Cleaning a tube furnace is a critical maintenance task to ensure its longevity and optimal performance. The process involves allowing the furnace to cool completely, removing loose debris with a soft brush or vacuum, and gently wiping the interior with a damp cloth and mild detergent. It's essential to avoid damaging heating elements and electrical components during cleaning. Regular cleaning, ideally after each use and a thorough cleaning monthly, helps prevent residue buildup and extends the furnace's service life. Additionally, using a boat crucible to hold materials during burning can protect the furnace tube from direct exposure to reactive substances.
Key Points Explained:
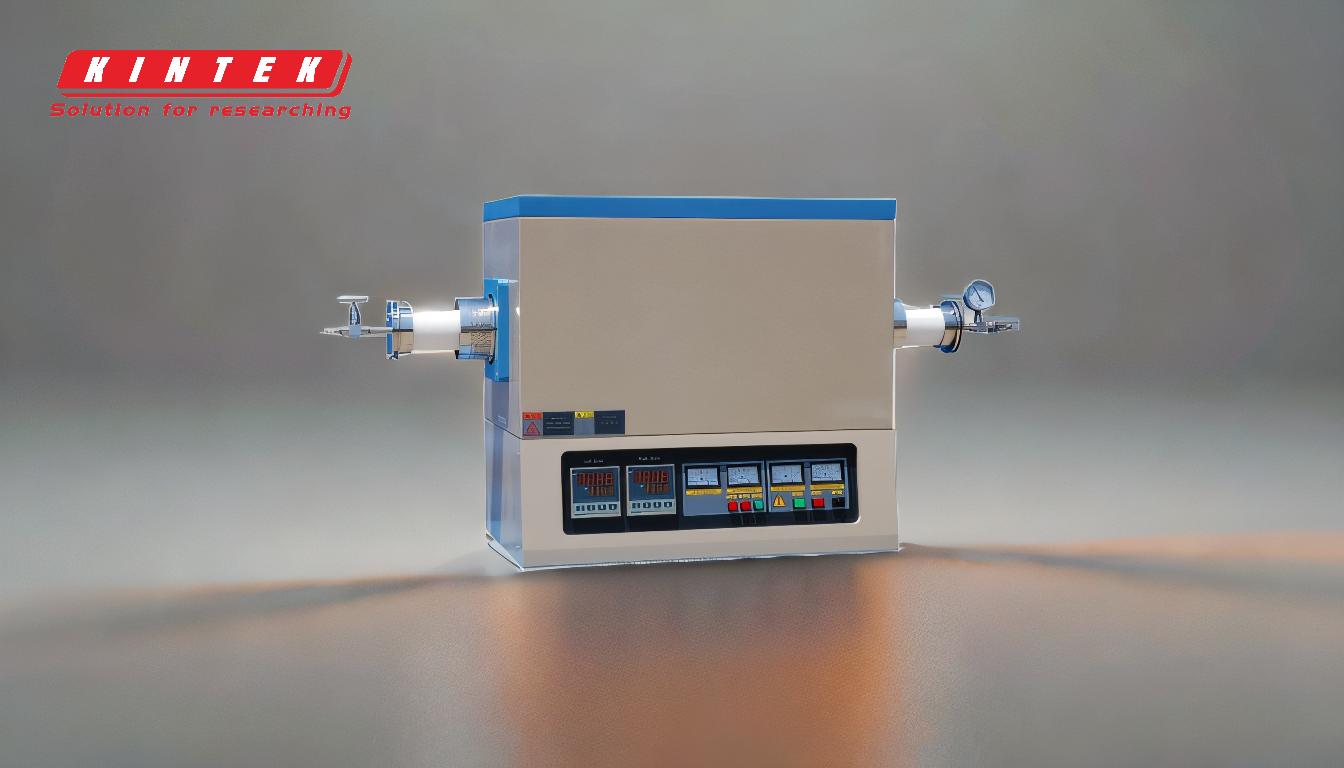
-
Allow the Furnace to Cool Completely
- Before starting any cleaning process, ensure the tube furnace has cooled down entirely. This prevents burns and ensures safe handling of the equipment.
- Cooling also avoids thermal shock, which could damage the furnace components.
-
Remove Loose Debris
- Use a soft brush or vacuum to remove loose debris, such as dust, ash, or particles, from the interior of the furnace.
- Be cautious not to damage the heating elements or insulation, as these are critical for the furnace's operation.
-
Clean the Interior with Mild Detergent
- Mix water with a mild detergent to create a cleaning solution.
- Apply the solution to a clean cloth and gently wipe the interior surfaces of the furnace.
- Avoid direct contact with electrical components and heating elements to prevent damage or safety hazards.
-
Rinse and Dry Thoroughly
- Rinse the cloth thoroughly and wring it out to remove detergent residues.
- Repeat the wiping process until all detergent is removed from the furnace interior.
- Finish by wiping the furnace with a clean, dry cloth to ensure no moisture remains, which could cause corrosion or electrical issues.
-
Use a Boat Crucible for Material Placement
- To protect the furnace tube, always place materials in a boat crucible during burning.
- This prevents direct contact between reactive substances and the furnace tube, reducing the risk of contamination and extending the tube's service life.
-
Cleaning Frequency
- Clean the furnace after each use to remove any residue or particles that may have accumulated.
- Perform a more thorough cleaning at least once a month, depending on usage and the manufacturer's recommendations.
- Regular cleaning ensures the furnace operates efficiently and maintains its performance over time.
-
Avoid Reactive Substances
- Keep the furnace tube clean and free of substances that react with SiO2 or other materials in the tube.
- This precaution helps maintain the integrity of the tube and prevents damage caused by chemical reactions.
By following these steps and guidelines, you can effectively clean and maintain your tube furnace, ensuring its reliability and extending its lifespan.
Summary Table:
Step | Details |
---|---|
1. Allow the Furnace to Cool | Ensure the furnace cools completely to prevent burns and thermal shock. |
2. Remove Loose Debris | Use a soft brush or vacuum to clear dust and particles without damaging components. |
3. Clean with Mild Detergent | Wipe the interior gently with a damp cloth and mild detergent, avoiding electrical parts. |
4. Rinse and Dry Thoroughly | Remove detergent residues and dry the furnace to prevent corrosion or electrical issues. |
5. Use a Boat Crucible | Protect the furnace tube by placing materials in a boat crucible during use. |
6. Cleaning Frequency | Clean after each use and perform a thorough cleaning monthly for best results. |
7. Avoid Reactive Substances | Keep the tube free of substances that react with SiO2 or other tube materials. |
Ensure your tube furnace stays in top condition—contact our experts today for personalized advice!