Heat treatment in a vacuum furnace offers numerous advantages, making it a preferred method for industries requiring high precision and quality. The primary benefits include the prevention of oxidation, which ensures a contaminant-free end product, and the ability to perform processes like annealing, brazing, and sintering without atmospheric interference. Vacuum heat treatment also enhances productivity by reducing downtime, as parts are ready for further forming immediately. Additionally, it improves mechanical properties, extends the service life of workpieces, and is environmentally friendly, eliminating harmful side effects. The controlled atmosphere allows for precise temperature management and uniform heating, further enhancing the quality of the treated materials.
Key Points Explained:
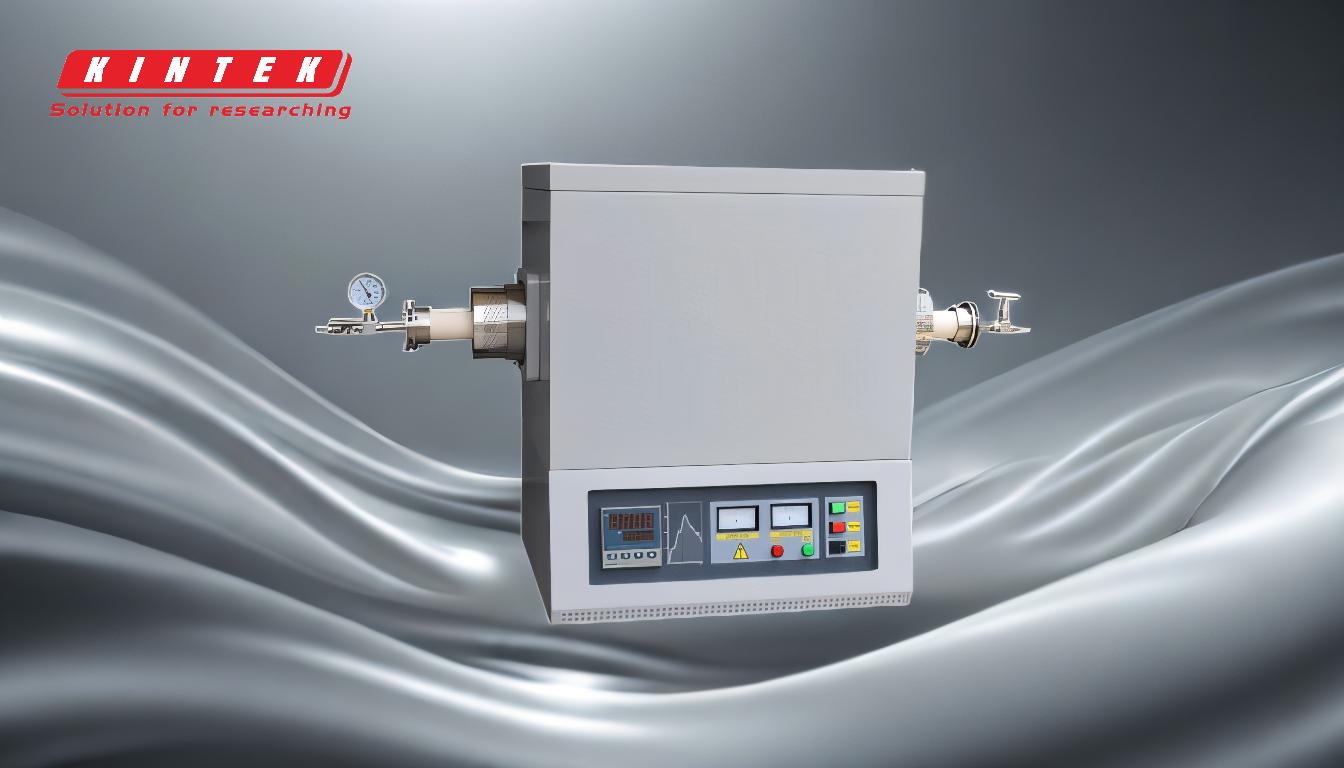
-
Prevention of Oxidation:
- Heating in a vacuum furnace prevents oxidation, which is crucial for maintaining the purity and integrity of the metal. Oxidation can lead to defects and contaminants, which are undesirable in high-precision industries.
- The absence of oxygen and other reactive gases ensures that the metal remains free from scale and other surface imperfections, resulting in a higher quality end product.
-
Controlled Atmosphere for Precise Temperature Management:
- A vacuum furnace provides a controlled environment that allows for precise temperature management. This is essential for processes like annealing, brazing, and sintering, where even minor temperature fluctuations can affect the outcome.
- Uniform heating is achieved, ensuring that all parts of the workpiece are treated consistently, which is critical for maintaining the mechanical properties and dimensional accuracy of the components.
-
Reduction of Downtime and Increased Productivity:
- Vacuum heat treatment allows parts to be ready for further forming immediately after the process. This reduces downtime and increases overall productivity, as there is no need for additional cleaning or surface treatment.
- The elimination of post-treatment cleaning steps saves time and effort, which is particularly beneficial in industries where efficiency is critical.
-
Cost Reduction and Improved Mechanical Properties:
- The process reduces costs by minimizing the need for additional treatments and by extending the service life of the workpieces. The improved mechanical properties, such as increased strength and durability, result in longer-lasting components.
- The degassing effect of vacuum heat treatment enhances the overall quality of the materials, making them more resistant to wear and tear.
-
Environmental Friendliness:
- Vacuum heat treatment is environmentally friendly as it does not produce harmful side effects. Unlike other heat treatment methods that may release toxic gases or by-products, vacuum heat treatment is a clean process.
- The absence of harmful emissions makes it a sustainable choice for industries looking to reduce their environmental impact.
-
Vacuum Pumping System:
- The vacuum pumping system evacuates air and its reactive elements from the heat treating chamber, creating a controlled environment. While it cannot remove all the air, it removes enough to prevent significant reactions with the metal.
- Different types of pumps, such as mechanical pumps and oil diffusion pumps, are used depending on the material being treated. For highly reactive materials, a 'super-clean' environment may be required, necessitating the use of additional pumps.
-
Medium Vacuum Level for Quenching:
- A medium vacuum level, typically around 4x10^-1 Pa, is suitable for quenching heat treatment. This level of vacuum is effective for treating materials like bearing steel, die steel, and structural steel.
- Two-stage pumps, including front-stage pumps and roots pumps, are commonly used to achieve the necessary vacuum levels for these processes.
In summary, heat treatment in a vacuum furnace offers a range of benefits, from preventing oxidation and ensuring high-quality end products to reducing costs and improving mechanical properties. The controlled environment allows for precise temperature management and uniform heating, while the process itself is environmentally friendly and enhances productivity. These advantages make vacuum heat treatment an essential process in industries requiring high precision and quality.
Summary Table:
Key Benefits | Explanation |
---|---|
Prevention of Oxidation | Ensures contaminant-free, high-quality end products by eliminating surface defects. |
Controlled Atmosphere | Enables precise temperature management and uniform heating for consistent results. |
Reduced Downtime | Parts are ready for further forming immediately, enhancing productivity. |
Improved Mechanical Properties | Increases strength, durability, and extends the service life of workpieces. |
Environmental Friendliness | No harmful emissions, making it a sustainable and clean process. |
Cost Reduction | Minimizes additional treatments and extends the lifespan of materials. |
Unlock the full potential of vacuum heat treatment for your industry—contact our experts today!