The lining of a furnace is designed to withstand extreme temperatures and provide insulation, ensuring efficient and safe operation. It is typically made of refractory materials that resist heat, maintain structural integrity, and offer thermal insulation. Common materials include high-purity alumina fiber, magnesium oxide (MgO), ceramic tiles, zirconia boards, high alumina bricks, and lightweight refractory bricks. These materials are chosen based on the furnace's operating temperature and specific requirements. For instance, ceramic tiles are used for temperatures up to 1200°C, while zirconia boards and high alumina bricks are suitable for higher temperatures up to 1600°C and 1800°C, respectively. The lining's composition ensures durability, rapid heat resistance, and minimal heat loss.
Key Points Explained:
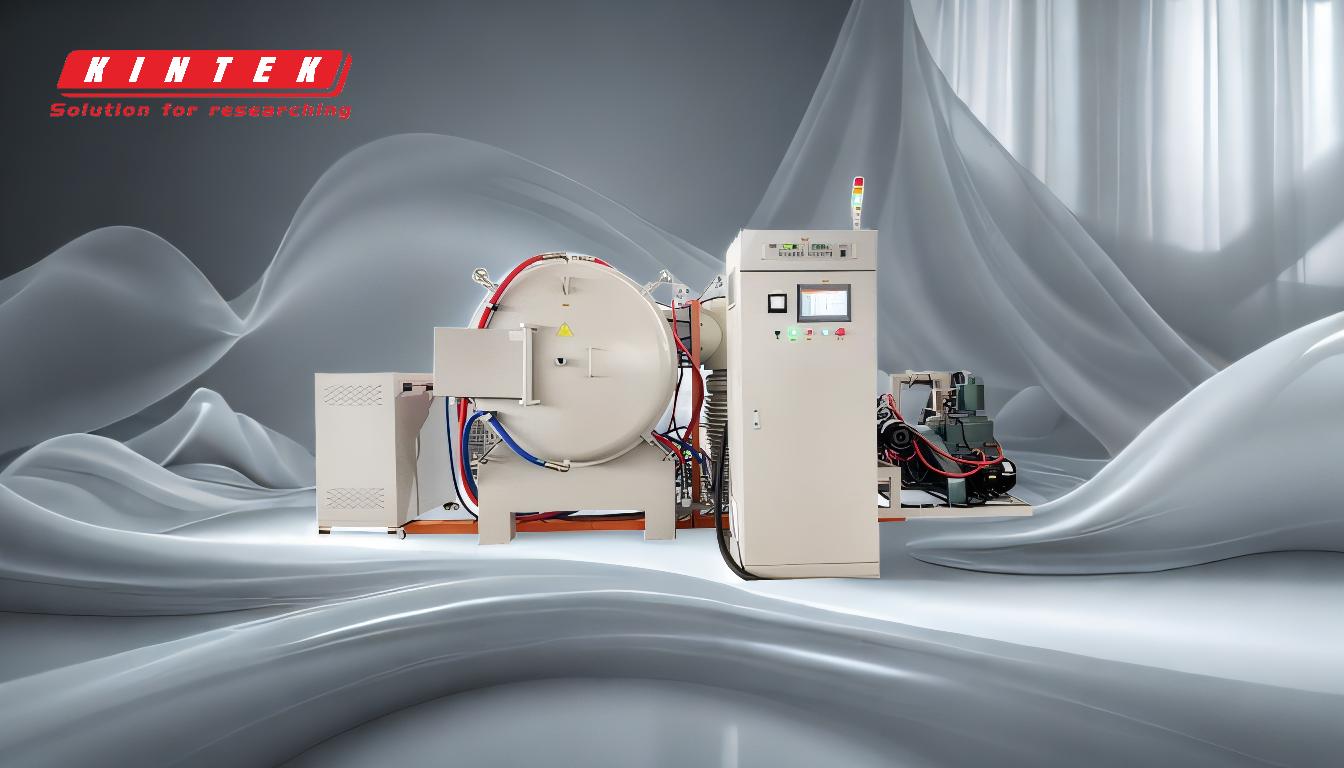
-
Purpose of Furnace Lining:
- The furnace lining is crucial for maintaining the furnace's structural integrity and thermal efficiency. It protects the outer shell from extreme heat and prevents heat loss.
- It acts as a barrier between the high-temperature environment inside the furnace and the external structure, ensuring safety and longevity.
-
Common Materials Used in Furnace Linings:
- High-Purity Alumina Fiber: Known for its high service temperature, small heat storage capacity, and excellent thermal insulation properties. It is vacuum-formed and lightweight, making it ideal for high-temperature applications.
- Magnesium Oxide (MgO): A refractory material that resists heat and maintains strength at extremely high temperatures. It is often used in furnaces requiring robust thermal resistance.
- Ceramic Tiles: Suitable for temperatures up to 1200°C, ceramic tiles are durable and provide good thermal insulation.
- Zirconia Boards: Used in furnaces operating at temperatures up to 1600°C, zirconia boards offer high thermal resistance and stability.
- High Alumina Bricks: Ideal for furnaces operating at temperatures up to 1800°C, these bricks are highly durable and resistant to thermal shock.
-
Material Selection Based on Operating Temperature:
- The choice of lining material depends on the furnace's maximum operating temperature. For example:
- Ceramic tiles are used for lower-temperature furnaces (up to 1200°C).
- Zirconia boards are selected for medium-temperature furnaces (up to 1600°C).
- High alumina bricks are used for high-temperature furnaces (up to 1800°C).
- The choice of lining material depends on the furnace's maximum operating temperature. For example:
-
Additional Features of Furnace Linings:
- Thermal Insulation: Materials like high-purity alumina fiber and lightweight refractory bricks provide excellent heat preservation, reducing energy consumption.
- Durability: Refractory materials are designed to withstand thermal cycling, preventing cracks and slag falling.
- Rapid Heat and Cold Resistance: Some materials, such as vacuum-formed alumina fiber, can quickly adapt to temperature changes without degrading.
-
Construction and Design Considerations:
- The furnace lining is often integrated with the furnace's structural components, such as inner and outer tubes, flanges, and electrode holes, all made of stainless steel or low-carbon steel.
- The lining is designed to accommodate various furnace features, including observation holes, thermocouple holes, and heating rods, ensuring functionality and ease of maintenance.
-
Examples of Furnace Types and Their Linings:
- Muffle Furnace: Typically lined with ceramic tiles, zirconia boards, or high alumina bricks, depending on the operating temperature.
- Sintering Furnace: Constructed using high-purity alumina fiber insulation and Morgan materials brick for durability and efficiency.
- High-Temperature Furnace: Often lined with refractory metals or dense, heat-resistant materials like alumina fiber and lightweight bricks.
In summary, the furnace lining is a critical component that ensures the furnace operates efficiently and safely at high temperatures. The choice of materials depends on the furnace's specific requirements, including operating temperature, thermal insulation needs, and durability. Common materials include high-purity alumina fiber, magnesium oxide, ceramic tiles, zirconia boards, and high alumina bricks, each offering unique properties to meet the demands of different furnace types.
Summary Table:
Material | Max Temperature | Key Properties |
---|---|---|
High-Purity Alumina Fiber | Up to 1800°C | Lightweight, excellent thermal insulation, rapid heat resistance |
Magnesium Oxide (MgO) | Up to 2800°C | Robust thermal resistance, maintains strength at extreme temperatures |
Ceramic Tiles | Up to 1200°C | Durable, good thermal insulation, ideal for lower-temperature furnaces |
Zirconia Boards | Up to 1600°C | High thermal resistance, stability, suitable for medium-temperature applications |
High Alumina Bricks | Up to 1800°C | Highly durable, resistant to thermal shock, ideal for high-temperature furnaces |
Need help selecting the right furnace lining for your application? Contact our experts today for personalized guidance!