Heat treatment processes are designed to alter the mechanical properties of metallic alloys, including strength, hardness, toughness, ductility, and elasticity. Among these processes, hardening is particularly effective in increasing the strength of metals. However, hardening also reduces ductility, making the metal more brittle. To counteract this brittleness, tempering is often employed after hardening to restore some ductility while maintaining increased strength. The overall goal of heat treatment is to manipulate the microstructure of the metal through controlled heating and cooling rates, which directly influences its mechanical properties.
Key Points Explained:
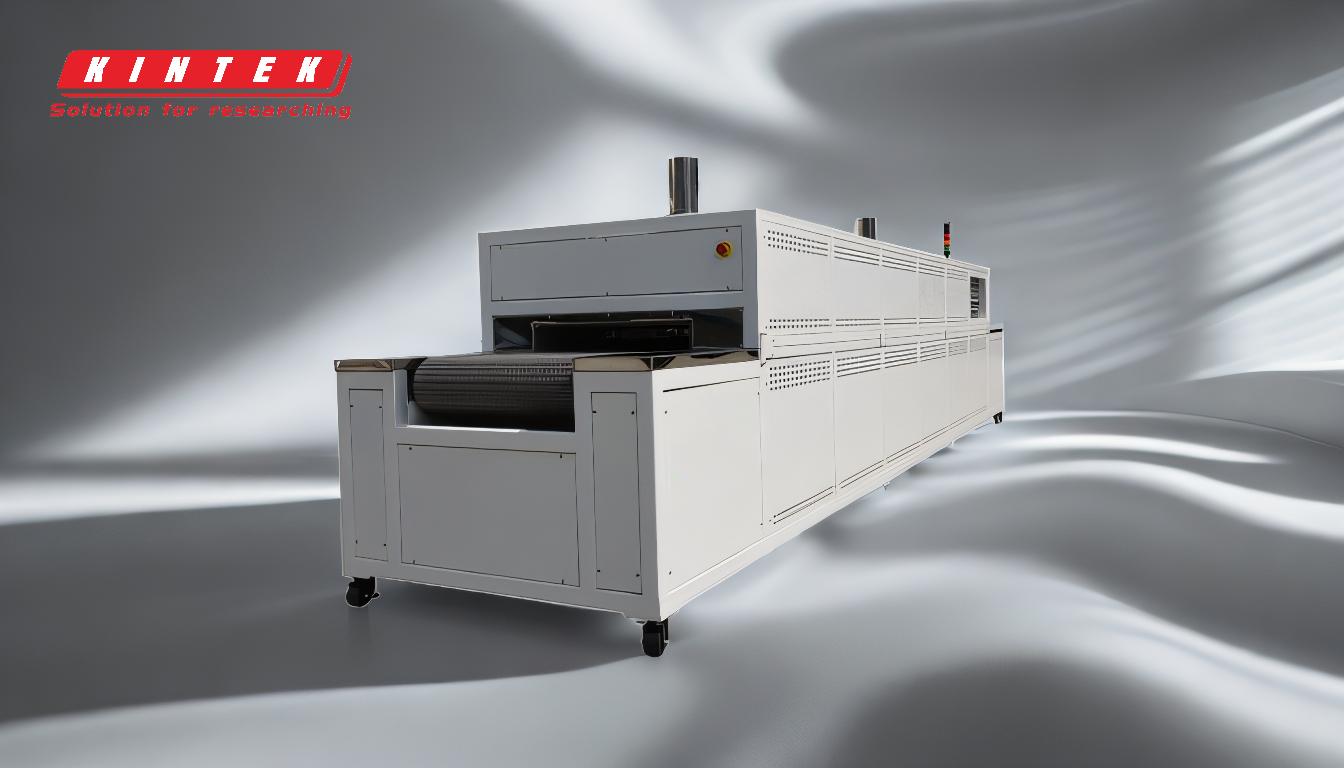
-
Hardening as a Strength-Enhancing Process:
- Hardening involves heating the metal to a specific temperature and then rapidly cooling it, typically through quenching in water, oil, or air.
- This rapid cooling locks the metal's microstructure into a harder state, increasing its strength and hardness.
- However, the process also reduces ductility, making the metal more brittle and prone to cracking under stress.
-
Trade-Off Between Strength and Ductility:
- While hardening significantly increases strength, the accompanying loss of ductility can be a drawback in applications where flexibility and toughness are required.
- This trade-off is a critical consideration when selecting heat treatment processes for specific applications.
-
Tempering to Mitigate Brittleness:
- Tempering is a follow-up process to hardening, where the metal is reheated to a lower temperature and then cooled slowly.
- This process reduces some of the brittleness introduced during hardening while maintaining a significant portion of the increased strength.
- Tempering improves toughness and ductility, making the metal more suitable for applications that require both strength and resistance to impact.
-
Microstructural Changes During Heat Treatment:
- Heat treatment works by altering the microstructure of the metal, which directly affects its mechanical properties.
- During hardening, the rapid cooling process transforms the microstructure into a harder phase, such as martensite in steel.
- Tempering then adjusts this microstructure to achieve a balance between hardness and toughness.
-
Applications of Hardening and Tempering:
- Hardening and tempering are commonly used in the manufacturing of tools, gears, shafts, and other components that require high strength and wear resistance.
- The combination of these processes ensures that the final product has the necessary mechanical properties for its intended use.
-
Importance of Controlled Heating and Cooling Rates:
- The effectiveness of heat treatment depends on precise control over heating and cooling rates.
- Variations in these rates can lead to inconsistent mechanical properties, making process control a critical factor in achieving desired outcomes.
In summary, hardening is the primary heat treatment process that increases the strength of metals, but it must often be followed by tempering to balance the increased strength with adequate ductility and toughness. The careful control of heating and cooling rates during these processes is essential to achieve the desired mechanical properties in the final product.
Summary Table:
Process | Purpose | Key Effects |
---|---|---|
Hardening | Increase strength and hardness | Rapid cooling locks microstructure into a harder state, increases brittleness |
Tempering | Restore ductility and toughness | Reheating reduces brittleness, maintains strength, improves impact resistance |
Microstructural Changes | Alter metal microstructure for desired properties | Hardening forms martensite; tempering adjusts for balanced hardness and toughness |
Applications | Tools, gears, shafts, and components requiring strength and wear resistance | Ensures components meet mechanical property requirements |
Heating/Cooling Control | Achieve consistent mechanical properties | Precise control prevents inconsistencies in strength, hardness, and ductility |
Discover how hardening and tempering can optimize your metal components—contact our experts today for tailored solutions!