Induction hardening is a heat treatment process that uses electromagnetic induction to heat and harden the surface of metal components. It is widely used in various industries due to its ability to selectively harden specific areas of a part, improving wear resistance, strength, and durability while maintaining the core's toughness. Applications of induction hardening span across automotive, aerospace, manufacturing, and tooling industries, among others. Below, we explore the key applications and benefits of this process.
Key Points Explained:
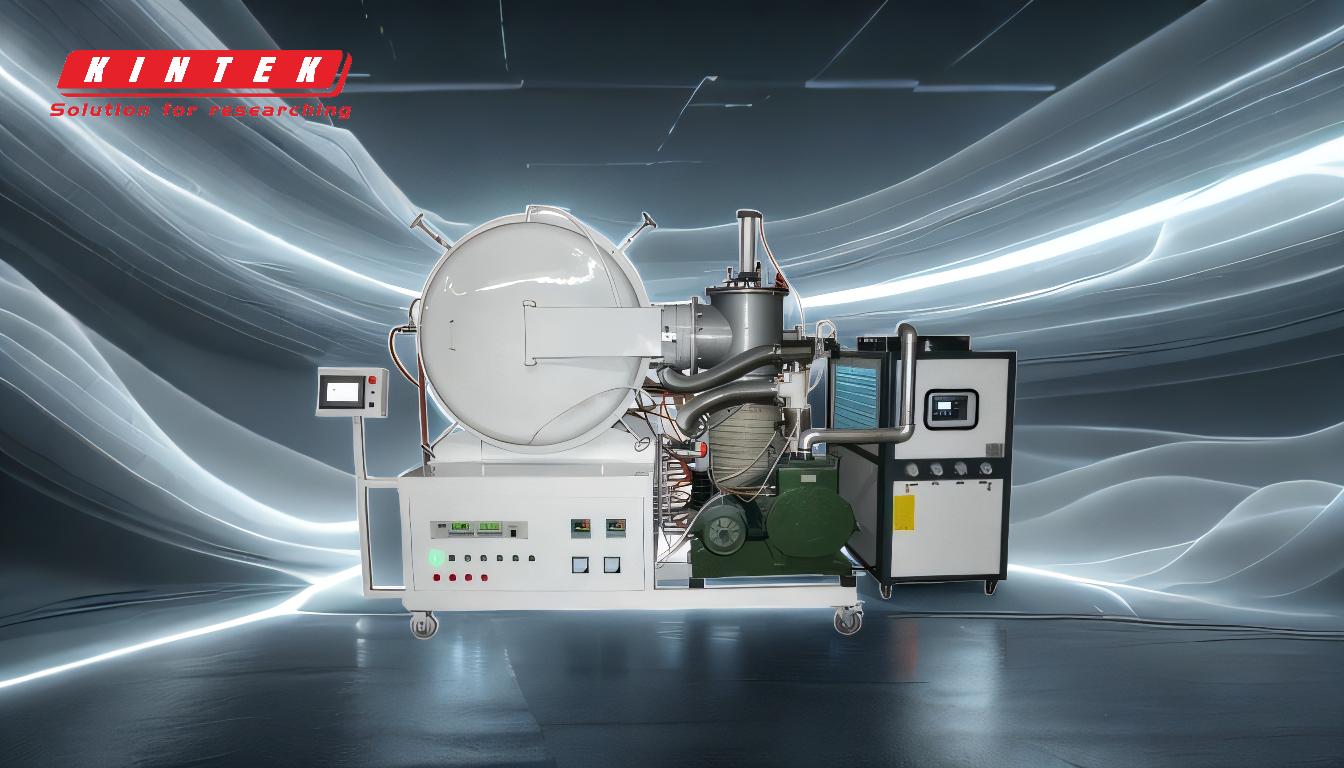
-
Automotive Industry Applications
Induction hardening is extensively used in the automotive sector to enhance the performance and longevity of critical components.- Engine Components: Crankshafts, camshafts, and connecting rods are often induction-hardened to withstand high stress and wear.
- Transmission Parts: Gears, shafts, and splines benefit from localized hardening, improving their resistance to fatigue and surface wear.
- Steering and Suspension Systems: Components like ball joints, tie rods, and kingpins are hardened to ensure durability under repetitive loads.
This process ensures that these parts can endure harsh operating conditions, such as high temperatures and mechanical stress, while maintaining their structural integrity.
-
Aerospace Industry Applications
In aerospace, induction hardening is used to improve the performance of components subjected to extreme conditions.- Landing Gear Components: Parts like struts and axles are hardened to withstand heavy loads and impact forces during landing.
- Engine Parts: Turbine blades and shafts are treated to enhance their resistance to wear and thermal stress.
- Fasteners: Bolts, nuts, and screws are induction-hardened to ensure they can handle high tension and vibration.
The precision of induction hardening allows for targeted treatment of critical areas without affecting the overall structure of the component.
-
Manufacturing and Tooling Applications
Induction hardening is a key process in the production of tools and machinery parts.- Cutting Tools: Drills, saw blades, and milling cutters are hardened to improve their cutting efficiency and lifespan.
- Dies and Molds: Induction hardening enhances the wear resistance of dies and molds used in metal forming and plastic injection molding.
- Machine Components: Gears, rollers, and bearings are treated to reduce wear and extend their operational life.
This process is particularly advantageous for tools and components that require a hard surface to resist abrasion while maintaining a tough core to absorb impacts.
-
Energy and Heavy Machinery Applications
Induction hardening is also applied in the energy sector and heavy machinery industries.- Wind Turbine Components: Gears and shafts in wind turbines are hardened to withstand constant rotation and environmental stress.
- Oil and Gas Equipment: Valves, pumps, and drilling tools are treated to resist corrosion and wear in harsh environments.
- Construction Machinery: Excavator teeth, bulldozer blades, and hydraulic components are hardened to endure heavy use and abrasive conditions.
These applications highlight the versatility of induction hardening in improving the reliability and performance of machinery used in demanding environments.
-
Advantages of Induction Hardening
Induction hardening offers several benefits that make it a preferred choice in various industries:- Selective Hardening: Only specific areas of a component are hardened, preserving the toughness of the core.
- Energy Efficiency: The process is highly efficient, as it directly heats the surface without wasting energy on the entire part.
- Speed and Precision: Induction hardening is fast and can be precisely controlled, making it suitable for high-volume production.
- Reduced Distortion: The localized heating minimizes thermal distortion, reducing the need for post-treatment machining.
- Environmental Benefits: The process produces less waste and emissions compared to traditional hardening methods.
-
Emerging Applications in Additive Manufacturing
Induction heating is also finding applications in advanced manufacturing processes, such as the Rapid Induction Printing method described in the reference.- Metal Additive Manufacturing: Induction heating is used to melt metal feedstock, enabling the creation of complex 3D structures with high energy efficiency.
- Material Efficiency: The process minimizes material waste by precisely melting and depositing metal only where needed.
- Safety and Control: Induction heating offers a safer alternative to laser-based methods, with better control over the heating process.
This innovative use of induction heating demonstrates its potential to revolutionize manufacturing techniques and expand its applications further.
In summary, induction hardening is a versatile and efficient process with a wide range of applications across industries. Its ability to selectively harden components, improve wear resistance, and enhance performance makes it an invaluable technique in modern manufacturing and engineering. From automotive and aerospace to tooling and additive manufacturing, induction hardening continues to play a critical role in advancing technology and improving product quality.
Summary Table:
Industry | Applications |
---|---|
Automotive | Crankshafts, camshafts, gears, ball joints, and more for wear resistance. |
Aerospace | Landing gear, turbine blades, fasteners for extreme condition durability. |
Manufacturing/Tooling | Cutting tools, dies, molds, gears for abrasion resistance and longevity. |
Energy/Heavy Machinery | Wind turbine gears, oil and gas valves, construction machinery parts. |
Additive Manufacturing | Rapid Induction Printing for efficient 3D metal structures. |
Discover how induction hardening can improve your components—contact us today for expert solutions!