Induction heating is a process that generates heat directly within a conductive material by exposing it to a changing magnetic field, typically produced by an alternating current passing through a coil. This method allows for rapid and precise heating without direct contact, making it ideal for applications where contamination or uneven heating is a concern. The temperature range for induction heating can vary significantly depending on the equipment and application, but it generally spans from room temperature up to several thousand degrees Celsius. The specific range depends on factors such as the material being heated, the power of the induction system, and the design of the coil. For example, the TIH 030M/230V induction heating system mentioned in the reference has a temperature control range of 0 - 250 °C (32 - 482 °F), which is suitable for many industrial and laboratory applications. However, induction heating can achieve much higher temperatures for specialized applications, such as metal melting or heat treatment.
Key Points Explained:
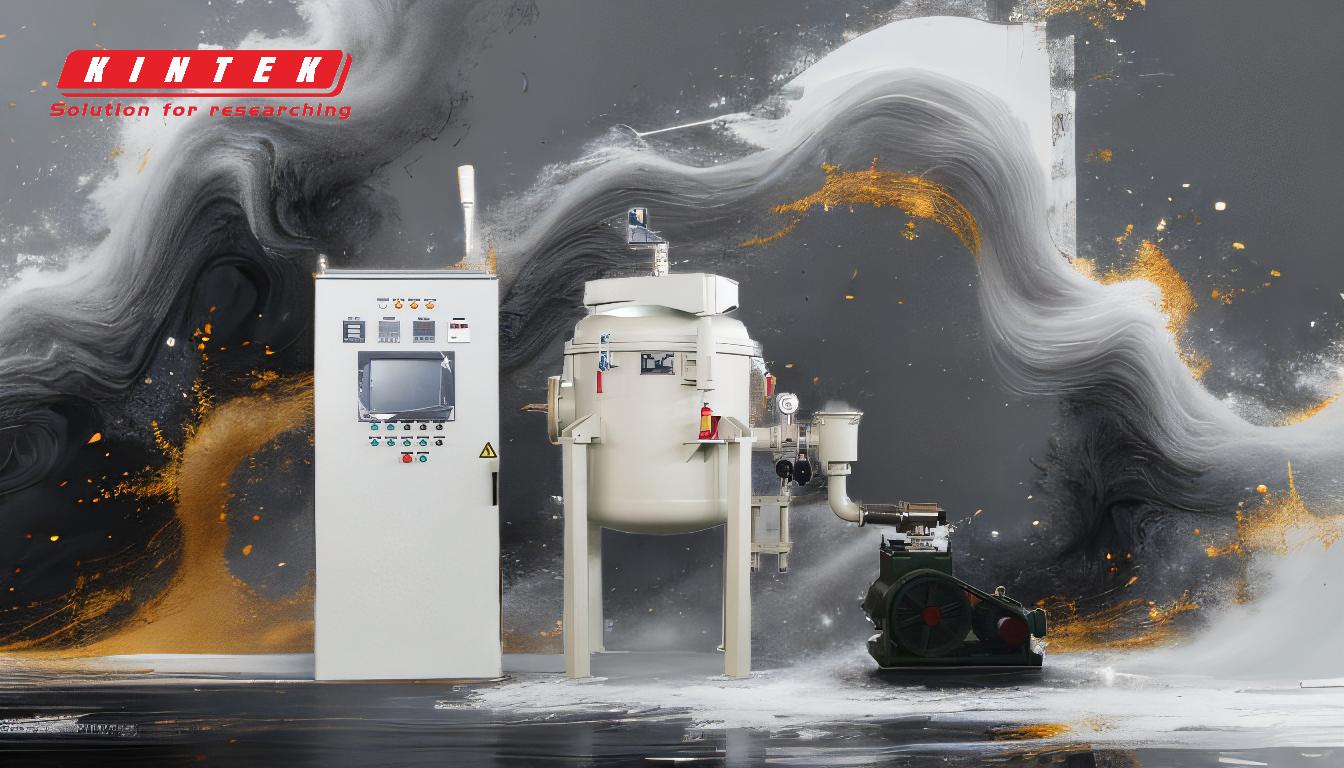
-
Principle of Induction Heating:
- Induction heating works by generating heat directly within a conductive material through a changing magnetic field. This is achieved by passing an alternating current through a coil, which creates the magnetic field. When a conductive workpiece is placed within this field, eddy currents are induced, generating heat due to the material's electrical resistance.
- This method is highly efficient because the heat is generated internally, eliminating the need for external heat sources or direct contact, which can lead to contamination or uneven heating.
-
Temperature Range of Induction Heating:
- The temperature range for induction heating is highly variable and depends on the specific system and application. For example, the TIH 030M/230V system has a temperature control range of 0 - 250 °C (32 - 482 °F), which is suitable for many industrial processes.
- However, induction heating can achieve much higher temperatures, often exceeding 1000 °C (1832 °F), making it suitable for applications like metal melting, forging, and heat treatment. The upper limit is determined by the material's properties and the power of the induction system.
-
Factors Influencing Temperature Range:
- Material Properties: The electrical conductivity and magnetic permeability of the workpiece significantly affect the heating efficiency and achievable temperature. Materials with higher conductivity and permeability heat more effectively.
- Power of the Induction System: Higher power systems can generate stronger magnetic fields, allowing for faster and higher-temperature heating.
- Coil Design: The design and configuration of the induction coil influence the distribution and intensity of the magnetic field, impacting the heating process.
-
Applications of Induction Heating:
- Induction heating is used in a wide range of applications, from low-temperature processes like plastic welding to high-temperature processes like metal melting and hardening. Its ability to provide rapid, localized, and contamination-free heating makes it ideal for industries such as automotive, aerospace, and electronics manufacturing.
-
Advantages of Induction Heating:
- Rapid Heating: Induction heating can achieve high temperatures quickly, reducing processing time.
- Precision: The heat is generated precisely where it is needed, allowing for localized heating without affecting surrounding areas.
- Clean Process: Since there is no direct contact between the heat source and the workpiece, the risk of contamination is minimized.
- Energy Efficiency: Induction heating is highly efficient, as the heat is generated directly within the material, reducing energy loss.
By understanding the principles and factors that influence induction heating, users can select the appropriate system and settings for their specific needs, ensuring optimal performance and results.
Summary Table:
Aspect | Details |
---|---|
Temperature Range | 0 - 250 °C (32 - 482 °F) for standard systems; up to 1000+ °C for high-temp applications |
Influencing Factors | Material properties, induction system power, and coil design |
Applications | Plastic welding, metal melting, forging, heat treatment, and more |
Advantages | Rapid heating, precision, clean process, and energy efficiency |
Unlock the potential of induction heating for your projects—contact our experts today!