High-frequency heating, particularly induction heating, offers several significant advantages that make it a preferred choice in various manufacturing and industrial applications. Its key benefits include speed, efficiency, compactness, cost-effectiveness, and environmental friendliness. These advantages stem from its ability to generate heat directly within the material, ensuring precise and controlled heating without external contact. Below, a detailed explanation of these advantages is provided.
Key Points Explained:
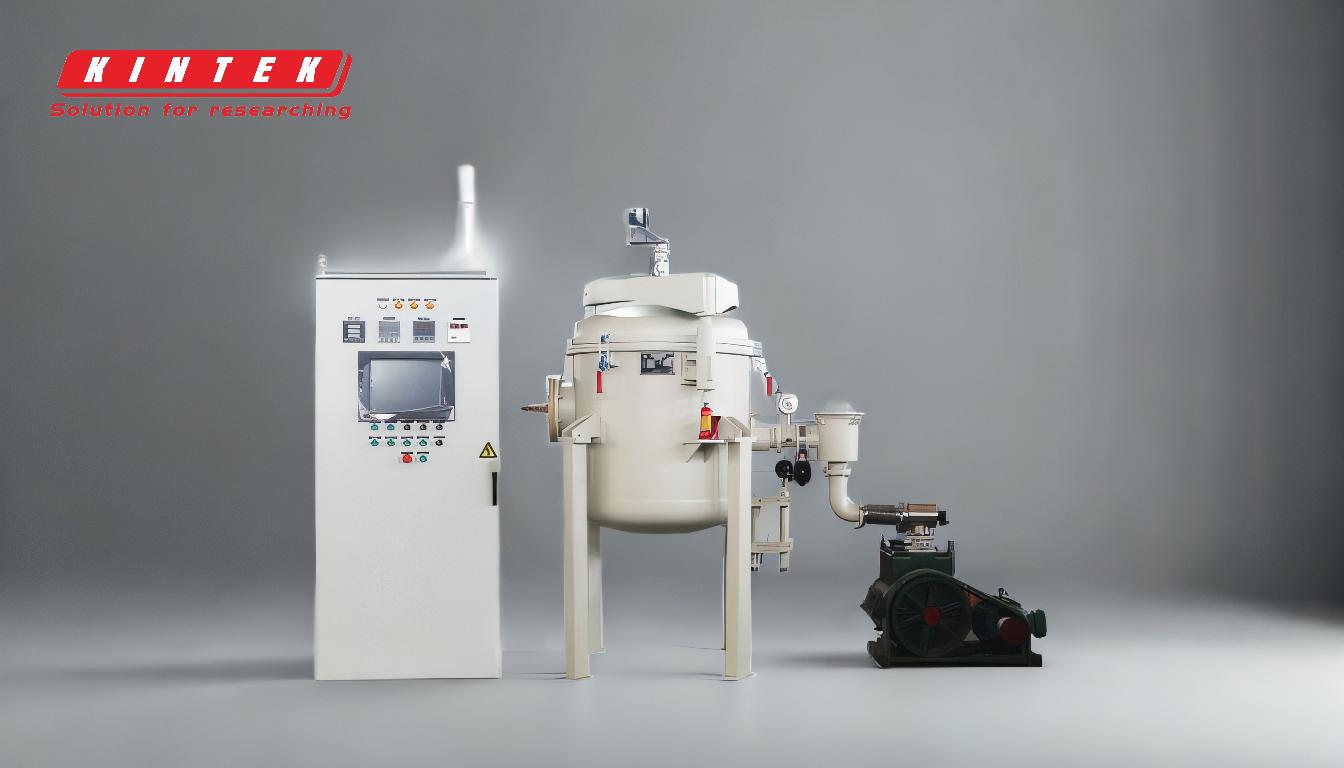
-
Speed and Efficiency
- High-frequency induction heating is extremely fast, as it generates heat directly within the material through electromagnetic induction. This eliminates the need for preheating or external heat transfer, significantly reducing processing times.
- The process is highly efficient because energy is concentrated directly into the target material, minimizing heat loss to the surrounding environment.
-
Compact and Space-Saving Design
- High-frequency heating systems are typically small in size and require minimal installation space compared to traditional heating methods.
- This compactness makes them ideal for integration into existing production lines or for use in facilities with limited space.
-
Cost-Effectiveness
- The process is relatively inexpensive to operate due to its energy efficiency and reduced material waste.
- Maintenance costs are also lower, as there are fewer moving parts and no direct contact between the heating source and the material, reducing wear and tear.
-
Precision and Control
- High-frequency heating allows for precise temperature control, ensuring consistent and uniform heating across the material.
- This level of control is particularly beneficial for applications requiring specific thermal profiles or localized heating.
-
Clean and Non-Polluting Process
- Induction heating is a clean process that does not produce harmful emissions, making it environmentally friendly.
- It eliminates the need for combustion or external heating media, reducing the risk of contamination or pollution.
-
Versatility in Applications
- High-frequency heating is suitable for a wide range of materials, including metals, plastics, and composites.
- It is used in various industries, such as automotive, aerospace, electronics, and food processing, for tasks like hardening, brazing, melting, and annealing.
-
Improved Product Quality
- The precise and controlled nature of high-frequency heating results in higher-quality products with fewer defects.
- For example, in metalworking, it ensures uniform hardness and reduces the risk of warping or cracking.
-
Energy Efficiency
- The direct transfer of energy to the material minimizes energy loss, making high-frequency heating one of the most energy-efficient heating methods available.
- This efficiency translates to lower operational costs and a reduced carbon footprint.
In summary, high-frequency heating stands out as a superior heating method due to its speed, precision, cost-effectiveness, and environmental benefits. Its ability to deliver consistent and high-quality results makes it an invaluable tool in modern manufacturing and industrial processes.
Summary Table:
Advantage | Description |
---|---|
Speed and Efficiency | Generates heat directly within the material, reducing processing times. |
Compact Design | Small size and minimal space requirements for easy integration. |
Cost-Effectiveness | Low operational and maintenance costs due to energy efficiency. |
Precision and Control | Ensures consistent and uniform heating for high-quality results. |
Clean Process | No harmful emissions, making it environmentally friendly. |
Versatility | Suitable for metals, plastics, and composites across various industries. |
Improved Product Quality | Reduces defects and ensures uniform hardness in materials. |
Energy Efficiency | Minimizes energy loss, lowering operational costs and carbon footprint. |
Ready to enhance your manufacturing process with high-frequency heating? Contact us today to learn more!