Furnace linings are critical components that ensure the efficient operation and longevity of furnaces by providing thermal insulation, resistance to high temperatures, and protection against chemical corrosion. The choice of lining material depends on the specific requirements of the furnace, such as the operating temperature, thermal shock resistance, and chemical resistance. Common materials used for furnace linings include silica, magnesia, alumina fiber, silicon carbide (SiC), and lightweight refractory bricks. These materials are selected based on their properties, such as high service temperature, low heat storage, rapid heat and cold resistance, and excellent thermal insulation. The design of the furnace lining often involves a multi-layer insulation approach to minimize heat loss and energy consumption.
Key Points Explained:
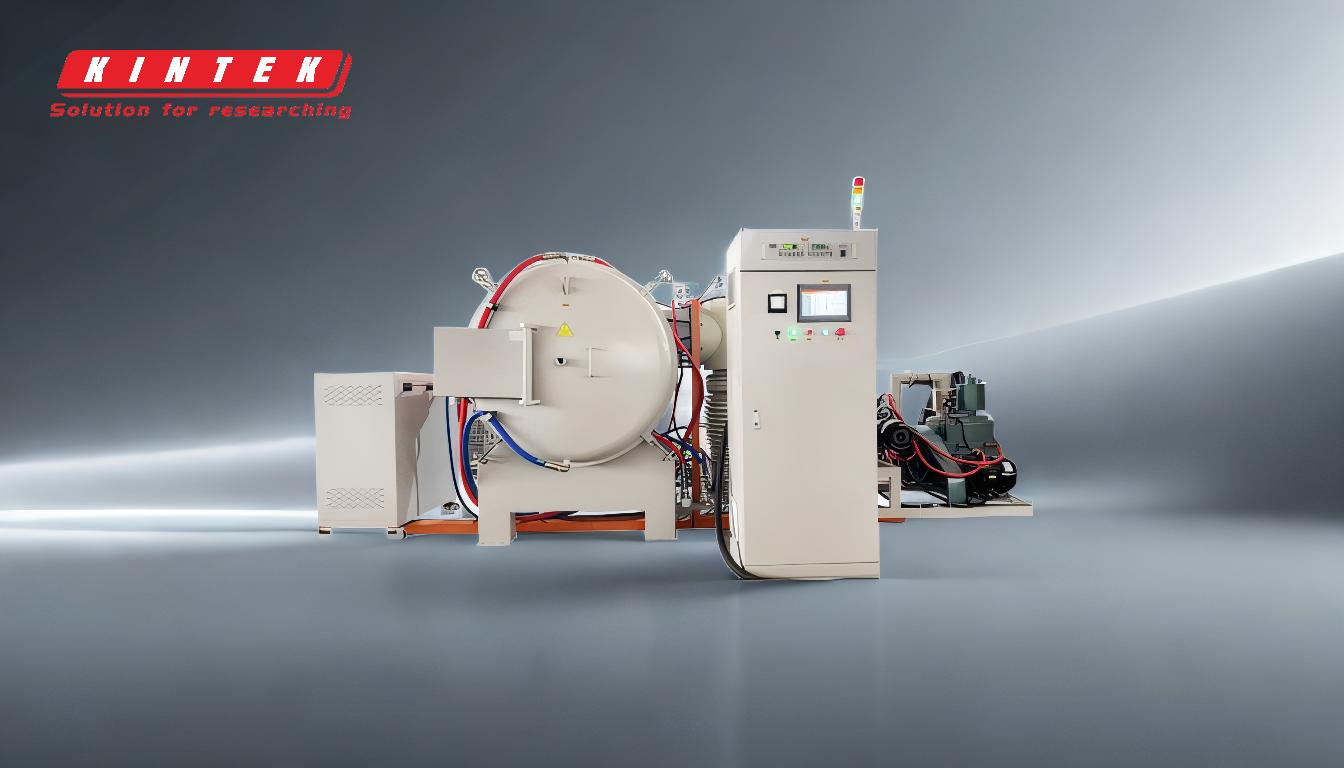
-
Types of Furnace Lining Materials:
- Silica: Made from silicon dioxide, silica is used in furnaces requiring high resistance to thermal shock. It is ideal for applications where rapid temperature changes occur.
- Magnesia: Composed of magnesium oxide, magnesia is chosen for furnaces that need high resistance to chemical corrosion. It is commonly used in environments with aggressive chemical reactions.
- Alumina Fiber: High-purity alumina fiber is a lightweight material that offers high service temperatures, small heat storage capacity, and excellent thermal insulation. It is often used in vacuum-formed applications.
- Silicon Carbide (SiC): SiC is known for its high strength and thermal conductivity. It is used in advanced furnace linings to ensure accurate and uniform process conditions.
- Lightweight Refractory Bricks: These bricks are used in combination with other materials to provide structural integrity and thermal insulation.
-
Properties of Furnace Lining Materials:
- High Service Temperature: Materials like alumina fiber and SiC can withstand extremely high temperatures, making them suitable for industrial furnaces.
- Thermal Shock Resistance: Silica and alumina fiber are designed to handle rapid temperature changes without cracking or degrading.
- Chemical Resistance: Magnesia and SiC are resistant to chemical corrosion, making them ideal for furnaces exposed to reactive substances.
- Thermal Insulation: Materials such as alumina fiber and lightweight refractory bricks provide excellent insulation, reducing heat loss and energy consumption.
-
Multi-Layer Insulation Design:
- Modern furnace linings often use a multi-layer insulation design, combining materials like lightweight alumina ceramic fiber and high-quality insulation boards. This design minimizes heat loss and ensures low energy consumption.
- The absence of asbestos in these designs makes them safer and more environmentally friendly.
-
Construction and Structural Features:
- The furnace shell is typically made from corrosion-resistant materials like Q235 low-carbon steel or 304 stainless steel. These materials provide durability and resistance to environmental factors.
- Features such as double-layer metal frames, heat-insulating fan structures, and mirror-polished surfaces help maintain low surface temperatures and improve efficiency.
- The furnace body may include various openings (e.g., electrode holes, thermocouple holes) made of stainless steel for functionality and durability.
-
Applications and Benefits:
- High-Temperature Furnaces: Materials like alumina fiber and SiC are used in high-temperature applications, such as muffle furnaces, to ensure uniform heating and process accuracy.
- Energy Efficiency: The use of lightweight and insulating materials reduces heat loss, leading to lower energy consumption and operational costs.
- Durability: The combination of materials like silica, magnesia, and SiC ensures long-lasting performance, even in harsh operating conditions.
In summary, the choice of furnace lining material depends on the specific requirements of the furnace, including temperature, chemical environment, and thermal shock resistance. Materials like silica, magnesia, alumina fiber, and SiC are commonly used due to their unique properties and benefits. The design of the furnace lining, including multi-layer insulation and corrosion-resistant construction, plays a crucial role in ensuring efficient and durable furnace operation.
Summary Table:
Material | Key Properties | Applications |
---|---|---|
Silica | High thermal shock resistance | Rapid temperature change environments |
Magnesia | High chemical resistance | Aggressive chemical environments |
Alumina Fiber | High service temperature, lightweight, excellent insulation | Vacuum-formed applications, high-temperature furnaces |
Silicon Carbide | High strength, thermal conductivity | Advanced linings for accurate and uniform process conditions |
Refractory Bricks | Structural integrity, thermal insulation | Combined with other materials for insulation and support |
Need help selecting the right furnace lining for your application? Contact our experts today!