Channel induction furnaces, particularly those utilizing IGBT technology, offer a range of advantages that make them highly efficient and effective for various industrial applications. These furnaces are known for their fast heating speed, high production efficiency, and precise temperature control. They also contribute to a superior working environment by reducing pollution and energy consumption. The use of IGBT induction furnaces further enhances these benefits by providing better energy efficiency and control over the melting process. Below, we will explore the key advantages of channel induction furnaces in detail.
Key Points Explained:
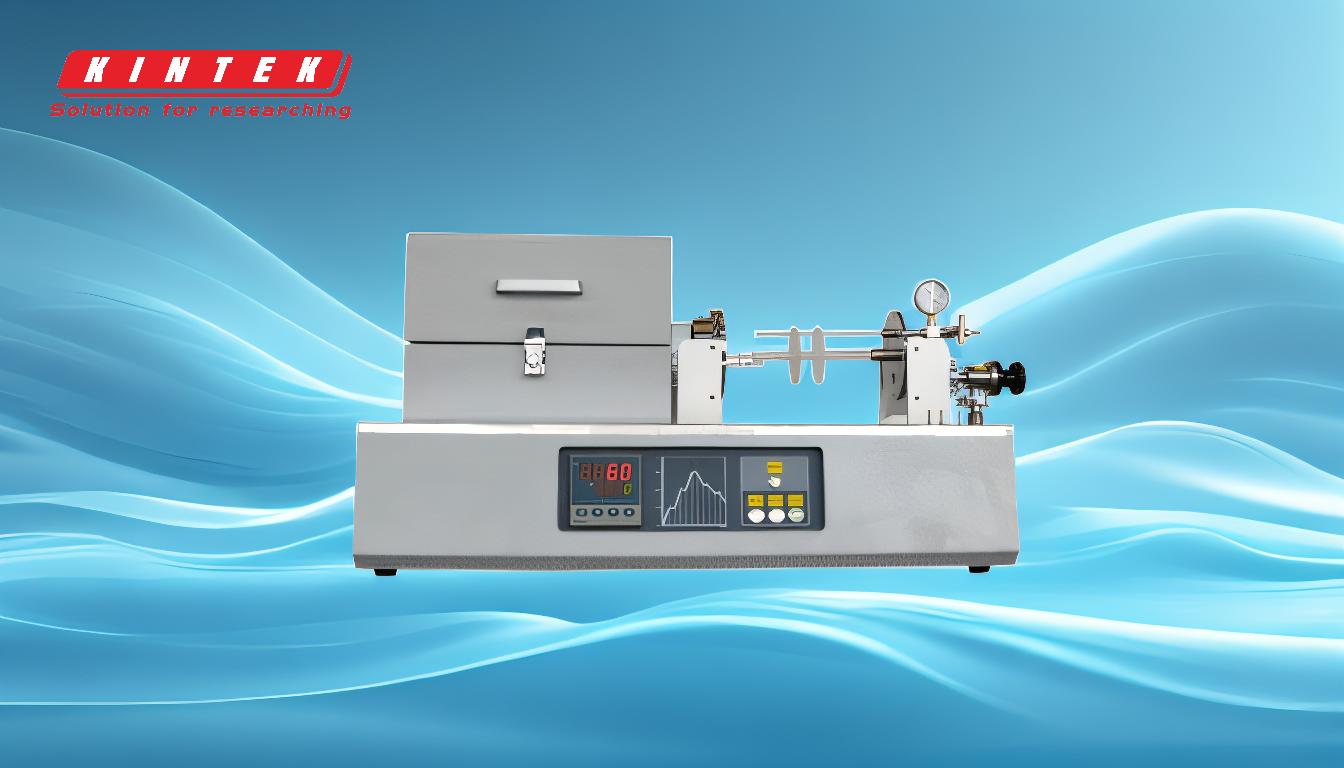
-
Fast Heating Speed and High Production Efficiency:
- Channel induction furnaces, especially those equipped with IGBT induction furnace technology, heat up quickly due to the high-frequency power they utilize. This rapid heating leads to shorter melting times and higher production rates.
- The fast heating speed is beneficial for industries that require quick turnaround times, such as metal casting and foundries.
-
Less Oxidation and Decarburization:
- The electromagnetic induction process minimizes the exposure of the metal to oxygen, reducing oxidation and decarburization. This results in higher-quality metal with fewer impurities.
- This advantage is particularly important in industries where metal purity is critical, such as in the production of high-grade steel and alloys.
-
Energy Conservation and Low Power Consumption:
- Induction furnaces are known for their energy efficiency. The IGBT technology further enhances this by providing precise control over the power input, reducing energy wastage.
- The compact design of these furnaces also contributes to lower energy consumption, making them a cost-effective solution for industrial heating and melting processes.
-
Superior Working Environment:
- Unlike traditional furnaces, induction furnaces do not produce flames or significant amounts of exhaust gas, making the working environment safer and more comfortable for workers.
- The reduced noise levels and absence of harmful emissions contribute to a healthier workplace.
-
Precise Temperature Control:
- The advanced control systems in IGBT induction furnaces allow for precise regulation of the furnace temperature. This precision is crucial for processes that require specific temperature ranges to achieve the desired metal properties.
- Accurate temperature control also helps in minimizing material waste and improving the overall quality of the final product.
-
Environmental Benefits:
- Induction furnaces are more environmentally friendly compared to traditional arc furnaces. They do not use graphite electrodes, which eliminates carbon pick-up and reduces the generation of waste and pollution.
- The reduced environmental impact makes induction furnaces a more sustainable choice for industries looking to minimize their carbon footprint.
-
Compact Installation and Lightweight Design:
- The small size and lightweight nature of induction furnaces make them easy to install and integrate into existing production lines. This is particularly advantageous for facilities with limited space.
- The compact design also contributes to the overall efficiency of the furnace, as it reduces the amount of energy required to heat the furnace itself.
-
Versatility in Material Melting:
- Induction furnaces can melt a wide range of materials, from ferrous to non-ferrous metals. This versatility makes them suitable for various industrial applications, including steel production, aluminum casting, and more.
- The ability to handle different materials without significant changes to the furnace setup adds to the operational flexibility and cost-effectiveness of these furnaces.
In summary, channel induction furnaces, particularly those utilizing IGBT technology, offer numerous advantages that make them a superior choice for industrial heating and melting processes. Their fast heating speed, energy efficiency, precise temperature control, and environmental benefits make them an ideal solution for industries looking to improve production efficiency and reduce operational costs.
Summary Table:
Advantage | Description |
---|---|
Fast Heating Speed | High-frequency power ensures rapid heating, reducing melting times. |
Less Oxidation & Decarburization | Minimizes metal exposure to oxygen, improving metal purity. |
Energy Conservation | IGBT technology reduces power consumption and energy wastage. |
Superior Working Environment | No flames or harmful emissions, creating a safer and healthier workplace. |
Precise Temperature Control | Advanced systems ensure accurate temperature regulation for better results. |
Environmental Benefits | No graphite electrodes, reducing carbon pick-up and pollution. |
Compact Installation | Lightweight and space-saving design for easy integration. |
Versatility in Material Melting | Suitable for ferrous and non-ferrous metals, enhancing operational flexibility. |
Ready to enhance your industrial processes? Contact us today to learn more about channel induction furnaces!