Heat treatment is a critical process in metallurgy that involves heating and cooling metals or alloys to achieve desired properties such as hardness, toughness, or ductility. The temperature of heat treatment varies significantly depending on the material, the desired outcome, and the specific heat treatment process being used. Key factors influencing the temperature include the type of metal, the phase transformations required, and the need to avoid defects like oxidation or decarburization. Precise temperature control is essential to ensure consistent product quality and to achieve the desired metallurgical transformations. Below, we explore the key aspects of heat treatment temperature in detail.
Key Points Explained:
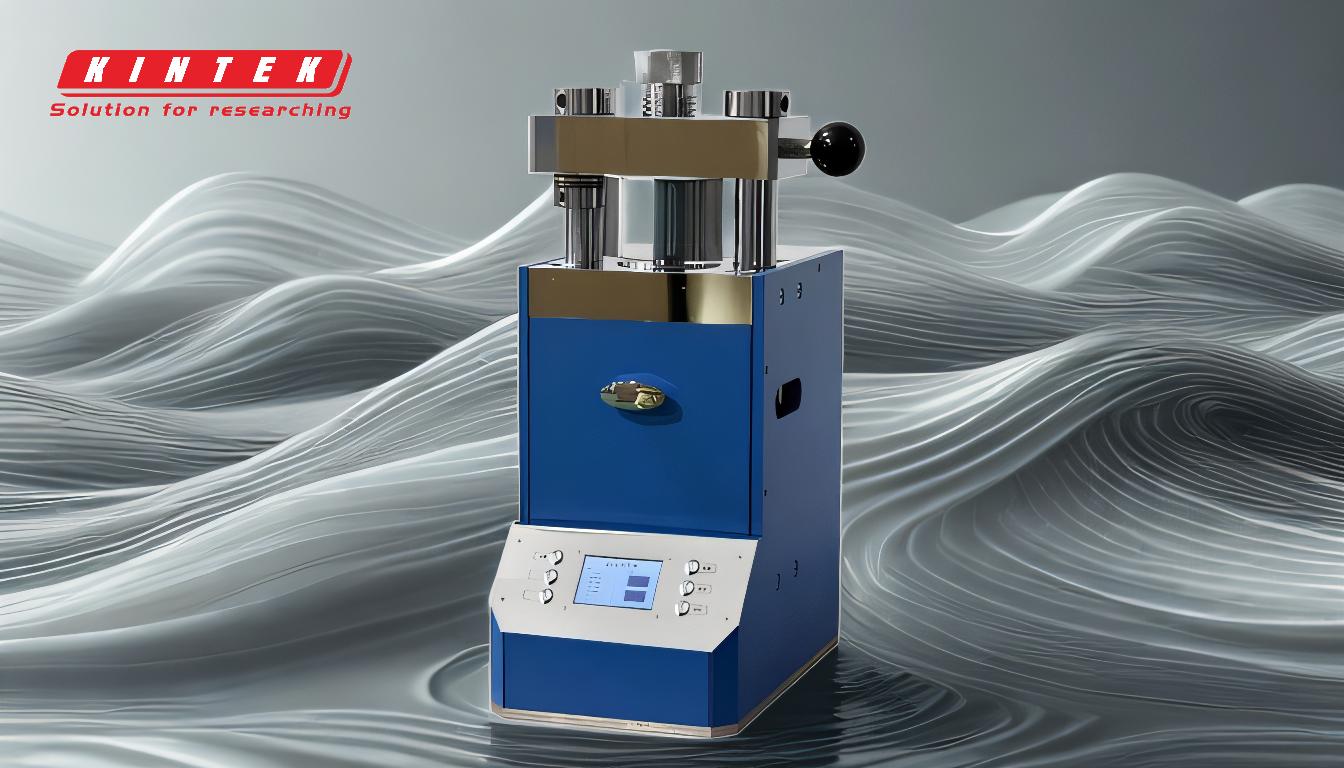
-
Definition and Purpose of Heat Treatment
- Heat treatment involves heating and cooling metals or alloys in the solid state to achieve specific mechanical or physical properties.
- The temperature is chosen based on the material's composition and the desired outcome, such as hardening, annealing, or tempering.
- Heating for hot working (e.g., forging) is not considered heat treatment, as it focuses on shaping rather than altering properties.
-
Factors Influencing Heat Treatment Temperature
- Material Type: Different metals and alloys require specific temperature ranges. For example, steel is often heated to between 700°C and 900°C for hardening, while aluminum alloys may require lower temperatures (around 400°C to 500°C).
- Desired Properties: The temperature is adjusted based on whether the goal is to increase hardness (higher temperatures) or improve ductility (lower temperatures).
- Phase Transformations: Metals undergo phase changes at specific temperatures, such as the austenitizing temperature for steel, which is critical for achieving the desired microstructure.
- Process Type: Common heat treatment processes like annealing, quenching, and tempering each have unique temperature requirements.
-
Temperature Control and Monitoring
- Tight Tolerances: Heat treatment often requires precise temperature control to ensure consistent results. Deviations can lead to defects or inconsistent properties.
- Heat-Up and Cool-Down Rates: The rate at which the material is heated and cooled can significantly impact the final properties. For example, rapid cooling (quenching) is used to harden steel, while slow cooling (annealing) softens it.
- Furnace Atmosphere: The temperature must be controlled in conjunction with the furnace atmosphere to prevent oxidation or decarburization, which can degrade the material's surface quality.
-
Common Heat Treatment Processes and Their Temperatures
- Annealing: Typically involves heating steel to 700°C to 900°C and then slowly cooling it to relieve internal stresses and improve ductility.
- Quenching: Steel is heated to its austenitizing temperature (around 800°C to 900°C) and then rapidly cooled in water, oil, or air to increase hardness.
- Tempering: After quenching, steel is reheated to a lower temperature (150°C to 650°C) to reduce brittleness while maintaining hardness.
- Normalizing: Similar to annealing but involves cooling in air, typically at temperatures between 800°C and 900°C.
-
Importance of Precise Temperature Control
- Consistency: Maintaining the correct temperature ensures uniform properties across the entire part.
- Avoiding Defects: Overheating can cause grain growth or melting, while insufficient heating may not achieve the desired phase transformation.
- Efficiency: Optimizing temperature and process time reduces energy consumption and production costs without compromising quality.
-
Practical Considerations for Equipment and Consumables Purchasers
- Furnace Capabilities: Ensure the furnace can achieve and maintain the required temperature range with precise control.
- Atmosphere Control: Invest in equipment that can regulate the furnace atmosphere to prevent oxidation or decarburization.
- Cooling Systems: Consider the cooling medium (water, oil, or air) and its compatibility with the material and desired properties.
- Monitoring Tools: Use advanced temperature sensors and control systems to maintain tight tolerances and ensure repeatability.
By understanding the temperature requirements of heat treatment, purchasers can select the right equipment and consumables to achieve consistent, high-quality results. Precise temperature control, combined with proper furnace atmosphere and cooling methods, is essential for optimizing the heat treatment process.
Summary Table:
Aspect | Details |
---|---|
Material Type | Steel: 700°C–900°C; Aluminum: 400°C–500°C |
Desired Properties | Hardness (higher temps) or Ductility (lower temps) |
Phase Transformations | Critical for achieving desired microstructure (e.g., austenitizing for steel) |
Process Type | Annealing, Quenching, Tempering, Normalizing |
Temperature Control | Precise control to avoid defects and ensure consistency |
Cooling Methods | Water, oil, or air cooling for specific outcomes |
Ready to optimize your heat treatment process? Contact our experts today for tailored solutions!