Induction furnaces, particularly core induction furnaces, are widely recognized for their efficiency, precision, and environmental benefits in metal melting and alloying processes. They offer fast heating speeds, high production efficiency, and minimal material loss, making them ideal for preserving valuable alloying elements. The absence of combustion or arcs ensures a cleaner process with reduced contamination and precise temperature control. Additionally, the electromagnetic stirring action promotes a homogeneous mixture of metals, eliminating the need for frequent sampling. These furnaces also contribute to a safer and healthier working environment by reducing pollutants and energy consumption, making them a preferred choice in modern industrial settings.
Key Points Explained:
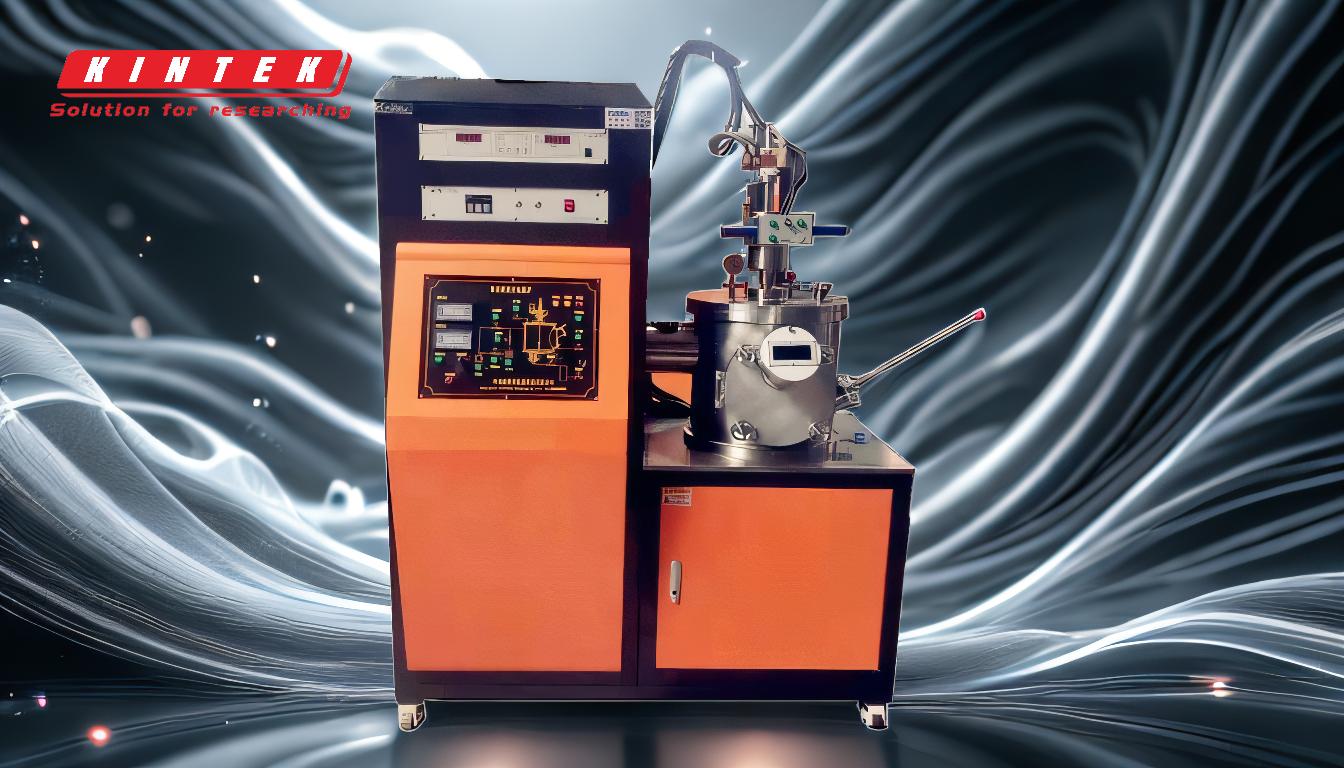
-
Fast Heating Speed and High Production Efficiency
- Induction furnaces heat metals rapidly due to the direct generation of heat within the metal charge itself. This eliminates the need for external heat sources, reducing energy losses and speeding up the melting process.
- The high production efficiency is attributed to the precise control over the heating process, which minimizes downtime and maximizes output.
-
Minimal Oxidation and Decarburization
- The controlled environment of an induction furnace reduces exposure to oxygen, thereby minimizing oxidation and decarburization of the metal.
- This is particularly beneficial for preserving the integrity of valuable alloying elements, ensuring high-quality output.
-
Energy Efficiency and Low Environmental Impact
- Induction furnaces are highly energy-efficient as they generate heat directly within the metal charge, reducing energy waste.
- They produce minimal pollutants, such as dust or toxic vapors, making them a cleaner alternative to traditional furnaces like cupolas.
- The absence of combustion or arcs further reduces the carbon footprint, aligning with sustainable industrial practices.
-
Superior Temperature Control and Uniform Heating
- The electromagnetic induction process ensures precise temperature control, which is critical for achieving consistent melting results.
- The small temperature difference between the core and surface of the metal charge ensures uniform heating, reducing the risk of defects in the final product.
-
Electromagnetic Stirring for Homogeneous Mixtures
- The electromagnetic stirring action in induction furnaces creates a homogeneous mixture of liquid metals, eliminating the need for manual stirring or frequent sampling.
- This feature is particularly advantageous for alloying processes, ensuring uniformity in the final product.
-
Improved Working Conditions and Safety
- Induction furnaces operate without combustible fuels, reducing the risk of accidents and improving workplace safety.
- The absence of open flames or arcs makes the temperature safer to work with, enhancing the overall working environment for operators.
-
Cost Savings on Materials and Maintenance
- The reduced oxidation and minimal melt losses translate to significant savings on raw materials.
- The durable construction of induction furnaces, including helically-wound coils made from refractory materials, ensures long service life and lower maintenance costs.
-
Versatility in Metal Melting and Alloying
- Induction furnaces are suitable for melting and alloying a wide variety of metals, including both ferrous and non-ferrous alloys.
- Their compatibility with additional controls and automation further enhances their versatility in industrial applications.
-
Automation and Advanced Controls
- Modern induction furnaces can be equipped with advanced controls and automation systems, enabling precise thermal cycling and reducing the generation of toxic vapors.
- These features contribute to a more efficient and safer operation, making induction furnaces a preferred choice in advanced manufacturing setups.
-
Cleaner and Safer Operation
- The containment of the melting process within a crucible, combined with water-cooled copper coils, ensures a cleaner and less messy operation.
- The elimination of pollutants and the reduction of hazardous materials contribute to a safer and healthier working environment.
In summary, core induction furnaces offer a combination of efficiency, precision, and environmental benefits that make them superior to traditional melting methods. Their ability to provide uniform heating, reduce material loss, and improve working conditions positions them as a key technology in modern metal processing industries.
Summary Table:
Key Benefit | Description |
---|---|
Fast Heating Speed | Rapid heating due to direct heat generation within the metal charge. |
High Production Efficiency | Precise control minimizes downtime and maximizes output. |
Minimal Oxidation | Controlled environment reduces oxidation, preserving alloying elements. |
Energy Efficiency | Generates heat directly within the metal, reducing energy waste. |
Superior Temperature Control | Ensures uniform heating and consistent melting results. |
Electromagnetic Stirring | Promotes homogeneous mixtures, eliminating manual stirring. |
Improved Safety | No combustible fuels or open flames, enhancing workplace safety. |
Cost Savings | Reduced oxidation and melt losses save on raw materials and maintenance. |
Versatility | Suitable for melting and alloying a wide range of metals. |
Automation | Advanced controls enable precise thermal cycling and reduce toxic vapors. |
Ready to upgrade your metal melting process? Contact us today to learn more about core induction furnaces!