The safety factor of a vacuum chamber is a critical consideration in its design and operation, particularly in applications like vacuum hot pressing. It ensures that the chamber can withstand operational stresses without failure. The safety factor is influenced by material properties, design specifications, and operational conditions. This answer explores the concept of safety factor, its importance, and how it applies to vacuum chambers, especially in the context of vacuum hot press systems.
Key Points Explained:
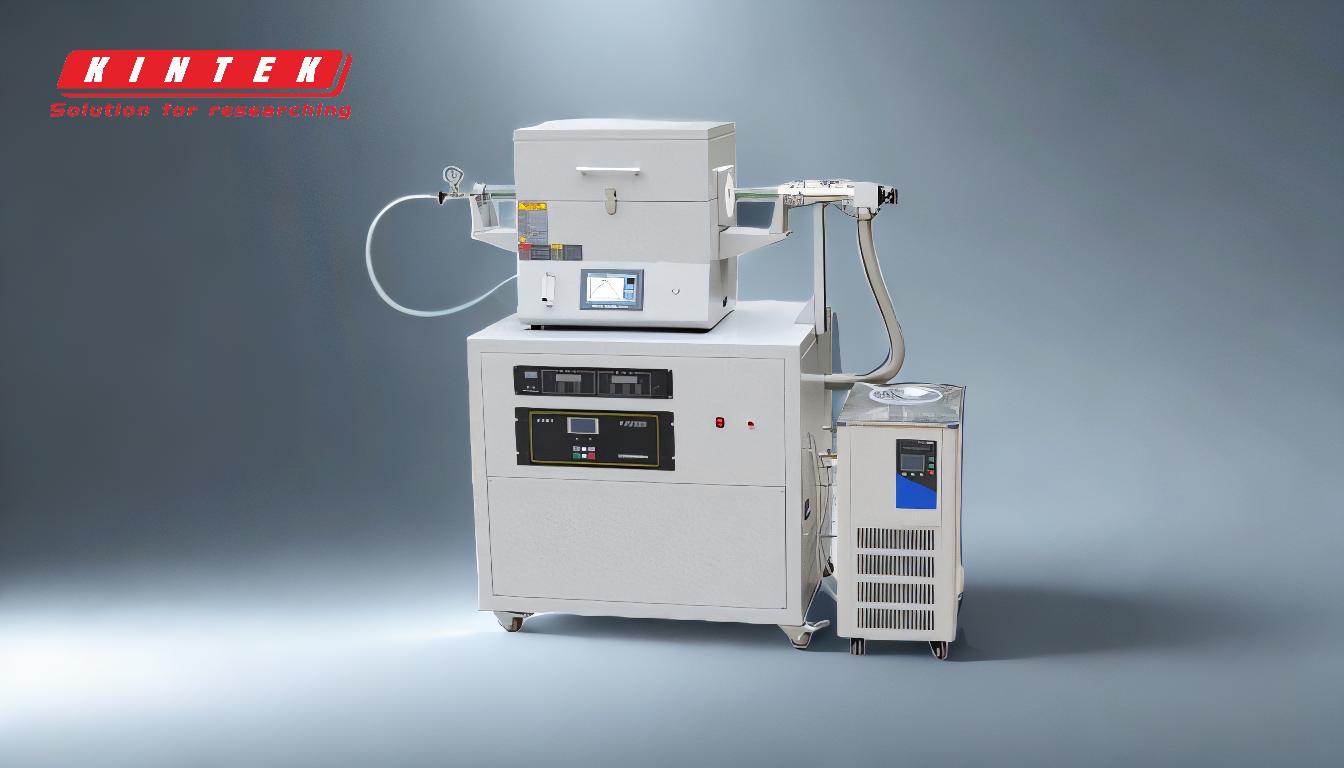
-
Definition of Safety Factor:
- The safety factor is a ratio of the maximum stress a material or structure can withstand to the expected operational stress. It provides a margin of safety to account for uncertainties in material properties, manufacturing processes, and operational conditions.
- For vacuum chambers, the safety factor ensures the chamber can handle internal and external pressures, thermal stresses, and mechanical loads without deformation or failure.
-
Importance in Vacuum Chambers:
- Vacuum chambers operate under extreme conditions, such as high pressure differentials, thermal cycling, and corrosive environments. A high safety factor is essential to prevent catastrophic failures, which could lead to equipment damage, loss of materials, or even safety hazards.
- In applications like vacuum hot press, where high temperatures and pressures are applied, the safety factor ensures the chamber maintains structural integrity during the process.
-
Factors Influencing Safety Factor:
- Material Properties: The choice of materials (e.g., stainless steel, aluminum) affects the chamber's strength, thermal conductivity, and corrosion resistance. Materials with higher tensile strength and durability allow for a higher safety factor.
- Design Considerations: The chamber's geometry, wall thickness, and reinforcement structures (e.g., ribs, flanges) play a significant role in determining its ability to withstand stress.
- Operational Conditions: Factors like maximum pressure, temperature range, and vacuum level influence the required safety factor. For instance, a vacuum hot press system operating at high temperatures and pressures will require a higher safety factor compared to a standard vacuum chamber.
-
Calculating Safety Factor:
- The safety factor is calculated using the formula:
[ \text{Safety Factor} = \frac{\text{Maximum Stress Material Can Withstand}}{\text{Expected Operational Stress}} ] - Engineers use finite element analysis (FEA) and stress simulations to estimate operational stresses and validate the design's safety factor.
- The safety factor is calculated using the formula:
-
Applications in Vacuum Hot Press Systems:
- Vacuum hot press systems combine high temperatures and pressures to process materials like ceramics, composites, and metals. The vacuum chamber in these systems must have a robust safety factor to handle the combined thermal and mechanical stresses.
- The safety factor ensures that the chamber can maintain a vacuum environment while withstanding the external atmospheric pressure and internal heating.
-
Standards and Regulations:
- Vacuum chambers, especially those used in industrial applications, must comply with safety standards and regulations. These standards specify minimum safety factors based on the application and operational conditions.
- For example, ASME Boiler and Pressure Vessel Code provides guidelines for designing pressure vessels, including vacuum chambers, to ensure safety and reliability.
-
Practical Considerations for Buyers:
- When purchasing a vacuum chamber, buyers should consider the safety factor in relation to their specific application. For instance, a vacuum hot press system used in material synthesis may require a higher safety factor than a standard vacuum chamber used for degassing.
- Buyers should also evaluate the manufacturer's design process, material selection, and compliance with industry standards to ensure the chamber's safety and durability.
In conclusion, the safety factor of a vacuum chamber is a crucial parameter that ensures its reliability and safety under operational conditions. For applications like vacuum hot pressing, a higher safety factor is essential to handle the combined thermal and mechanical stresses. Buyers should prioritize safety factor, material quality, and compliance with standards when selecting a vacuum chamber for their needs.
Summary Table:
Aspect | Details |
---|---|
Definition | Ratio of maximum stress to operational stress, ensuring structural integrity. |
Importance | Prevents failures in extreme conditions like high pressure and temperature. |
Key Factors | Material properties, design specifications, and operational conditions. |
Calculation | Safety Factor = Maximum Stress / Operational Stress. |
Applications | Critical in vacuum hot press systems for handling thermal and mechanical stress. |
Standards | Compliance with ASME Boiler and Pressure Vessel Code ensures safety. |
Buyer Considerations | Prioritize safety factor, material quality, and industry standards. |
Ensure your vacuum chamber meets the highest safety standards—contact our experts today for tailored solutions!