Hot press forming, particularly in powder metallurgy, is a process that integrates compaction and sintering into a single operation. This method involves creating a "green part" from metal particles and then applying both high pressure and elevated temperatures to sinter the particles together without melting them. The primary function of hot press forming is to produce dense, strong, and precise components by combining these two critical stages in one chamber.
Key Points Explained:
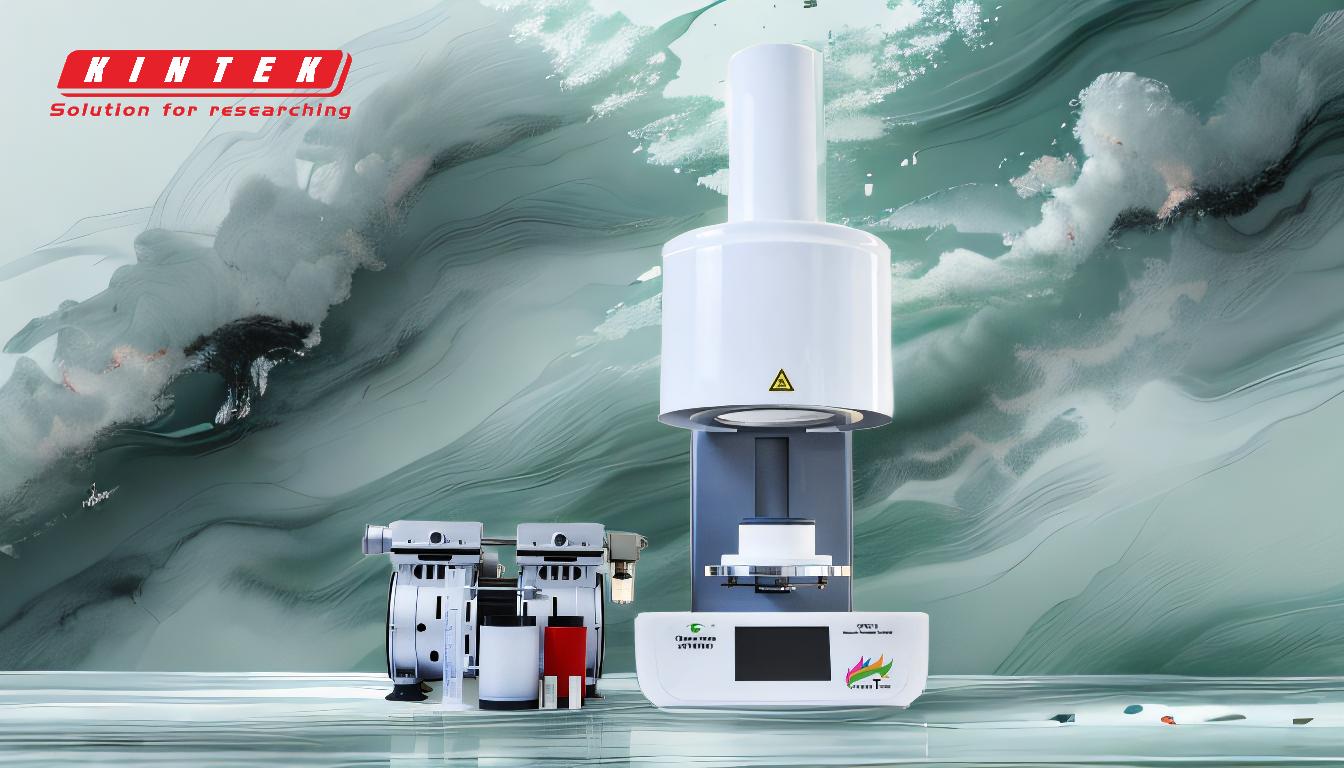
-
Integration of Compaction and Sintering:
- Compaction: The process begins with the compaction of metal powders into a desired shape, known as the green part. This is achieved using a die that applies high pressure to the powder, forming a coherent but still porous structure.
- Sintering: Immediately after compaction, the green part is subjected to elevated temperatures just below the melting point of the alloy. This allows the particles to bond at their contact points, a process known as "necking," which increases the strength and density of the final product.
-
Role of High Pressure and Temperature:
- High Pressure: The application of high pressure during the compaction stage ensures that the metal particles are densely packed, reducing porosity and increasing the overall strength of the component.
- Elevated Temperature: The heat applied during sintering facilitates the diffusion of atoms between particles, leading to the formation of strong metallurgical bonds. This thermal energy is crucial for achieving the desired material properties without reaching the melting point.
-
Advantages of Hot Press Forming:
- Enhanced Density and Strength: By combining compaction and sintering, hot press forming produces components with higher density and superior mechanical properties compared to traditional methods.
- Precision and Complexity: The process allows for the production of complex shapes with high precision, making it suitable for applications requiring tight tolerances.
- Efficiency: Integrating the two stages into a single operation reduces processing time and energy consumption, making it a more efficient manufacturing method.
-
Applications of Hot Press Forming:
- Powder Metallurgy: Widely used in the production of metal parts for various industries, including automotive, aerospace, and electronics.
- Ceramics and Composites: The process is also applicable to the manufacturing of ceramic and composite materials, where high density and strength are required.
-
Hot Press Machine:
- The hot press machine is the essential equipment used in this process. It is designed to apply both the necessary pressure and temperature in a controlled environment, ensuring the successful formation of high-quality components.
In summary, hot press forming is a highly effective manufacturing process that combines compaction and sintering to produce dense, strong, and precise components. The integration of high pressure and elevated temperature in a single chamber, facilitated by the hot press machine, makes this method efficient and suitable for a wide range of industrial applications.
Summary Table:
Aspect | Details |
---|---|
Process | Combines compaction and sintering in a single operation. |
Key Stages | Compaction: High pressure forms green parts. Sintering: Heat bonds particles. |
Benefits | Enhanced density, strength, precision, and efficiency. |
Applications | Powder metallurgy, ceramics, composites, automotive, aerospace, electronics. |
Equipment | Hot press machine applies controlled pressure and temperature. |
Learn how hot press forming can elevate your manufacturing process—contact our experts today!