In DC sputtering, the required pressure typically ranges from 1 to 15 mTorr (millitorr), depending on the specific application, target material, and desired film properties. The pressure plays a critical role in determining the energy distribution of sputtered atoms, plasma density, and the overall quality of the deposited film. Lower pressures favor high-energy ballistic impacts, while higher pressures promote diffusive motion and thermalization of sputtered atoms. The optimal pressure must balance these effects to achieve the desired film uniformity, density, and adhesion.
Key Points Explained:
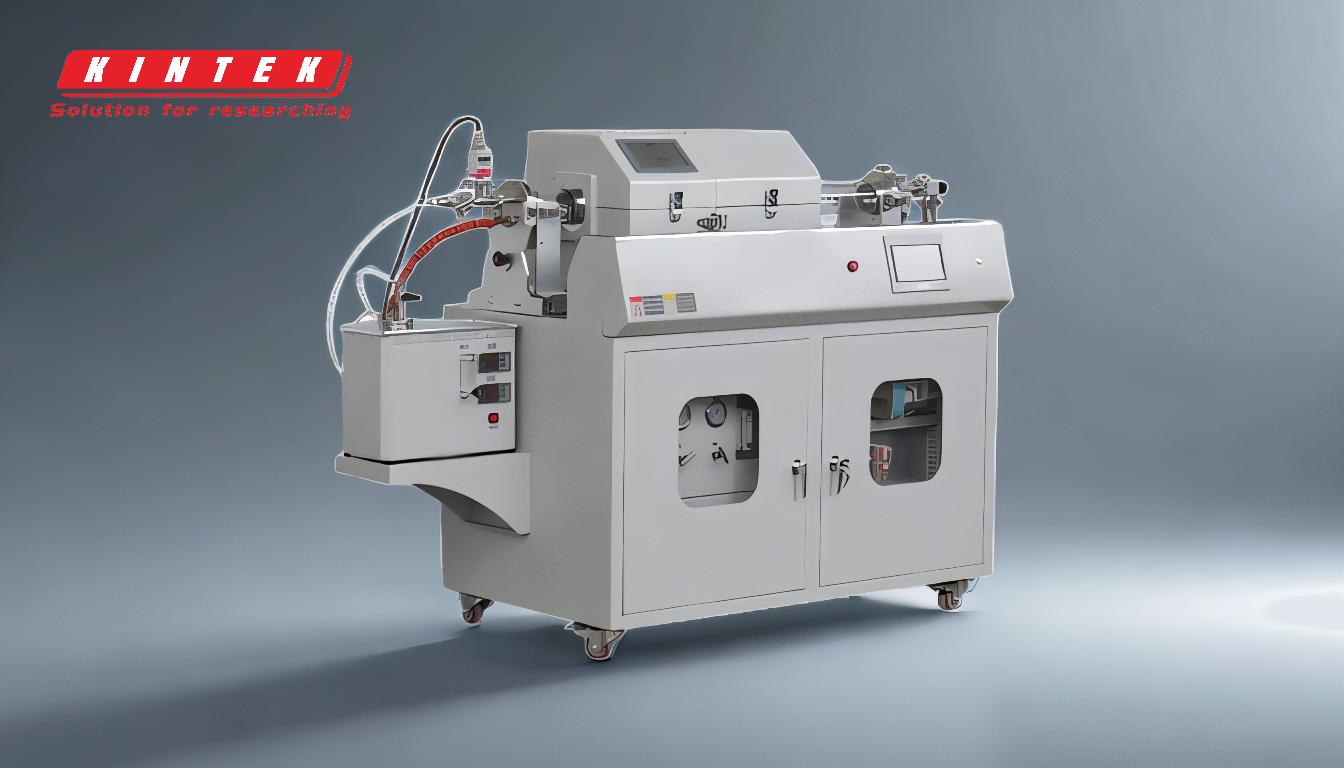
-
Pressure Range in DC Sputtering:
- The typical operating pressure for DC sputtering is 1 to 15 mTorr.
- Lower pressures (1–5 mTorr) allow for high-energy ballistic impacts, where sputtered atoms travel directly to the substrate with minimal collisions.
- Higher pressures (5–15 mTorr) promote diffusive motion, where sputtered atoms undergo multiple collisions with gas atoms, leading to a more random, thermalized deposition.
-
Role of Pressure in Sputtering:
- Mean Free Path: Pressure determines the mean free path of sputtered atoms. At lower pressures, the mean free path is longer, enabling high-energy deposition. At higher pressures, the mean free path shortens, leading to thermalized motion.
- Plasma Density: Pressure influences plasma density, which affects the ionization level and energy of sputtered atoms. The plasma density can be calculated using the formula: [ n_e = \left(\frac{1}{\lambda_{De}^2}\right) \times \left(\frac{\omega^2 m_e \epsilon_0}{e^2}\right) ] where (n_e) is the plasma density, (\lambda_{De}) is the Debye length, (\omega) is the angular frequency, (m_e) is the electron mass, (\epsilon_0) is the permittivity of free space, and (e) is the elementary charge.
- Film Quality: Pressure optimization is crucial for achieving the desired film properties, such as uniformity, density, and adhesion.
-
Factors Influencing Pressure Selection:
- Target Material: Different materials require different pressures to achieve optimal sputtering yields. For example, heavier target atoms may benefit from higher pressures to ensure sufficient energy transfer.
- Substrate Requirements: The desired film properties (e.g., density, uniformity) influence the choice of pressure. High-energy impacts at lower pressures are ideal for dense films, while thermalized deposition at higher pressures improves coverage on complex geometries.
- Power Source: DC sputtering typically operates at lower pressures compared to RF sputtering due to differences in plasma generation and ionization efficiency.
-
Impact of Pressure on Sputtering Yield:
- The sputtering yield (number of target atoms ejected per incident ion) depends on the energy of the ions, the mass of the target atoms, and the angle of incidence.
- At lower pressures, higher ion energies result in a higher sputtering yield, but excessive energy can lead to substrate damage.
- At higher pressures, the sputtering yield may decrease due to energy loss from collisions, but the thermalized motion improves film uniformity.
-
Practical Considerations for Pressure Control:
- Chamber Design: The vacuum system must be capable of maintaining the desired pressure range consistently.
- Gas Flow Rate: The flow rate of the sputtering gas (e.g., argon) must be optimized to achieve the desired pressure and plasma conditions.
- Process Monitoring: Real-time monitoring of pressure and plasma parameters ensures consistent film quality and process reproducibility.
-
Trade-offs in Pressure Selection:
- Low Pressure: Advantages include high-energy deposition, dense films, and faster deposition rates. Disadvantages include potential substrate damage and poor coverage on complex geometries.
- High Pressure: Advantages include improved film uniformity and better coverage on complex substrates. Disadvantages include lower deposition rates and potential film porosity.
By carefully selecting and controlling the pressure in DC sputtering, manufacturers can optimize the deposition process to achieve the desired film properties for their specific application.
Summary Table:
Aspect | Low Pressure (1–5 mTorr) | High Pressure (5–15 mTorr) |
---|---|---|
Energy Distribution | High-energy ballistic impacts | Diffusive, thermalized motion |
Film Uniformity | Lower (direct impacts) | Higher (randomized deposition) |
Deposition Rate | Faster | Slower |
Substrate Coverage | Poor on complex geometries | Better on complex geometries |
Film Density | Denser | Potentially porous |
Substrate Damage Risk | Higher | Lower |
Need help optimizing your DC sputtering process? Contact our experts today for tailored solutions!