Heating elements can indeed use a significant amount of electricity, but the actual consumption depends on factors such as the wattage of the heating element, the duration of use, and the efficiency of the device. Generally, heating elements convert electrical energy into heat, and their power consumption is directly related to their wattage. For example, a 1500-watt heating element running for one hour will consume 1.5 kWh of electricity. While heating elements are efficient in converting electricity to heat, their high power requirements can lead to substantial electricity usage, especially in appliances like water heaters, space heaters, or ovens. To minimize energy consumption, users can opt for energy-efficient models, insulate their homes, or use timers to control usage.
Key Points Explained:
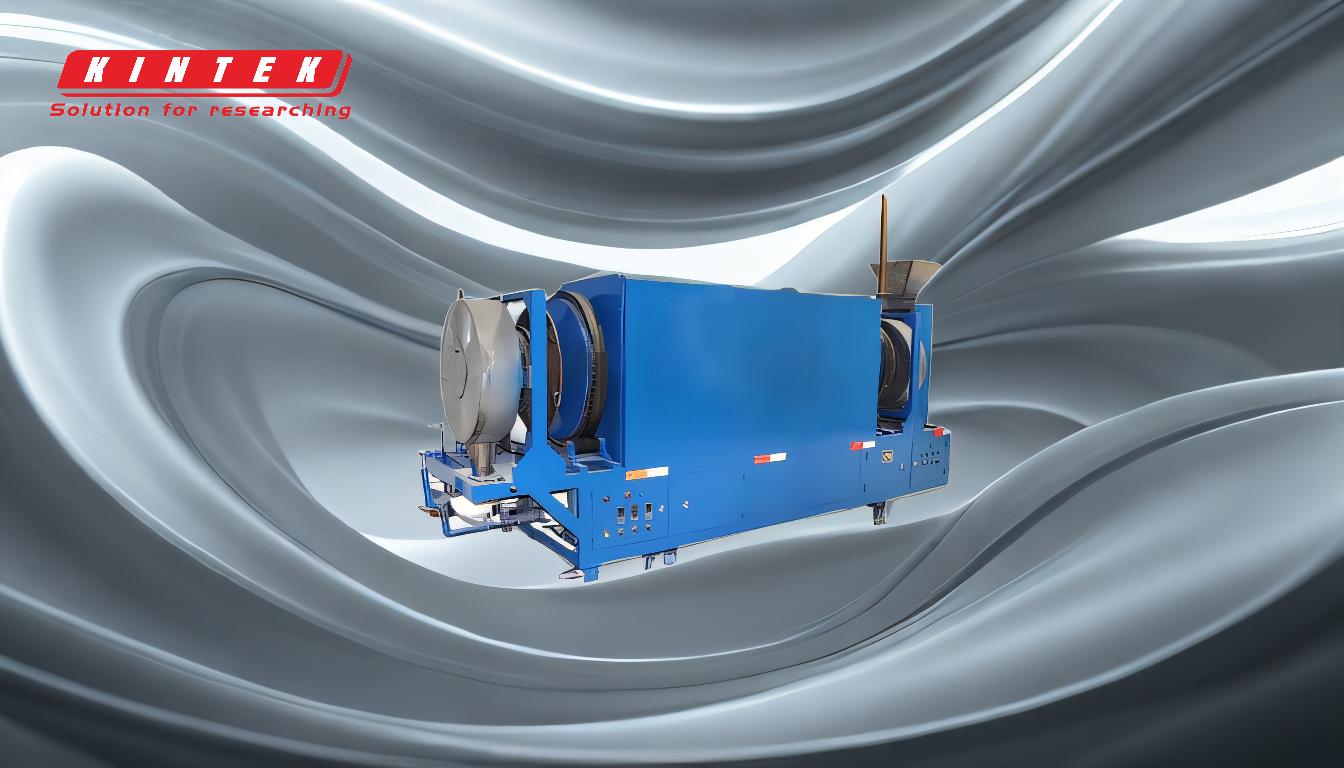
-
How Heating Elements Work:
- Heating elements convert electrical energy into heat through resistance. When electricity passes through the element, it encounters resistance, which generates heat.
- This process is highly efficient, as nearly all the electrical energy is converted into heat. However, the efficiency of the overall appliance may vary depending on insulation and design.
-
Factors Affecting Electricity Usage:
- Wattage: The power rating of the heating element (measured in watts) directly determines how much electricity it consumes. Higher wattage means more energy usage. For example, a 2000-watt heater uses twice as much electricity as a 1000-watt heater when running for the same duration.
- Duration of Use: The longer a heating element operates, the more electricity it consumes. For instance, a 1500-watt heater running for 2 hours will use 3 kWh of electricity.
- Efficiency of the Appliance: While heating elements themselves are efficient, the overall efficiency of the appliance (e.g., a water heater or oven) depends on factors like insulation, thermostat accuracy, and heat distribution.
-
Examples of Heating Elements in Common Appliances:
- Space Heaters: Portable space heaters often use heating elements with wattages ranging from 500 to 1500 watts. These can consume a significant amount of electricity if used continuously.
- Water Heaters: Electric water heaters typically have heating elements with wattages between 1500 and 4500 watts. Their energy consumption depends on the size of the tank and the frequency of use.
- Ovens and Stoves: Electric ovens and stovetops use heating elements to cook food. Their wattage can range from 1000 to 5000 watts, depending on the model and cooking settings.
-
Energy Consumption Calculations:
- To calculate the energy consumption of a heating element, use the formula: Energy (kWh) = Power (kW) × Time (hours).
- For example, a 2000-watt (2 kW) heating element running for 3 hours will consume 6 kWh of electricity. At an average electricity rate of $0.12 per kWh, this would cost $0.72.
-
Strategies to Reduce Electricity Usage:
- Choose Energy-Efficient Appliances: Look for appliances with high energy efficiency ratings (e.g., ENERGY STAR certified products).
- Use Timers or Thermostats: Programmable thermostats or timers can help control the operation of heating elements, reducing unnecessary energy consumption.
- Improve Insulation: Proper insulation in homes or appliances (e.g., water heaters) can minimize heat loss, reducing the need for prolonged heating.
- Optimize Usage Patterns: For example, using a space heater only in occupied rooms or lowering the thermostat on a water heater can save energy.
-
Cost Implications:
- The cost of operating a heating element depends on the local electricity rate and the appliance's energy consumption. For instance, a 1500-watt heater used for 5 hours a day at $0.12 per kWh would cost $0.90 per day or approximately $27 per month.
- High-wattage appliances like electric water heaters or ovens can significantly impact monthly electricity bills if used extensively.
By understanding these factors, users can make informed decisions about their heating needs and implement strategies to minimize electricity usage while maintaining comfort and functionality.
Summary Table:
Factor | Impact on Electricity Usage |
---|---|
Wattage | Higher wattage = more energy consumption (e.g., 2000W uses twice as much as 1000W). |
Duration of Use | Longer operation = higher energy usage (e.g., 1500W for 2 hours = 3 kWh). |
Appliance Efficiency | Poor insulation or design reduces overall efficiency, increasing energy needs. |
Common Appliances | Space heaters (500-1500W), water heaters (1500-4500W), ovens (1000-5000W). |
Energy Consumption | Formula: Energy (kWh) = Power (kW) × Time (hours). Example: 2000W for 3 hours = 6 kWh. |
Cost Implications | Example: 1500W heater used 5 hours/day at $0.12/kWh = $0.90/day or ~$27/month. |
Energy-Saving Tips | Use energy-efficient models, timers, insulation, and optimize usage patterns. |
Ready to reduce your energy costs? Contact us today for expert advice on energy-efficient heating solutions!