Sintering is a critical process used to increase the density and strength of materials by heating them below their melting point. It involves compacting powdered materials into a desired shape and then heating them in a sintering furnace to facilitate particle bonding and densification. The process typically includes stages such as powder preparation, compaction, heating, and cooling. Sintering is widely used in industries like ceramics, metallurgy, and 3D printing to produce high-density, durable materials with specific mechanical properties. The method varies depending on the material and application, but the core principles remain consistent.
Key Points Explained:
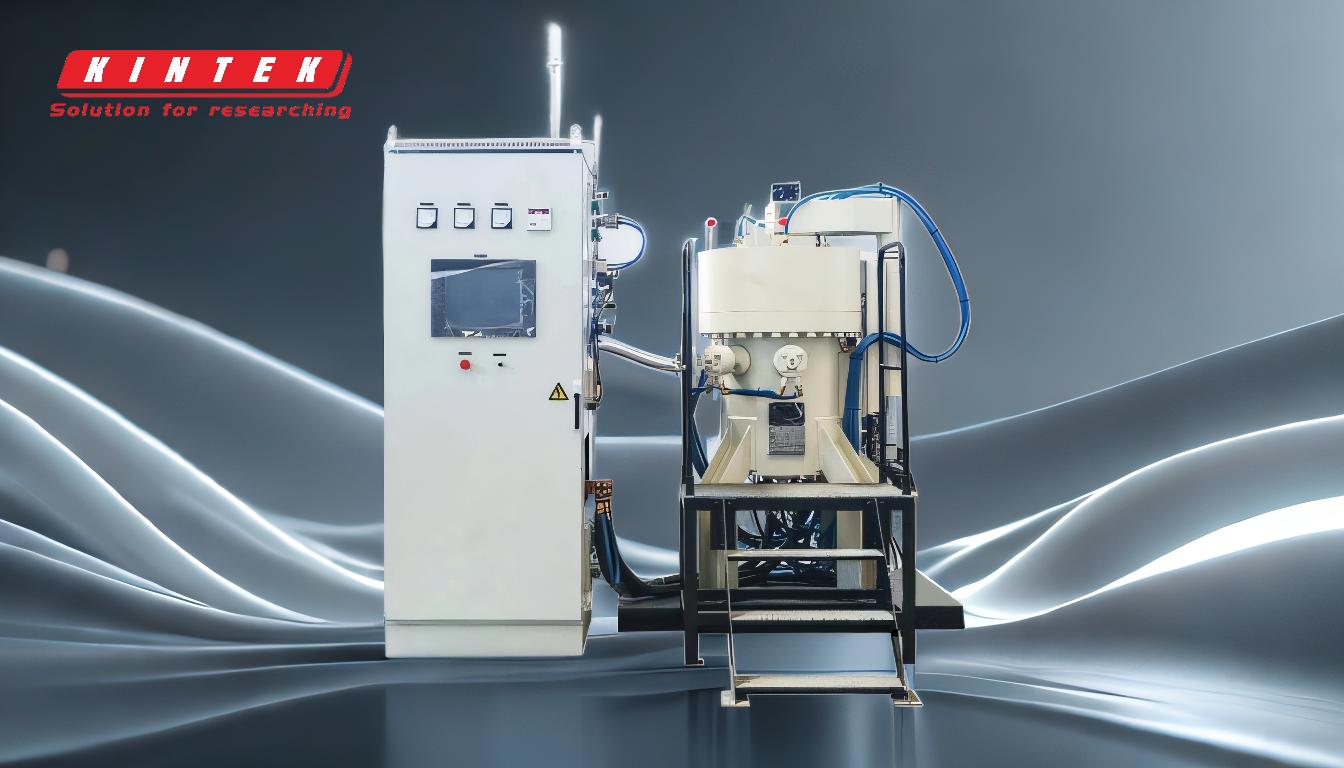
-
Definition and Purpose of Sintering:
- Sintering is a thermal process that increases the density of materials by heating them below their melting point.
- It is used to bond particles together, reduce porosity, and improve mechanical properties such as strength and durability.
-
Stages of the Sintering Process:
- Powder Preparation: Raw materials are ground into fine powders and often mixed with additives like binders or lubricants.
- Compaction: The powder is pressed into a specific shape using high pressure to eliminate voids and ensure uniformity.
- Heating: The compacted material is heated in a sintering furnace at controlled temperatures to facilitate particle bonding and densification.
- Cooling: The sintered product is cooled to solidify it into a rigid and cohesive structure.
-
Types of Sintering:
- Pressureless Sintering: Uses only heat to bond particles, commonly used for ceramics and metals.
- Hot Press Sintering: Combines heat and pressure in a vacuum environment, ideal for producing high-density materials like ceramics.
- Liquid Phase Sintering: Involves adding a liquid phase to aid particle bonding, often used in metal and ceramic composites.
-
Applications of Sintering:
- Ceramics: Used to produce high-density ceramic components for industries like electronics and aerospace.
- Metals: Common in powder metallurgy for manufacturing gears, bearings, and other mechanical parts.
- 3D Printing: Sintering is essential for debinding and densifying 3D-printed metal and ceramic parts.
-
Key Equipment: Sintering Furnace:
- A sintering furnace is the core equipment used in the process, providing controlled heating environments.
- It consists of a furnace body, heating elements, pressure systems (for hot press sintering), and vacuum systems (for oxygen-sensitive materials).
-
Factors Influencing Sintering:
- Temperature: Must be carefully controlled to avoid melting while ensuring sufficient particle bonding.
- Time: Longer sintering times generally lead to higher density and better mechanical properties.
- Atmosphere: Inert or reducing atmospheres are often used to prevent oxidation.
-
Advantages of Sintering:
- Produces materials with high density and strength.
- Enables the creation of complex shapes and fine details.
- Cost-effective for mass production of components.
-
Challenges and Considerations:
- Shrinkage of the material during sintering must be accounted for in the design phase.
- Proper selection of sintering parameters (temperature, time, pressure) is crucial to achieve desired properties.
By understanding the sintering process and its stages, manufacturers can optimize the production of high-performance materials for various applications.
Summary Table:
Aspect | Details |
---|---|
Definition | Thermal process to increase material density by heating below melting point. |
Stages | Powder preparation, compaction, heating, cooling. |
Types | Pressureless, hot press, liquid phase sintering. |
Applications | Ceramics, metals, 3D printing. |
Key Equipment | Sintering furnace with controlled heating environments. |
Advantages | High density, strength, cost-effective for mass production. |
Challenges | Shrinkage, precise parameter control required. |
Ready to optimize your material production with sintering? Contact our experts today for tailored solutions!