The lining of an igbt induction furnace is a critical component that ensures the safe and efficient operation of the furnace. It serves to contain molten metal, protect the furnace structure, and isolate the molten metal from the coil and other external components. The lining must be carefully selected and sintered to achieve the desired performance and durability. The sintering process involves three stages: baking, semi-sintering, and complete sintering, each of which contributes to the formation of a robust, three-layer structure. Factors such as sintering temperature, material composition, and particle size ratio significantly influence the quality and longevity of the lining.
Key Points Explained:
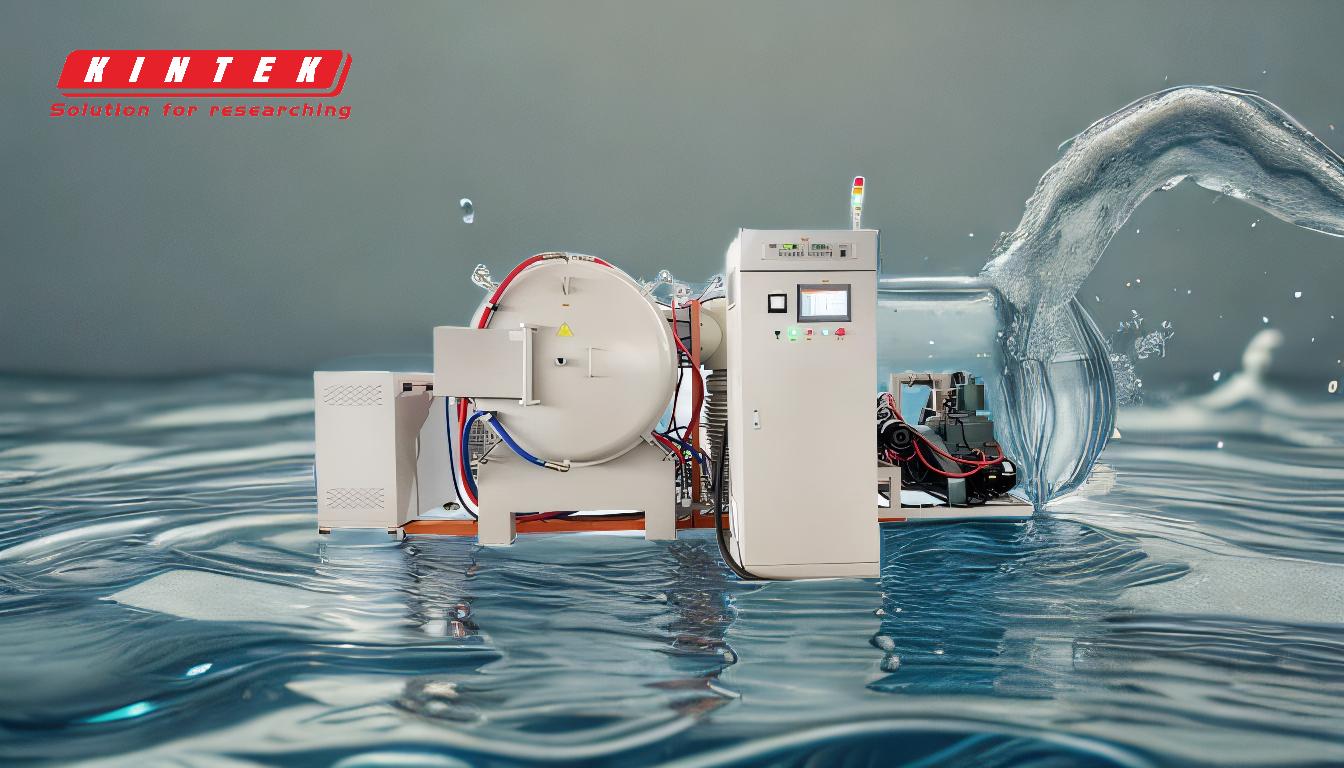
-
Purpose of the Induction Furnace Lining:
- The lining is essential for containing molten metal and preventing it from coming into contact with the furnace's outer structure, such as the coil.
- It acts as a protective barrier, safeguarding the furnace body during operation and ensuring the integrity of the system.
-
Importance of Lining Sintering:
- Sintering is the process of forming the lining into a solid, cohesive structure. A well-executed sintering process results in a lining with a good microstructure, which directly impacts its performance.
- The sintering process is divided into three stages:
- Baking Stage: The lining is heated to 600°C to remove moisture and prepare it for further sintering.
- Semi-Sintering Stage: The temperature is raised to 900°C, held, and then increased to 1200°C to partially sinter the lining.
- Complete Sintering Stage: The final firing temperature is critical, as it determines the service life of the furnace lining. Proper sintering ensures the lining can withstand the high temperatures and stresses encountered during operation.
-
Factors Affecting Lining Sintering:
- Sintering Temperature and Process: The temperature and duration of each sintering stage must be carefully controlled to achieve the desired microstructure and performance.
- Chemical Composition: The materials used in the lining must have the right chemical properties to withstand the high temperatures and corrosive environment of the furnace.
- Particle Size Ratio: The size and distribution of particles in the lining material affect its density and strength. A well-balanced particle size ratio ensures a uniform and durable lining.
-
Three-Layer Structure of the Sintered Lining:
- A properly sintered lining should have a three-layer structure, which enhances its durability and performance.
- Each layer plays a specific role in protecting the furnace and ensuring efficient operation.
-
Material Selection for Lining:
- The choice of lining material is crucial and depends on the type of metal being melted and the operating conditions of the furnace.
- Common materials include refractory ceramics, silica, and alumina, which offer high thermal resistance and durability.
-
Maintenance and Longevity:
- Regular inspection and maintenance of the lining are necessary to ensure its continued performance and safety.
- Proper sintering and material selection can significantly extend the service life of the lining, reducing downtime and maintenance costs.
In summary, the lining of an igbt induction furnace is a vital component that requires careful selection, precise sintering, and regular maintenance. Understanding the sintering process and the factors that influence it is essential for achieving a durable and efficient furnace lining.
Summary Table:
Key Aspect | Details |
---|---|
Purpose | Contains molten metal, protects furnace structure, isolates molten metal. |
Sintering Stages | Baking (600°C), Semi-Sintering (900°C-1200°C), Complete Sintering (critical). |
Critical Factors | Sintering temperature, chemical composition, particle size ratio. |
Material Options | Refractory ceramics, silica, alumina. |
Maintenance | Regular inspection, proper sintering, and material selection. |
Need help selecting the right lining for your induction furnace? Contact our experts today!