional tube furnaces.
- The length of time heat is applied during annealing depends on several factors:
-
Typical Holding Times:
- For many metals, the holding time during the recrystallization stage can range from a few minutes to several hours. For example:
- Steel: Holding times can range from 1 to 4 hours, depending on the alloy and thickness.
- Aluminum: Holding times are typically shorter, often around 30 minutes to 2 hours.
- Copper: Holding times can vary widely, from a few minutes to several hours, depending on the specific alloy and desired properties.
- For many metals, the holding time during the recrystallization stage can range from a few minutes to several hours. For example:
-
Importance of Atmosphere in Annealing:
- The furnace atmosphere plays a crucial role in the annealing process. It can either protect the material from oxidation (inert atmosphere) or allow surface changes, such as carburization or nitriding (active atmosphere). The choice of atmosphere can influence the holding time and the overall quality of the annealed material.
-
Cooling Process:
- After the holding time, the material is cooled slowly to prevent the reintroduction of internal stresses. The cooling rate is an essential part of the annealing process and can affect the final properties of the material.
In summary, the length of time heat is applied during the annealing process varies based on the material, desired outcome, and specific annealing stage. Understanding these factors is crucial for achieving the desired material properties and ensuring a successful heat treatment process.
Summary Table:
Factor | Details |
---|---|
Material Type | Steel: 1-4 hours, Aluminum: 30 mins-2 hours, Copper: Varies widely |
Material Thickness | Thicker materials require longer holding times for uniform heating |
Desired Outcome | Influences holding time (e.g., ductility, hardness) |
Furnace Type | Rapid furnaces reduce holding time; traditional furnaces require longer |
Annealing Stages | Recovery, Recrystallization, Grain Growth |
Cooling Process | Slow cooling prevents reintroduction of internal stresses |
Need help optimizing your annealing process? Contact our experts today for tailored solutions!