Annealing is a critical heat treatment process used to soften metals, improve ductility, and relieve internal stresses. The number of times a metal can be annealed depends on factors such as the type of metal, its composition, and the specific application. While there is no fixed limit, repeated annealing can lead to grain growth, oxidation, or other material degradation if not controlled properly. Proper temperature, cooling rate, and environmental conditions are essential to ensure the metal retains its desired properties. Below, we explore the key considerations and factors influencing the annealing process and its repeatability.
Key Points Explained:
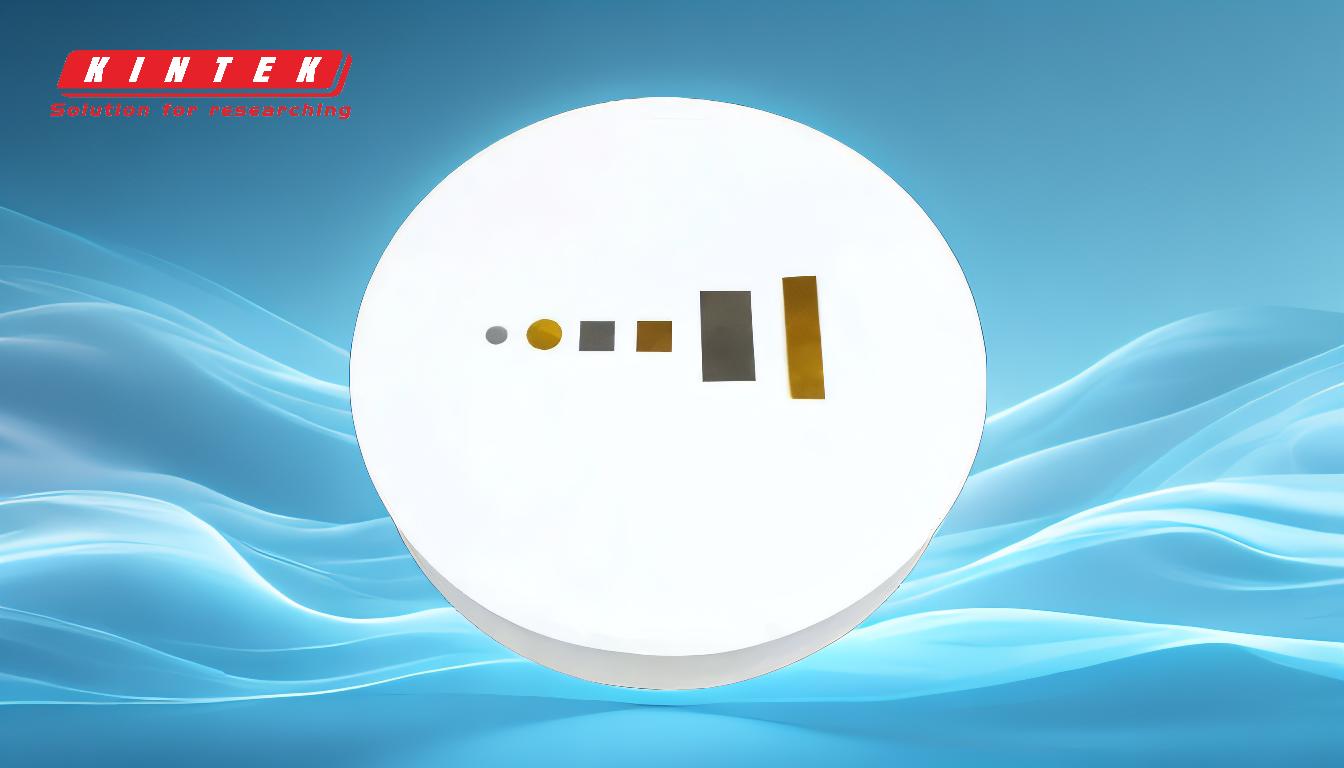
-
What is Annealing and Its Purpose?
- Annealing is a heat treatment process that involves heating a metal to a specific temperature, holding it at that temperature, and then cooling it slowly.
- The primary goals of annealing are to:
- Soften the metal for improved workability.
- Reduce internal stresses caused by machining, welding, or cold working.
- Enhance ductility and toughness.
- Refine the grain structure for better mechanical properties.
-
Factors Affecting the Number of Annealing Cycles
-
Metal Type and Composition:
- Different metals and alloys respond differently to annealing. For example, steel can be annealed multiple times, but excessive annealing may lead to grain coarsening or decarburization.
- Non-ferrous metals like copper or aluminum can also be annealed repeatedly, but their oxide layers may thicken with each cycle.
-
Temperature Control:
- Each annealing cycle must maintain precise temperature control to avoid overheating or underheating, which can degrade the metal's properties.
-
Cooling Rate:
- Slow cooling is essential to achieve the desired microstructure. Rapid cooling may negate the benefits of annealing.
-
Environmental Conditions:
- Exposure to oxygen or contaminants during annealing can cause oxidation or surface degradation, limiting the number of cycles.
-
Metal Type and Composition:
-
Impact of Repeated Annealing
-
Grain Growth:
- Repeated annealing can lead to grain coarsening, which reduces the metal's strength and toughness.
-
Oxidation and Surface Damage:
- Each annealing cycle exposes the metal to high temperatures, increasing the risk of oxidation or scaling, especially in non-inert environments.
-
Material Degradation:
- Over time, repeated annealing may cause changes in the metal's microstructure, leading to reduced mechanical properties.
-
Grain Growth:
-
Practical Considerations for Equipment and Consumables Purchasers
-
Material Selection:
- Choose metals with compositions that withstand multiple annealing cycles, such as certain grades of stainless steel or copper alloys.
-
Annealing Equipment:
- Invest in furnaces with precise temperature control and inert gas environments to minimize oxidation and contamination.
-
Cooling Systems:
- Ensure proper cooling systems are in place to achieve the desired cooling rates without compromising the metal's properties.
-
Monitoring and Testing:
- Regularly test the metal's mechanical properties and microstructure after each annealing cycle to ensure quality and performance.
-
Material Selection:
-
Conclusion
- While there is no strict limit to the number of times a metal can be annealed, the process must be carefully controlled to avoid material degradation. Factors such as metal type, temperature control, cooling rate, and environmental conditions play a significant role in determining the feasibility of repeated annealing. For equipment and consumables purchasers, investing in high-quality annealing equipment and monitoring systems is essential to maximize the benefits of this process while maintaining the metal's integrity.
Summary Table:
Key Factor | Impact on Annealing |
---|---|
Metal Type | Different metals respond uniquely; steel and non-ferrous metals have varying limits. |
Temperature Control | Precise heating prevents overheating or underheating, ensuring desired properties. |
Cooling Rate | Slow cooling is essential for proper microstructure; rapid cooling can negate benefits. |
Environmental Conditions | Exposure to oxygen or contaminants can cause oxidation or surface degradation. |
Repeated Annealing | Can lead to grain growth, oxidation, or material degradation if not controlled properly. |
Need expert advice on annealing processes? Contact us today to optimize your heat treatment solutions!